Chronosoft
Established Member
Hi,
I thought I would take a little time to review some of the courses that I attended with at Chris Tribe's workshop in Ilkley. I have been a woodworker since 2000 and it started out as a way to occupy some downtime when I wasn't writing software. I attended a basic skills course at a local college and pretty much never bothered with another lesson, I set my own workshop up and hacked at finding my own way to work and of course using the magazines and books.
I bumped into Chris at the 2013 North of England Woodworking show and saw some absolutely beautiful work on display, I was more shocked when he told me his students had actually built them. I thought there is no way I would be able to build anything like this but a curved stool caught my eye. I asked Chris what course was the stool covered on and he mentioned it was the advanced laminating and veneering. I did think that this was way beyond my skill set but hopefully one day. I gave it some thought and looking through his list he had a basic skills 1 to 3 that covered sharpening and preparation of tools, planing and M & T joints and finally Dovetailing. I thought it would be nice to go over the basics and plug any holes I had in my skill set (and there were a few gaping ones). It wanted to make sure I had a good foundations to build on so in November 2014 I started my first course. I remember hand cutting a really sloppy Mortice and Tenon (most of mine up to that point were machined) and I said to Chris, well its not a million miles away and he looked at me and said, so David, it doesn't fit then! I think the penny dropped at this point that nearly just wasn't good enough, it is perfect or it isn't. I realised if I had any hope of making that curved stool I needed to raise my game and make things as perfectly as possible. The first three courses were excellent, they covered the basics in enough detail to send you home with a set of razor sharp chisels and a lovely set of dovetail bookends. The courses were perfectly paced over three weekends and we managed to finish everything on time.
I took a bit of a left turn and did the modern cabinet making course as I was planning to build some fitted wardrobes and If time permitted my own kitchen (a new born baby has put the latter option off the table) and then the finishing course which I did with my wife who absolutely loved it. The modern cabinet making course was really excellent, I learned an awful lot about the preparation of panel products and the use of a spindle moulder. It was doubly helpful as I had bought a Felder combination and I wasn't too sure about the spindle side of things. However the course covered setup and safe use of the machine so it was a bonus to me. The only problem was that I now really really wanted a Domino to help me make the cabinets (another toy to smuggle into the workshop).
The finishing course covered the uses of french polish (nicely demystified by Chris), Danish oils and water based finishes, also the preparation of a surface before finish is applied. Finishing was always an afterthought for me but this course really gave me a good grounding on what is a vital element of making a piece.
After I had come home and practiced my newly improved skill set, I booked onto the advanced laminating and veneering course. This was entirely new territory for me, I had never done anything like this. It was a week long course just like the modern cabinet making and I imagined we would need every hour. I was on the course with two lovely gentleman from North Yorkshire who I had the pleasure of having lunch with everyday. Up until that time I had never seen anyone eat a sandwich with a knife and fork but this was a week of firsts for me. We started out by making the formers for the top and the legs. Selecting veneers for the table and cutting these as a quarter or a half to get visually pleasing results. We covered flattening and preparing the surface for glue. Once that had been done, we started looking at jig making for cutting angles (most important). We proceeded to then glue up the top and legs covering the choice of correct glues for the job and use of the vacuum press. Once the forms had cured we could start machining them with the jigs and getting them lipped. We then moved onto the use of inlay to dress the area where the veneer met solid, this was done in ebony stringing and was the most delicate part of the process. I actually used a card scraper for the first time and its now a really invaluable part of my toolkit.
We finished the piece off by scraping the whole thing level and eased the edges. The final element was to glue it all together and give it a finish. I managed to get mine done at the workshop but a few others who had fallen behind finished theirs off at home. I remember standing back and looking at it as a complete piece thinking I have actually made this! I never thought I would have the skill set or actually the patience but once it is broken down into its constituent parts, its a small set of logical steps that have to be completed (perfectly
).
I think something needs to be said about the scheduling of the course once you are there. You are paying a premium for Chris' time and experience and he expects you to crack on a keep up the pace. You leave at the end of the week physically tired as you have been working flat out to learn and make, but the sense of pride is immense that you have crafted something so lovely, you soon forget how much you ache. However, its very manageable and I am the proof of that pudding.
Chris himself is a very nice and approachable guy. He has a great sense of humour, although a little dry (the north has rubbed off on him) but I don't share his taste in music. I think radio 3 and nothing beyond 1975 are on his playlist, but oddly enough it matched the work we were doing. The workshop is very well equipped and is an old mill building which has its own old world charm. I must admit I really looked forward to getting in there very early and cracking on, it was a shame when it was over as the whole experience was extremely enjoyable. I also met some really lovely people on the course.
Completed project without a finish applied, I still look at it with a degree of awe!
I entered the stool into a local exhibition and won first prize!!!
What next, well good question. I have just renovated the whole house over the last 6 months to get ready for our first baby so nothing for the time but I have had my eye on making my own sliding table and chairs. I was thinking about booking some special tuition and making the table over a few months but Chris' new chair making course looks like an amazing challenge and there is his piston fit draw making course which I really would love to do. So that's another two weeks spoken for.
I thought I would take a little time to review some of the courses that I attended with at Chris Tribe's workshop in Ilkley. I have been a woodworker since 2000 and it started out as a way to occupy some downtime when I wasn't writing software. I attended a basic skills course at a local college and pretty much never bothered with another lesson, I set my own workshop up and hacked at finding my own way to work and of course using the magazines and books.
I bumped into Chris at the 2013 North of England Woodworking show and saw some absolutely beautiful work on display, I was more shocked when he told me his students had actually built them. I thought there is no way I would be able to build anything like this but a curved stool caught my eye. I asked Chris what course was the stool covered on and he mentioned it was the advanced laminating and veneering. I did think that this was way beyond my skill set but hopefully one day. I gave it some thought and looking through his list he had a basic skills 1 to 3 that covered sharpening and preparation of tools, planing and M & T joints and finally Dovetailing. I thought it would be nice to go over the basics and plug any holes I had in my skill set (and there were a few gaping ones). It wanted to make sure I had a good foundations to build on so in November 2014 I started my first course. I remember hand cutting a really sloppy Mortice and Tenon (most of mine up to that point were machined) and I said to Chris, well its not a million miles away and he looked at me and said, so David, it doesn't fit then! I think the penny dropped at this point that nearly just wasn't good enough, it is perfect or it isn't. I realised if I had any hope of making that curved stool I needed to raise my game and make things as perfectly as possible. The first three courses were excellent, they covered the basics in enough detail to send you home with a set of razor sharp chisels and a lovely set of dovetail bookends. The courses were perfectly paced over three weekends and we managed to finish everything on time.
I took a bit of a left turn and did the modern cabinet making course as I was planning to build some fitted wardrobes and If time permitted my own kitchen (a new born baby has put the latter option off the table) and then the finishing course which I did with my wife who absolutely loved it. The modern cabinet making course was really excellent, I learned an awful lot about the preparation of panel products and the use of a spindle moulder. It was doubly helpful as I had bought a Felder combination and I wasn't too sure about the spindle side of things. However the course covered setup and safe use of the machine so it was a bonus to me. The only problem was that I now really really wanted a Domino to help me make the cabinets (another toy to smuggle into the workshop).
The finishing course covered the uses of french polish (nicely demystified by Chris), Danish oils and water based finishes, also the preparation of a surface before finish is applied. Finishing was always an afterthought for me but this course really gave me a good grounding on what is a vital element of making a piece.
After I had come home and practiced my newly improved skill set, I booked onto the advanced laminating and veneering course. This was entirely new territory for me, I had never done anything like this. It was a week long course just like the modern cabinet making and I imagined we would need every hour. I was on the course with two lovely gentleman from North Yorkshire who I had the pleasure of having lunch with everyday. Up until that time I had never seen anyone eat a sandwich with a knife and fork but this was a week of firsts for me. We started out by making the formers for the top and the legs. Selecting veneers for the table and cutting these as a quarter or a half to get visually pleasing results. We covered flattening and preparing the surface for glue. Once that had been done, we started looking at jig making for cutting angles (most important). We proceeded to then glue up the top and legs covering the choice of correct glues for the job and use of the vacuum press. Once the forms had cured we could start machining them with the jigs and getting them lipped. We then moved onto the use of inlay to dress the area where the veneer met solid, this was done in ebony stringing and was the most delicate part of the process. I actually used a card scraper for the first time and its now a really invaluable part of my toolkit.
We finished the piece off by scraping the whole thing level and eased the edges. The final element was to glue it all together and give it a finish. I managed to get mine done at the workshop but a few others who had fallen behind finished theirs off at home. I remember standing back and looking at it as a complete piece thinking I have actually made this! I never thought I would have the skill set or actually the patience but once it is broken down into its constituent parts, its a small set of logical steps that have to be completed (perfectly
I think something needs to be said about the scheduling of the course once you are there. You are paying a premium for Chris' time and experience and he expects you to crack on a keep up the pace. You leave at the end of the week physically tired as you have been working flat out to learn and make, but the sense of pride is immense that you have crafted something so lovely, you soon forget how much you ache. However, its very manageable and I am the proof of that pudding.
Chris himself is a very nice and approachable guy. He has a great sense of humour, although a little dry (the north has rubbed off on him) but I don't share his taste in music. I think radio 3 and nothing beyond 1975 are on his playlist, but oddly enough it matched the work we were doing. The workshop is very well equipped and is an old mill building which has its own old world charm. I must admit I really looked forward to getting in there very early and cracking on, it was a shame when it was over as the whole experience was extremely enjoyable. I also met some really lovely people on the course.
Completed project without a finish applied, I still look at it with a degree of awe!
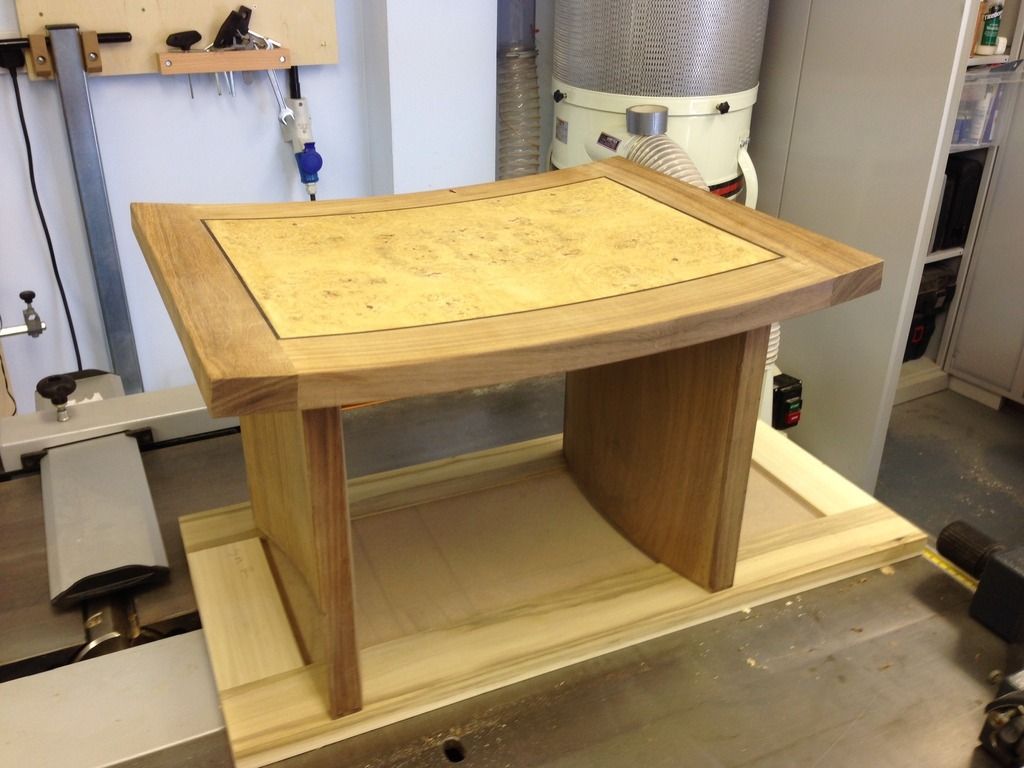
I entered the stool into a local exhibition and won first prize!!!
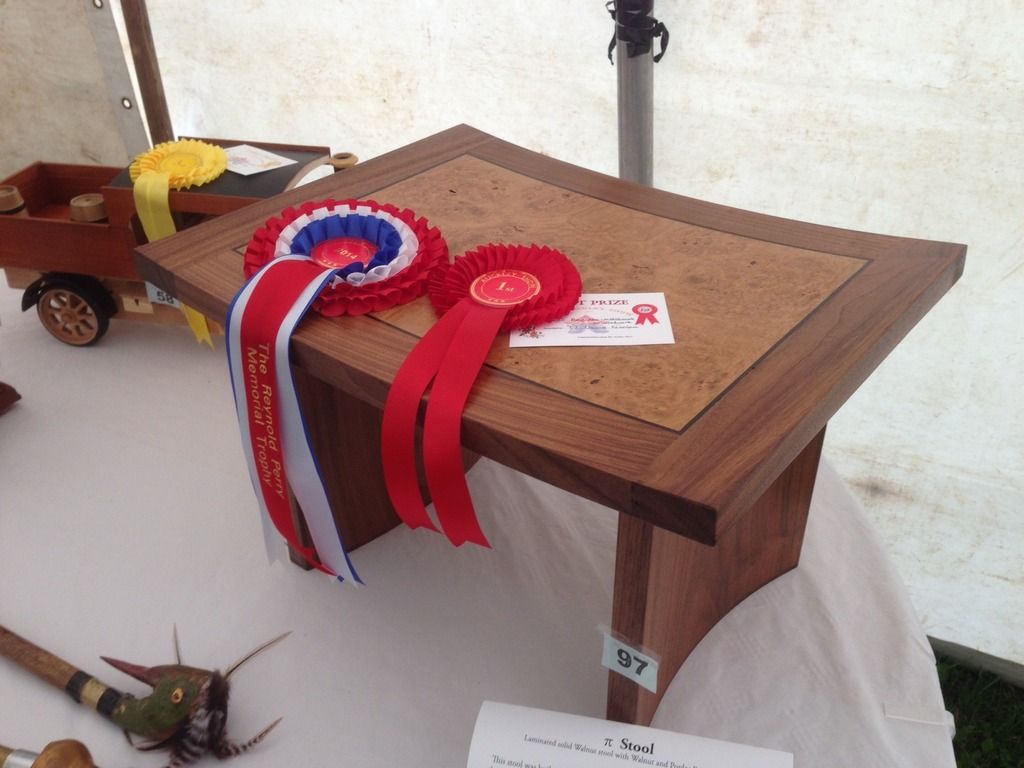
What next, well good question. I have just renovated the whole house over the last 6 months to get ready for our first baby so nothing for the time but I have had my eye on making my own sliding table and chairs. I was thinking about booking some special tuition and making the table over a few months but Chris' new chair making course looks like an amazing challenge and there is his piston fit draw making course which I really would love to do. So that's another two weeks spoken for.