Mikey R
Established Member
Hi everyone,
Im quite new here so I thought its about time i introduced myself properly and showed a project Ive been working on since last summer. Its a 5 string multiscale bass guitar. Beware, this post is a bit of a novel, so feel free to skip the text and just look at the pictures!
Multiscale basically means the frets are laid out in a fan arangement, allowing the bass strings to be longer and therefore at a higher tension, and the treble strings to be at a lower tension. When I started I'd never played one so buiding one seemed like a good idea.
The scale length of the low B is 35 1/2" dropping to 34" on the high G.
The neck is made of some dark american birch - Ive never seen this before but I liked the look of it, and it was cheaper than walnut
The body is made from some native ash I got from a friend at work.
The fingerboard is hard maple.
Heres the design:
Because I'd never built a bass guitar before, let alone a multiscale one, I chose to use only inexpensive timber from John Boddys. The fingerboard was made from resawing a 33mm square x 750mm maple turning blank:
Heres a pic of the fingerboard next to the neck blank:
And glued up and tapered:
Gluing the birch top to the ash core. Used pretty much all of my clamps. In furure I'll use two piece bookmatched tops and glue the center line first:
This pic shows the neck attached to the body:
Carving the neck:
Fretting:
Before doing any serious carving, I wanted to check the action and see how it played. So I fitted the bridge pieces:
And made a temporary nut:
I found that the action needed to go up quite alot, so I shaved some wood off the back of the neck at the heel.
Routing the pickup cavities was a little nervewracking - Ive really developed a preference for hand tools, but there was no easy way to do this - so out came the router.
Then I started with the job of carving the body using my Record spokeshave, Footprint rasp and a cabinet scraper. Since then Ive really fallen out with the rasp and shave, dispite upgrading the latter with a new Ray Iles iron.
Heres the front:
This one shows the beveled forarm contour a little better:
The hole for the barrel style jack socket is at a slight angle, so that I could cut away from the edge and make it look at little more interesting. I started with a 5mm pilot hole. Next was an 18mm flat bit, about 12mm deep, then followed by a 12mm bit the rest of the way. I wanted a more extreme angle, unfortunately whilst drilling the pilot hole I didnt get the angle right. But I think its turned out Ok.
The electronics cavity:
That native ash is hard stuff - next one will definately be made of something softer! Its just so hard to shape it properly!
Next job will be sanding. My cheap rasp has left some really deep scratches, so I'll need to sand those out with 80 grit, then work my way up to 220 grit. I really want an Auriou rasp, but Im not sure I can justify spending that much.
Im still undecided on the finish - I want something quick and easy, so I might try some wipe on varnish. The other option is water based acrylic laquer.
Im quite new here so I thought its about time i introduced myself properly and showed a project Ive been working on since last summer. Its a 5 string multiscale bass guitar. Beware, this post is a bit of a novel, so feel free to skip the text and just look at the pictures!
Multiscale basically means the frets are laid out in a fan arangement, allowing the bass strings to be longer and therefore at a higher tension, and the treble strings to be at a lower tension. When I started I'd never played one so buiding one seemed like a good idea.
The scale length of the low B is 35 1/2" dropping to 34" on the high G.
The neck is made of some dark american birch - Ive never seen this before but I liked the look of it, and it was cheaper than walnut
The body is made from some native ash I got from a friend at work.
The fingerboard is hard maple.
Heres the design:

Because I'd never built a bass guitar before, let alone a multiscale one, I chose to use only inexpensive timber from John Boddys. The fingerboard was made from resawing a 33mm square x 750mm maple turning blank:



Heres a pic of the fingerboard next to the neck blank:

And glued up and tapered:

Gluing the birch top to the ash core. Used pretty much all of my clamps. In furure I'll use two piece bookmatched tops and glue the center line first:

This pic shows the neck attached to the body:

Carving the neck:


Fretting:

Before doing any serious carving, I wanted to check the action and see how it played. So I fitted the bridge pieces:
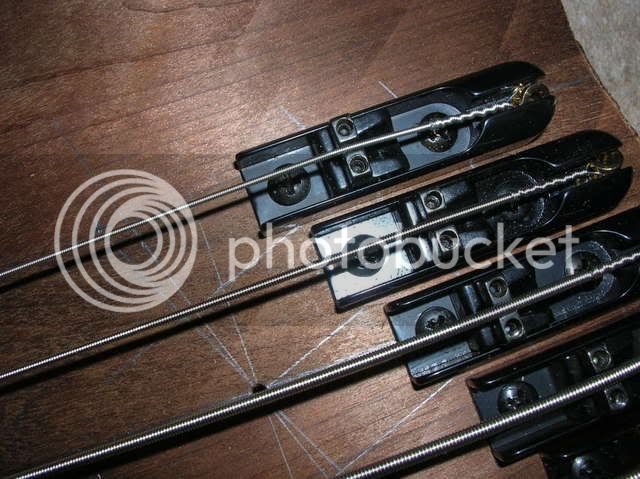
And made a temporary nut:
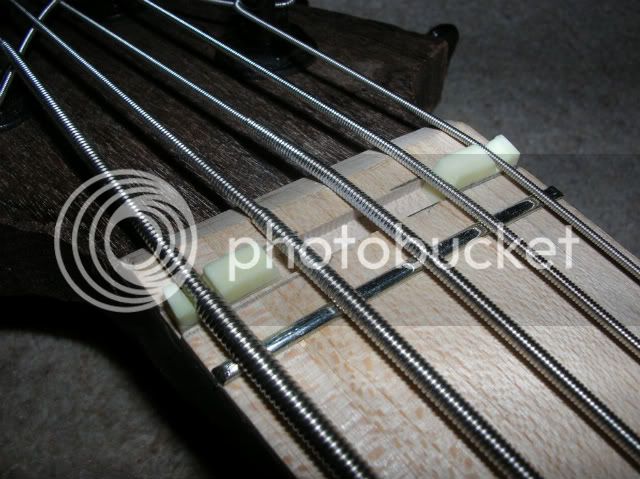
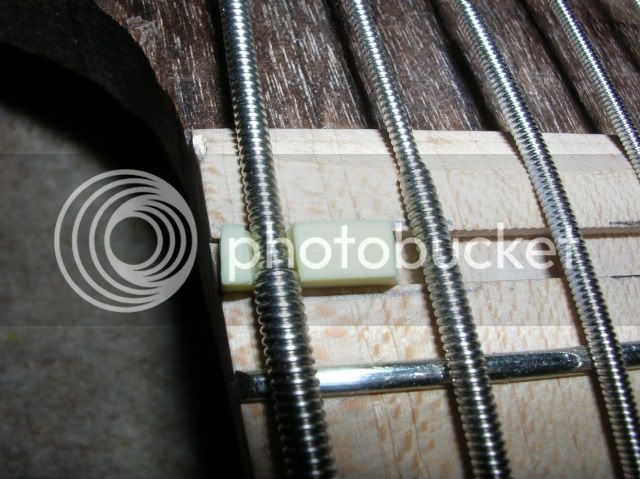
I found that the action needed to go up quite alot, so I shaved some wood off the back of the neck at the heel.
Routing the pickup cavities was a little nervewracking - Ive really developed a preference for hand tools, but there was no easy way to do this - so out came the router.
Then I started with the job of carving the body using my Record spokeshave, Footprint rasp and a cabinet scraper. Since then Ive really fallen out with the rasp and shave, dispite upgrading the latter with a new Ray Iles iron.
Heres the front:

This one shows the beveled forarm contour a little better:

The hole for the barrel style jack socket is at a slight angle, so that I could cut away from the edge and make it look at little more interesting. I started with a 5mm pilot hole. Next was an 18mm flat bit, about 12mm deep, then followed by a 12mm bit the rest of the way. I wanted a more extreme angle, unfortunately whilst drilling the pilot hole I didnt get the angle right. But I think its turned out Ok.

The electronics cavity:

That native ash is hard stuff - next one will definately be made of something softer! Its just so hard to shape it properly!
Next job will be sanding. My cheap rasp has left some really deep scratches, so I'll need to sand those out with 80 grit, then work my way up to 220 grit. I really want an Auriou rasp, but Im not sure I can justify spending that much.
Im still undecided on the finish - I want something quick and easy, so I might try some wipe on varnish. The other option is water based acrylic laquer.