siggy_7
Full time tool collector, part time woodworker
A while ago I posted on here for some advice on insuring some structural work I was planning for my house, and I was asked to put some info up when it was all done. So here it is...
Background: Our house is a farming cottage originally built in 1856. The house had a 2 storey extension added to the rear around 20 years ago. On the ground floor, I think the original living room had a patio door to the garden. When the extension was added, I think they just took the frame out to connect the living room to the extension. However, this left a large chunk of wall in the middle of the room effectively dividing it up into two smaller less usable rooms, and also made the original living room very dark. As the original walls of the house are about 360mm thick and solid brick, it also took up a lot of floor space. We wanted to remove most of this wall to open up the room and make the space more usable.
You can also see in the photos a couple of other problems with the old lounge. Firstly, the original floor in the old lounge was wood block, but having been laid a long time ago on a slab with no DPM and subsequently been covered up by underlay and carpet the wood had rotted away. Also, the old walls had been re-plastered in gypsum based plaster. As the old parts of the house have no constructional DPM (although we think a liquid one was injected at some point) this was causing big problems with moisture damage to the plaster. The wiring was also in quite a poor state, and we wanted to reconfigure and add to a lot of the wiring in the room. Given that a lot of the works were inter-related, we decided that the best thing to do was to bite the bullet and do the whole lot at once.
Structural modifications
The first job was to prop the ceiling before we could remove the wall and install a steel RSJ. The old part of the house has joists running into the wall, whereas the extension has joists running parallel to the wall. On the first floor, there is about 400mm of wall on either side to support the roof. By propping the ceiling on the old house side, we supported all the joists that were originally load bearing on the old wall; additionally as these ran into the old wall on either side we effectively made use of the joists as temporary strongboys to support the short length of wall either side of the opening on the first floor.
Taking the wall out and installing the new steels took 2 days of work from me and two family members. The wall was pretty solid and took some shifting in places! The new steel, specified by a structural engineer, was a pair of 152x152mm I-beams bolted together at 600mm centres resting on 400mmx150mm concrete padstones either end. Total unsupported span is about 3.6m.
I had to put back a few bricks on top of the steel to support the small bits of wall above. Laying bricks from the top course down is quite challenging, particularly with tight access!
I then drove steel shims between the beam and the wall plate under every joist so that they would be supported by the beam when the props were removed.
No props, and it hasn't fallen down! I was actually quite surprised that there was no movement or creaking when I took the props away, clearly the shims did a good job.
At this point, it was all signed off by building control and the boarding up and plastering could commence. Post to be continued...
Background: Our house is a farming cottage originally built in 1856. The house had a 2 storey extension added to the rear around 20 years ago. On the ground floor, I think the original living room had a patio door to the garden. When the extension was added, I think they just took the frame out to connect the living room to the extension. However, this left a large chunk of wall in the middle of the room effectively dividing it up into two smaller less usable rooms, and also made the original living room very dark. As the original walls of the house are about 360mm thick and solid brick, it also took up a lot of floor space. We wanted to remove most of this wall to open up the room and make the space more usable.
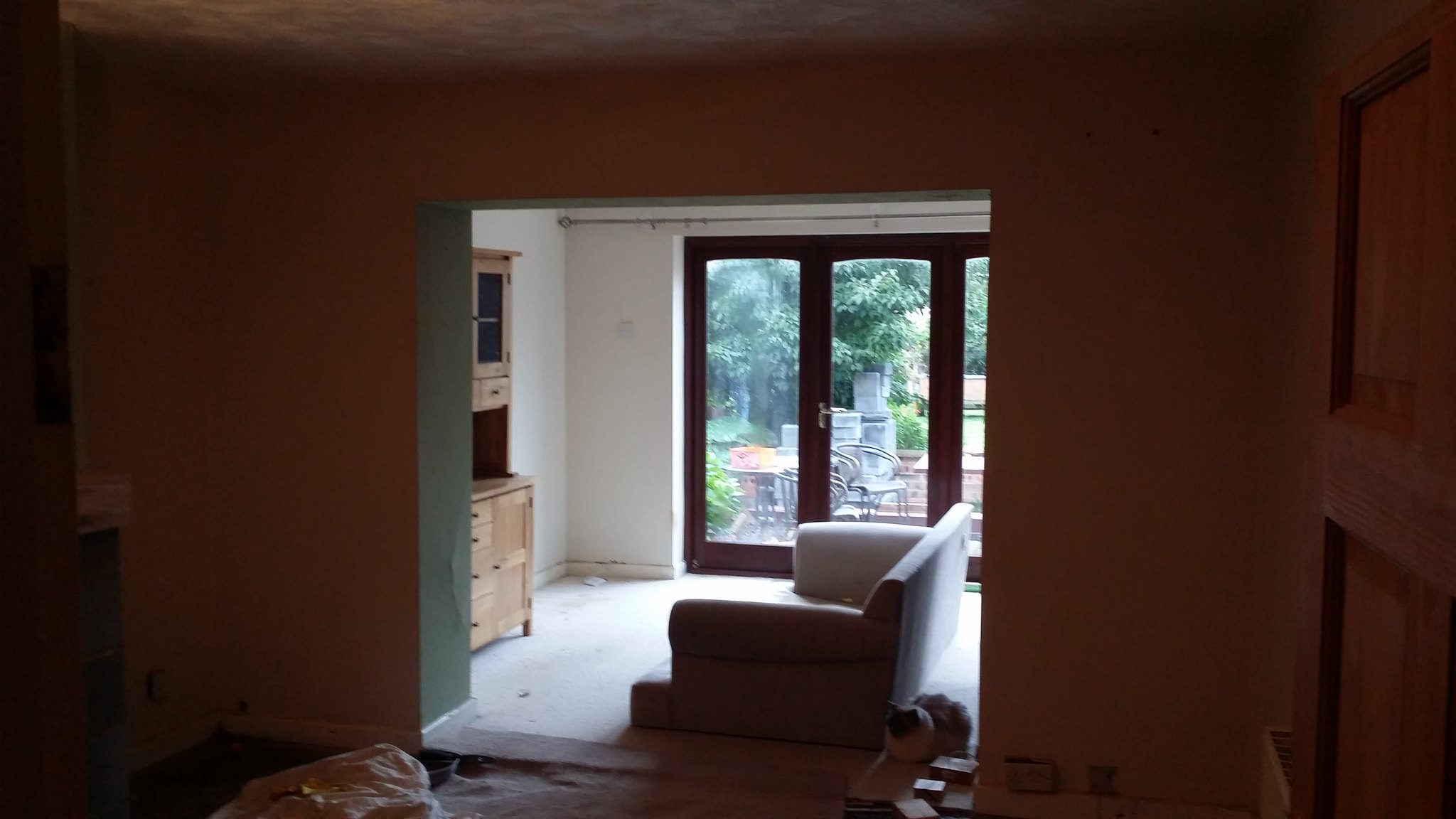
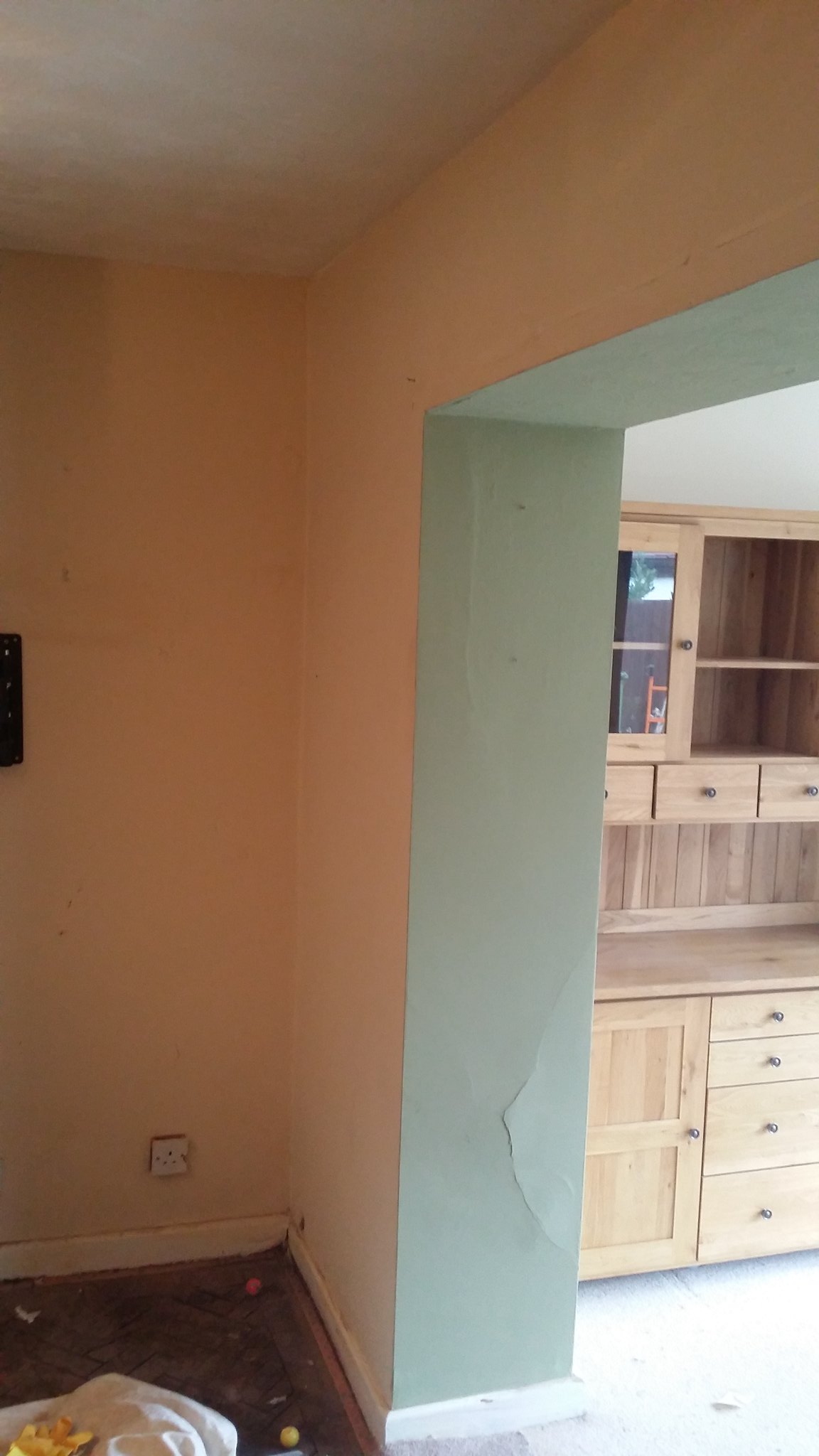
You can also see in the photos a couple of other problems with the old lounge. Firstly, the original floor in the old lounge was wood block, but having been laid a long time ago on a slab with no DPM and subsequently been covered up by underlay and carpet the wood had rotted away. Also, the old walls had been re-plastered in gypsum based plaster. As the old parts of the house have no constructional DPM (although we think a liquid one was injected at some point) this was causing big problems with moisture damage to the plaster. The wiring was also in quite a poor state, and we wanted to reconfigure and add to a lot of the wiring in the room. Given that a lot of the works were inter-related, we decided that the best thing to do was to bite the bullet and do the whole lot at once.
Structural modifications
The first job was to prop the ceiling before we could remove the wall and install a steel RSJ. The old part of the house has joists running into the wall, whereas the extension has joists running parallel to the wall. On the first floor, there is about 400mm of wall on either side to support the roof. By propping the ceiling on the old house side, we supported all the joists that were originally load bearing on the old wall; additionally as these ran into the old wall on either side we effectively made use of the joists as temporary strongboys to support the short length of wall either side of the opening on the first floor.
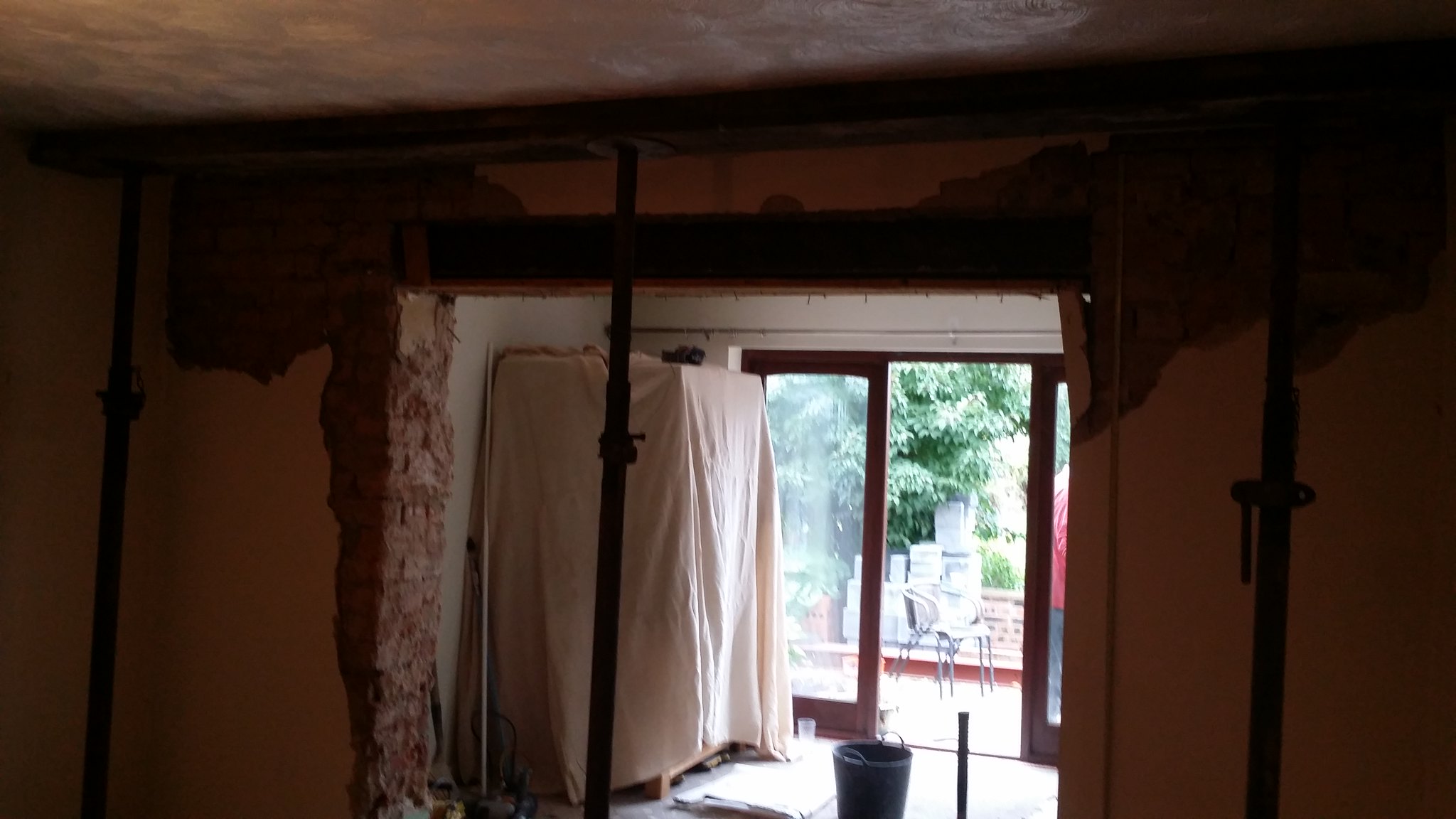
Taking the wall out and installing the new steels took 2 days of work from me and two family members. The wall was pretty solid and took some shifting in places! The new steel, specified by a structural engineer, was a pair of 152x152mm I-beams bolted together at 600mm centres resting on 400mmx150mm concrete padstones either end. Total unsupported span is about 3.6m.
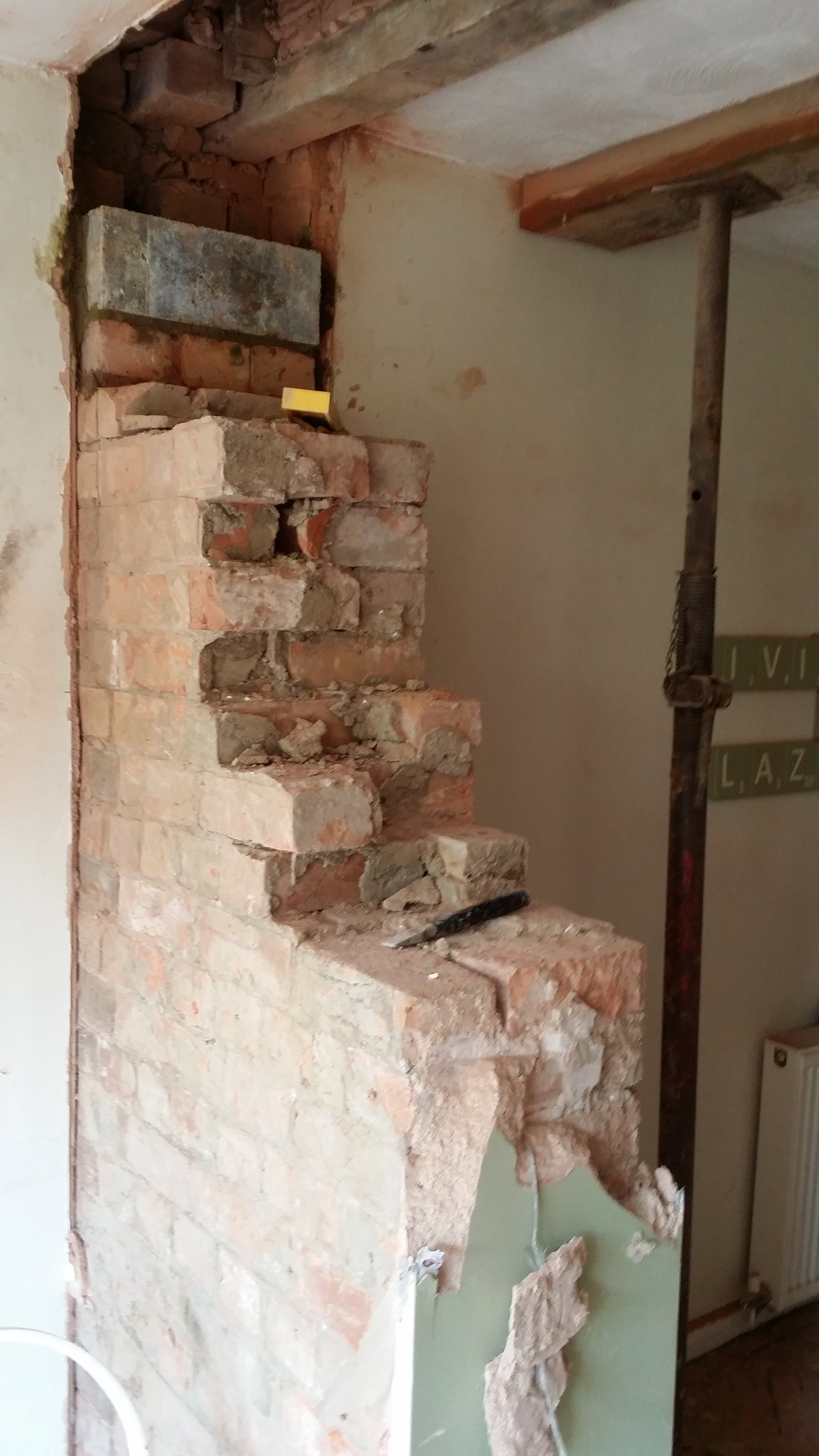
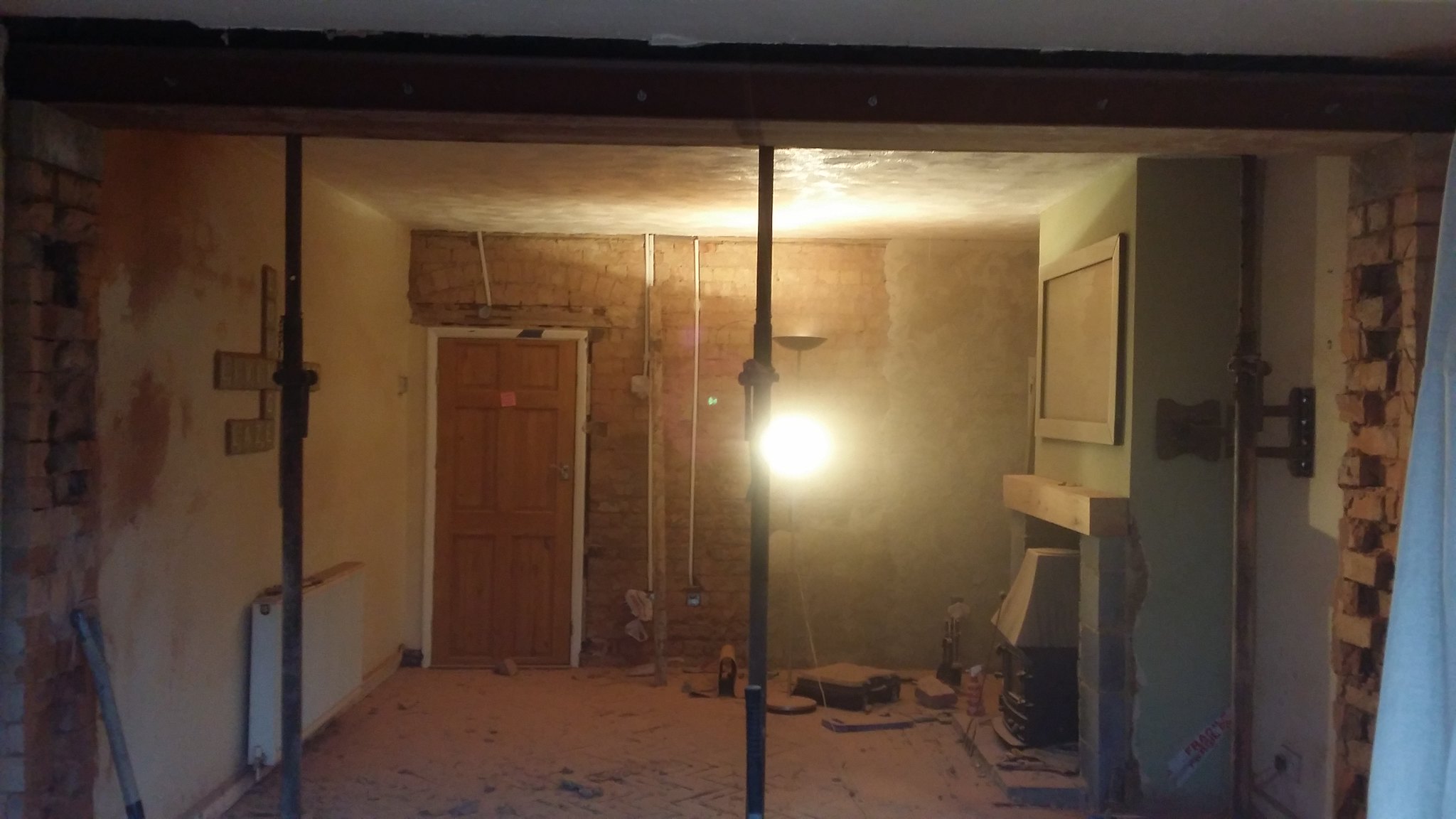
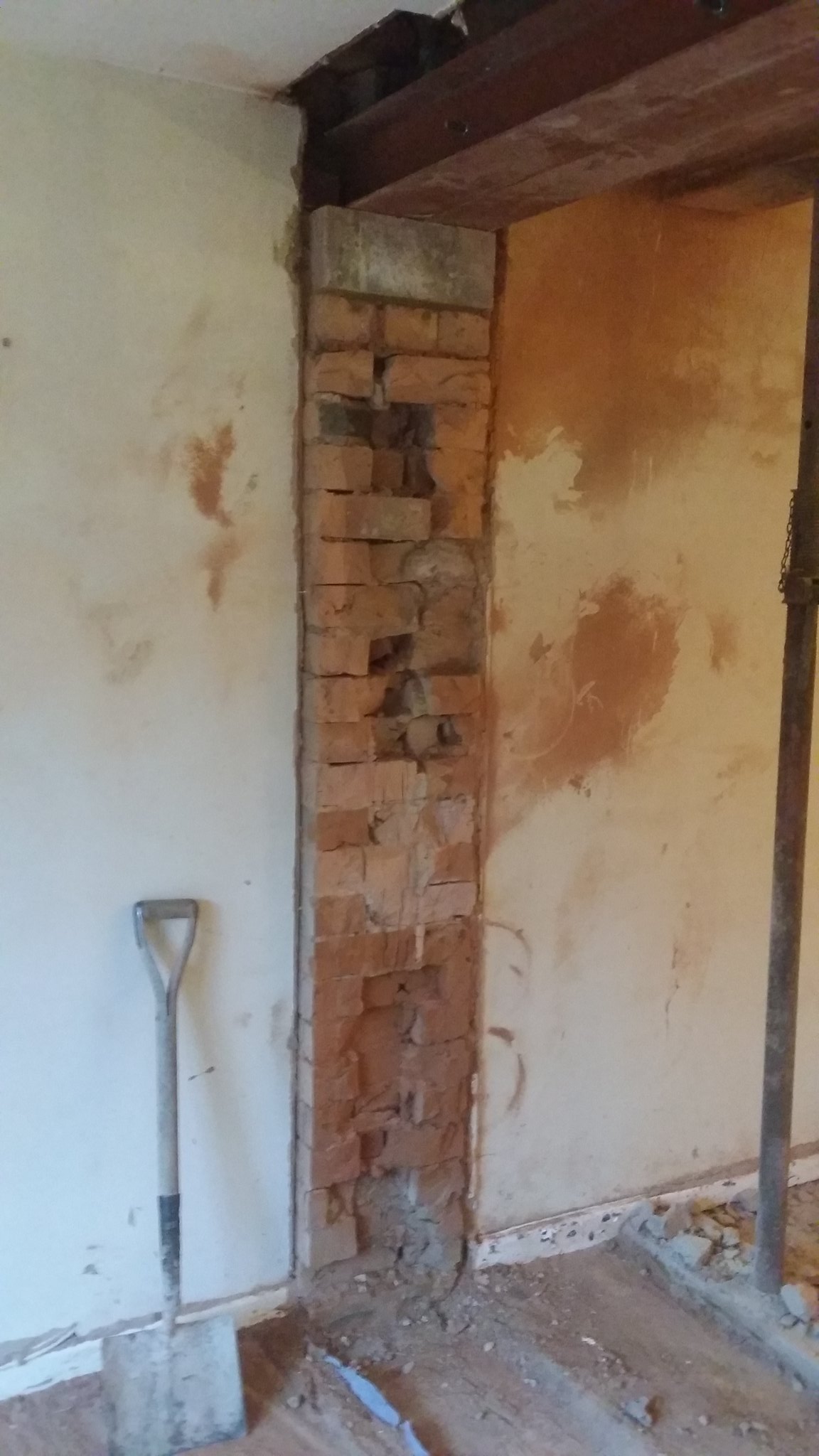
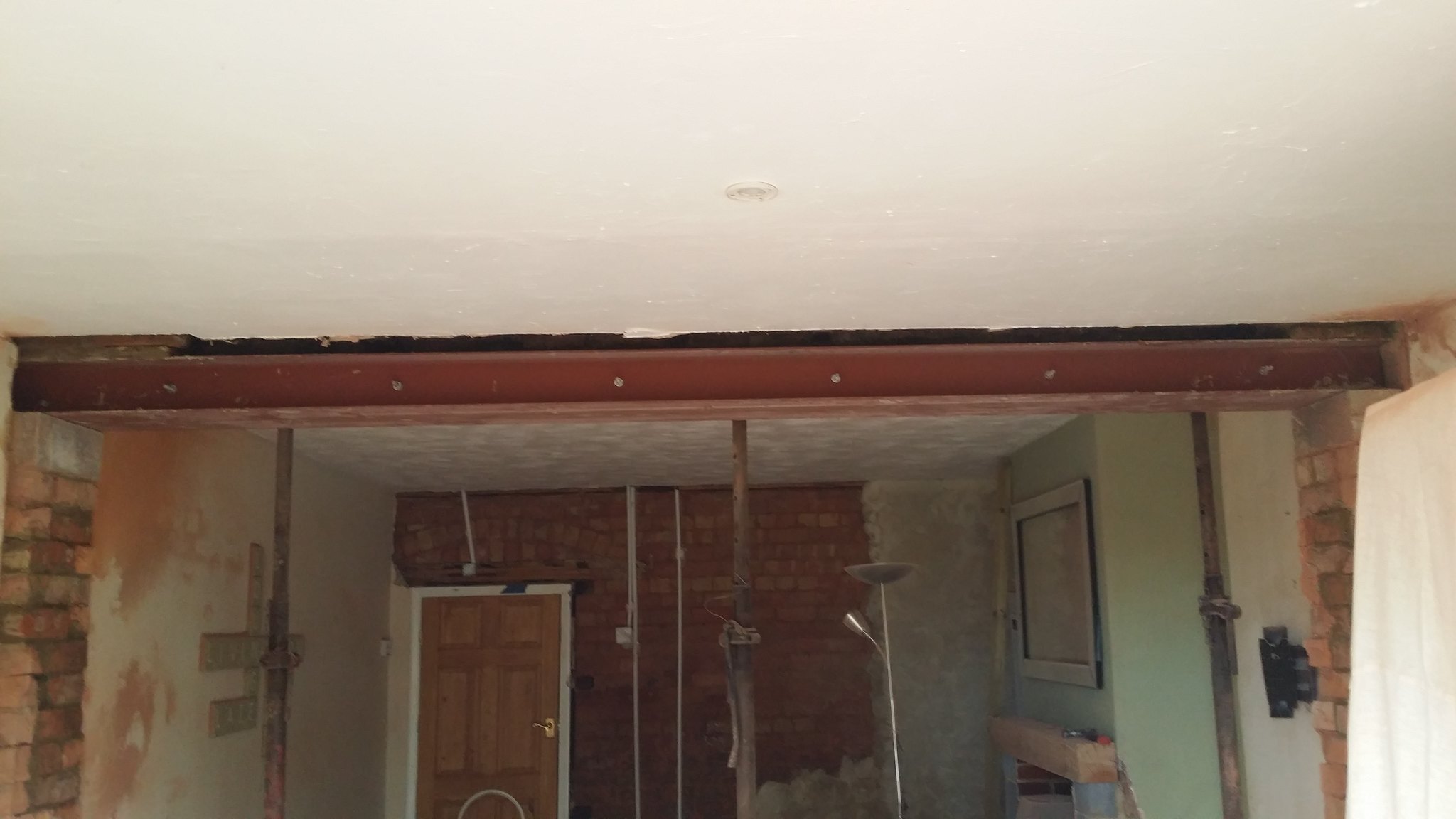
I had to put back a few bricks on top of the steel to support the small bits of wall above. Laying bricks from the top course down is quite challenging, particularly with tight access!
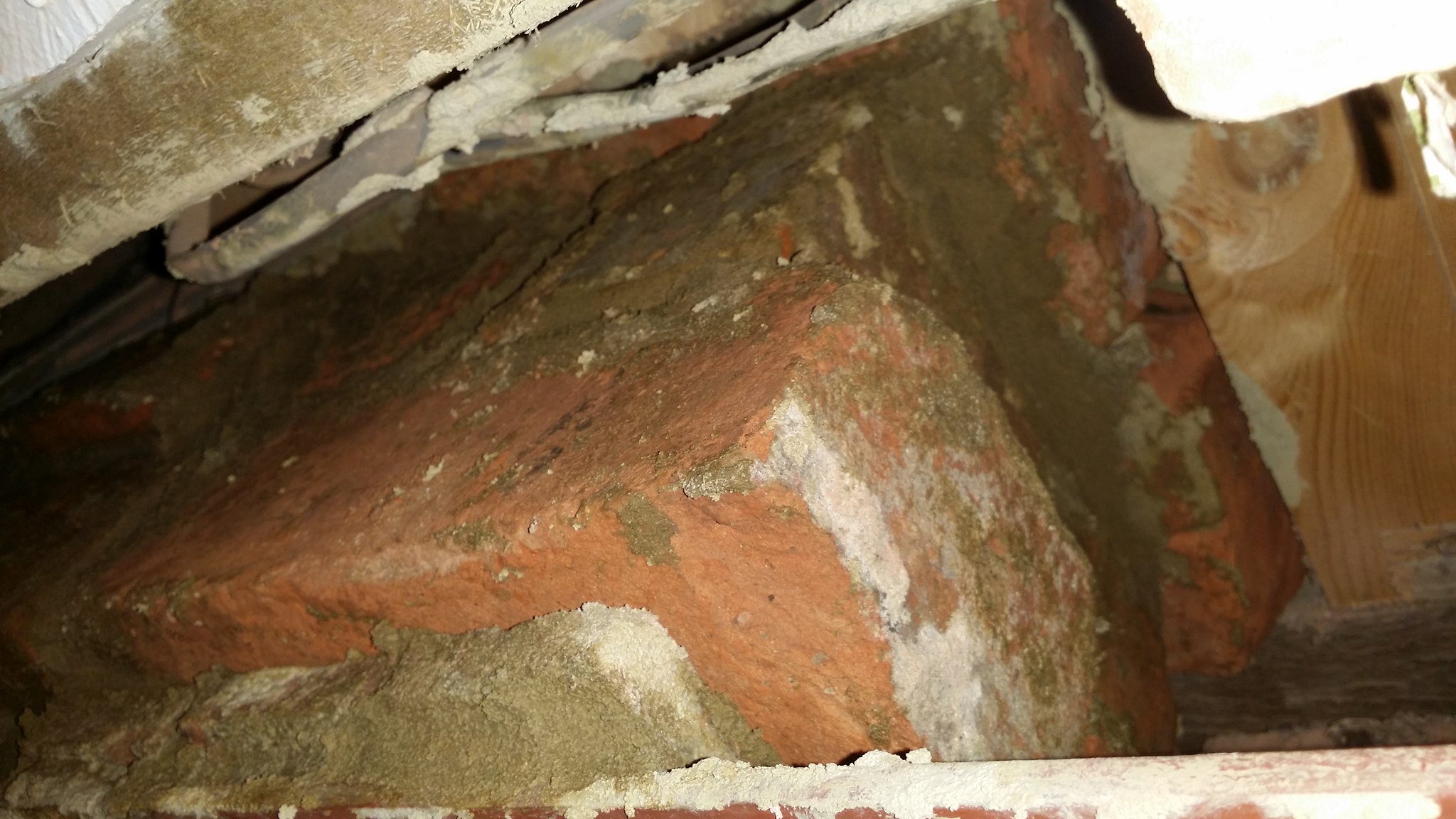
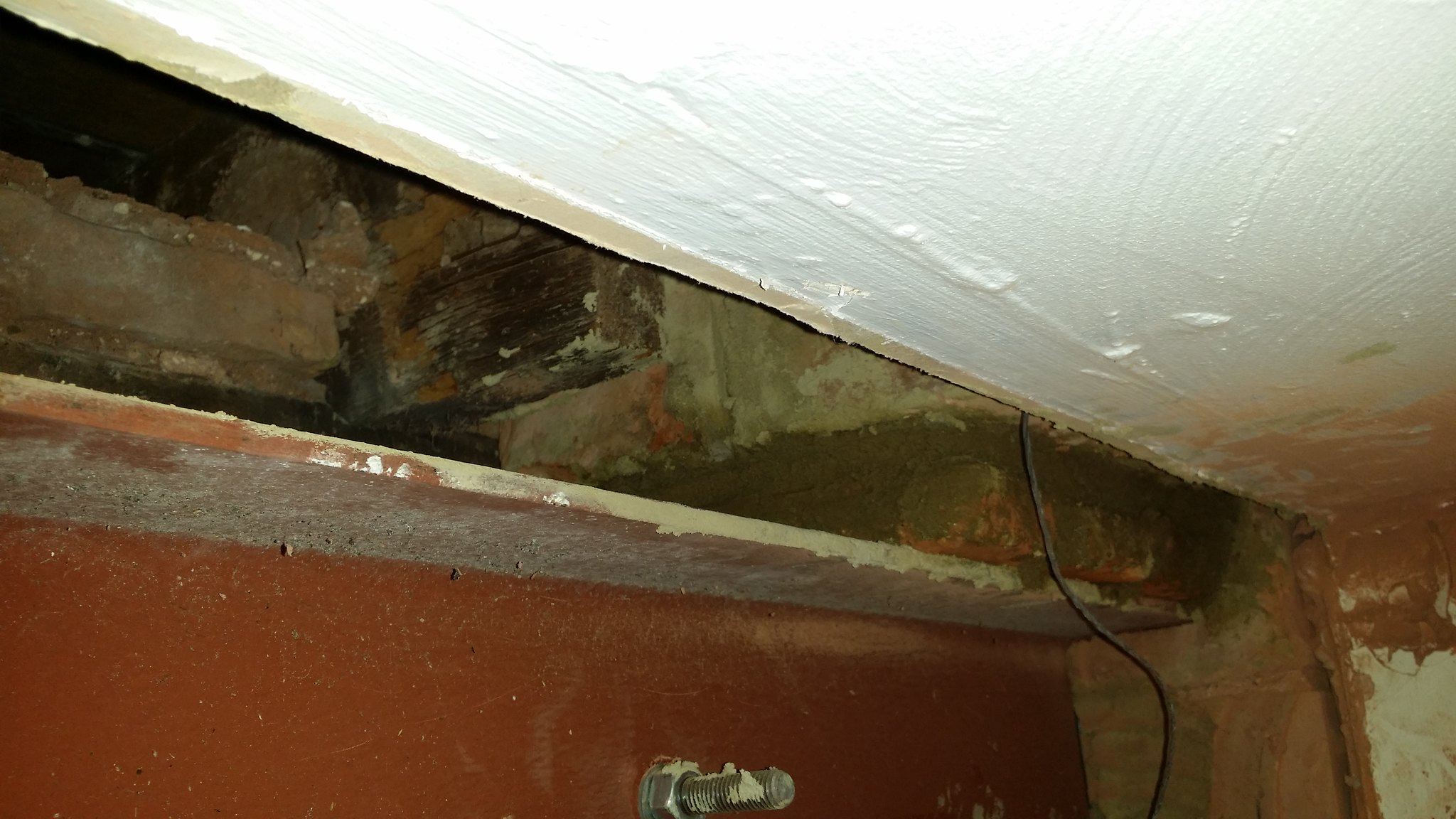
I then drove steel shims between the beam and the wall plate under every joist so that they would be supported by the beam when the props were removed.
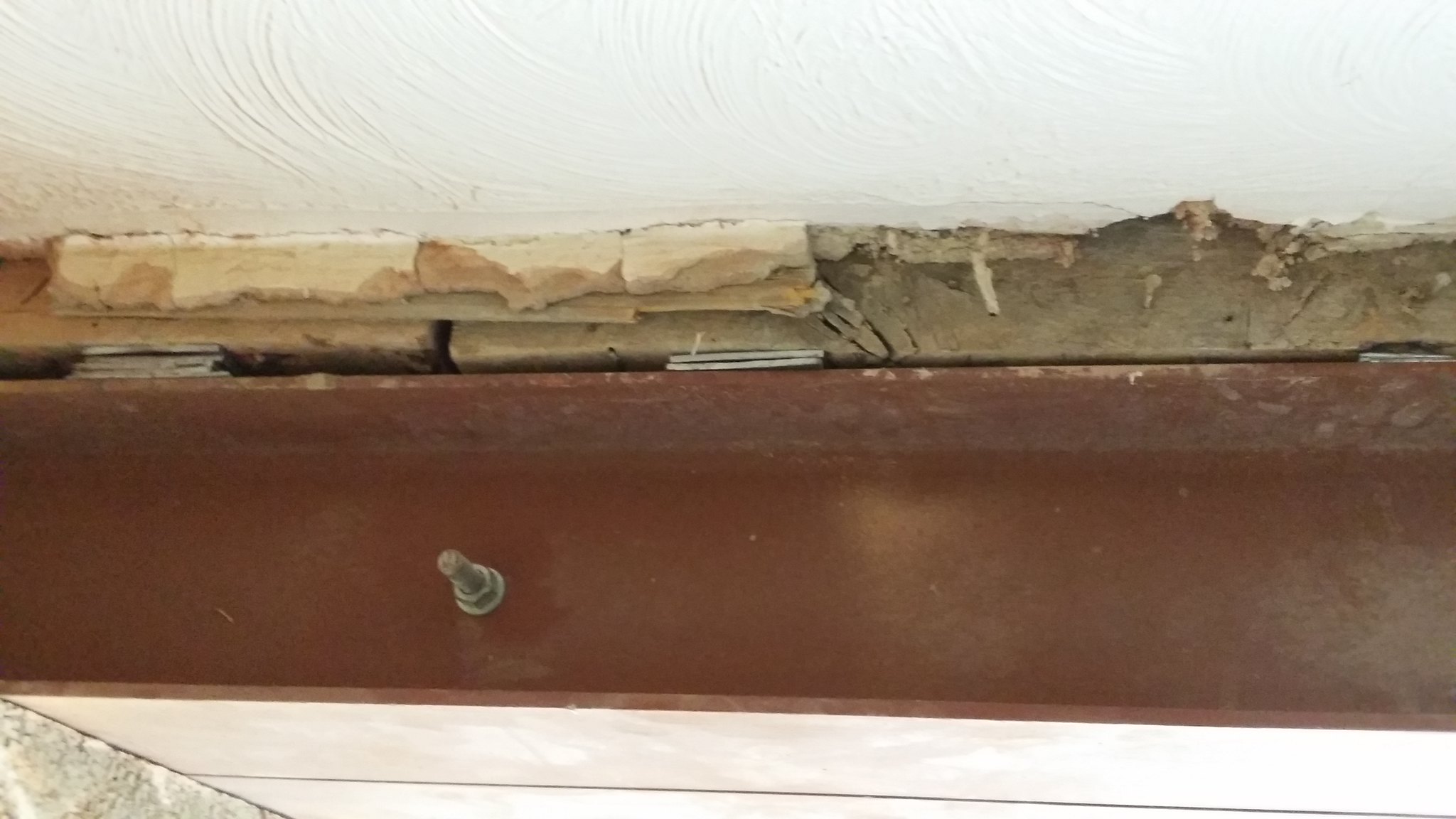
No props, and it hasn't fallen down! I was actually quite surprised that there was no movement or creaking when I took the props away, clearly the shims did a good job.
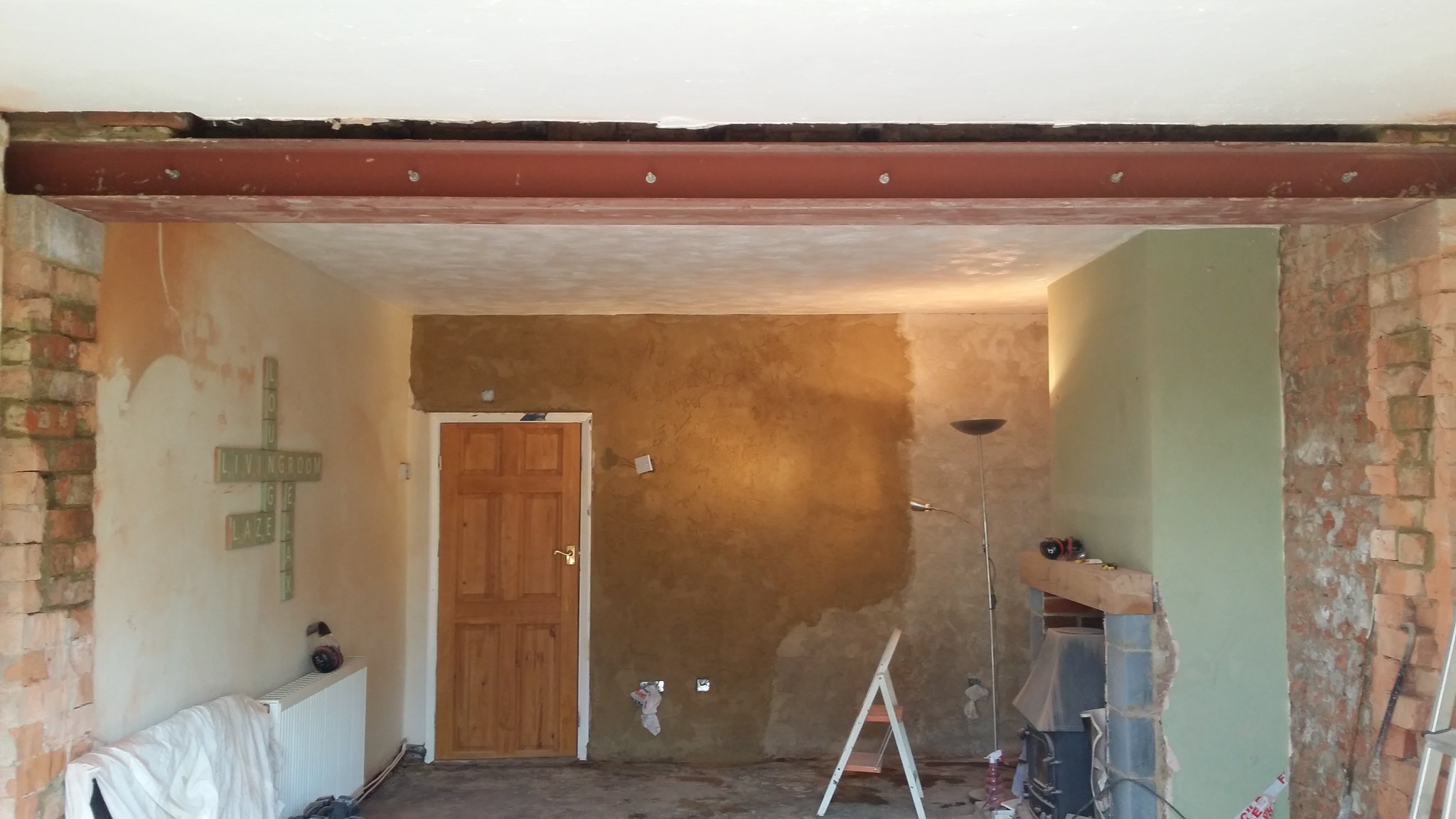
At this point, it was all signed off by building control and the boarding up and plastering could commence. Post to be continued...