devonwoody
Established Member
Preview of box description
Another new design for me but no doubt there are others around.
Information on geometrical details was given me by members of the Australian forum.
(To create a cyclinder using 16 pieces of timber, divide 360 degrees by 16 and obtain the figure of 22.5%, half this amount and you need a cutting angle of 11.25% each side of strip. This I obtained using a protractor finding 11% and estimating the odd .25 figur, I then made a former which I set the tilt of blade.)
I found four pieces of contrasting coloured timber, (B.walnut, Meranti, Sapelle, and Br. Mahogany) plus American Ash for white.
I prepared and reduced to strips in my usual fashion using the strip jig on the tablesaw.
Set out on my flat board in colour choice.
Put he 11.25% angle to each strip using the stripping jig again with the blade angle set this time.
Placed on my flat board with masking tape under, this means when the tube is rolled up with glue on each edge. the tape holds while glue sets.
In addition I did not glue between sections 4 & 5 or 13 & 14 so that I would have a lid formed which is removable when tape is removed after the other glued sections have set.
A rebate was put on each end of strip to close up tube at a later date.
Tube glued and awaiting set
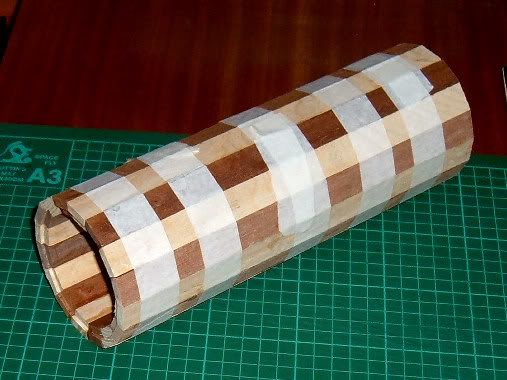
Another new design for me but no doubt there are others around.
Information on geometrical details was given me by members of the Australian forum.
(To create a cyclinder using 16 pieces of timber, divide 360 degrees by 16 and obtain the figure of 22.5%, half this amount and you need a cutting angle of 11.25% each side of strip. This I obtained using a protractor finding 11% and estimating the odd .25 figur, I then made a former which I set the tilt of blade.)
I found four pieces of contrasting coloured timber, (B.walnut, Meranti, Sapelle, and Br. Mahogany) plus American Ash for white.
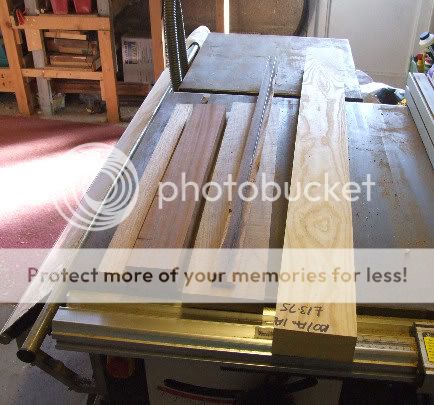
I prepared and reduced to strips in my usual fashion using the strip jig on the tablesaw.
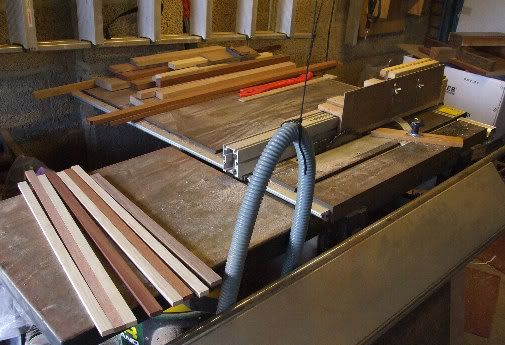
Set out on my flat board in colour choice.
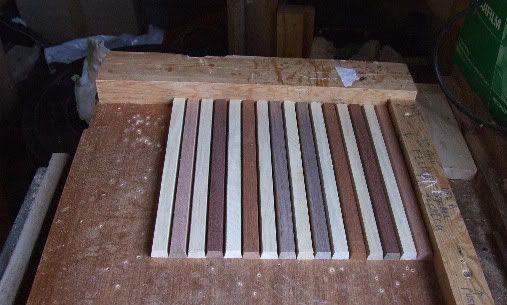
Put he 11.25% angle to each strip using the stripping jig again with the blade angle set this time.
Placed on my flat board with masking tape under, this means when the tube is rolled up with glue on each edge. the tape holds while glue sets.
In addition I did not glue between sections 4 & 5 or 13 & 14 so that I would have a lid formed which is removable when tape is removed after the other glued sections have set.
A rebate was put on each end of strip to close up tube at a later date.
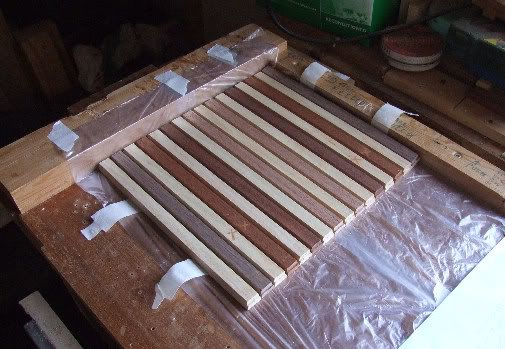
Tube glued and awaiting set
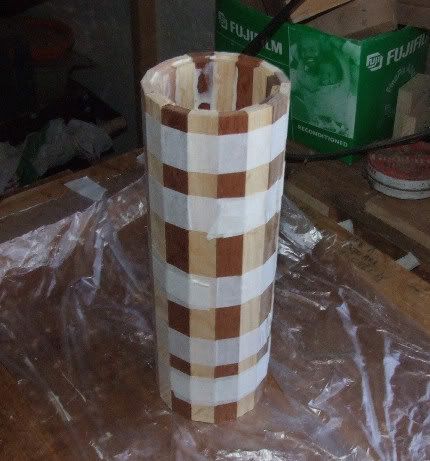