9fingers
Established Member
I've been working on this project for a few weekends now. I bought an axminster mobile base kit a few months back for my table saw and it is OK but frustrating in that it only has two castoring wheels which gives it only limited manoeverability.
I wanted a base with greater load capacity and four wheel castoring for my bandsaw and Jet jointer.
Wheels shown in the Up or Fixed position
Wheels down or Mobile position
The lifting castor mount design is a shameless copy of the Axminster one but modified so that it can be made from stock materials.
I used 50mm steel angle and 40, 50 and 60 mm square box section tube
All readily available from steel stock holders in yellow pages.
The castors are also standard items
The parts were all cut on the bandsaw which I modified by making new pulleys to drop the speed down from wood cutting speeds to much slower metal cutting speeds. I bought a metal blade from Dragon Saws.
The rounded corners and smooth edges were done on a nutool 1" linisher.
Note the foot lever has a cam profile with the curved edge having a changing radius from the pivot hole.
The parts are assembled as shown using M8 x 70mm socket cap bolts.
The item shown is one of a pair of loose units going to be bolted onto the Axminster base to give it 4 castoring wheels.
The others were welded directly onto the angle iron frame.
The final task was to fit 'elephants foot' adjustable feet which can be seen in the first few pictures. When in use, the machines rest on these feet for stability.
If anyone want more details then I have Visio drawings showing the critical dimensions and an excel spreadsheet wth cam data - PM me with a direct email address for the files if you want more info.
Bob
UPDATE: 25-02-11
The original files for this project have been lost in computer moves. However there has been some recent interest so I have done some drawings based on the parts I made. These can be found here http://homepage.ntlworld.com/bob.minchi ... ring_feet/
HTH
Bob
I wanted a base with greater load capacity and four wheel castoring for my bandsaw and Jet jointer.
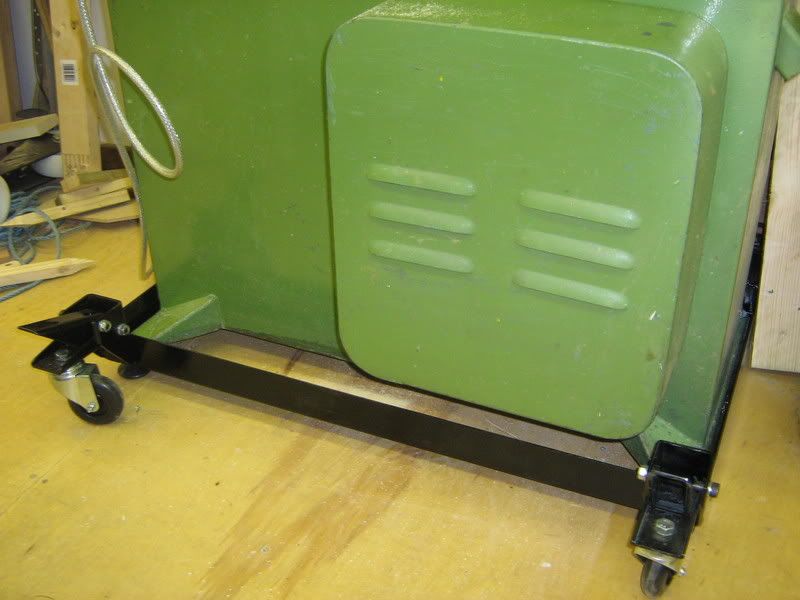
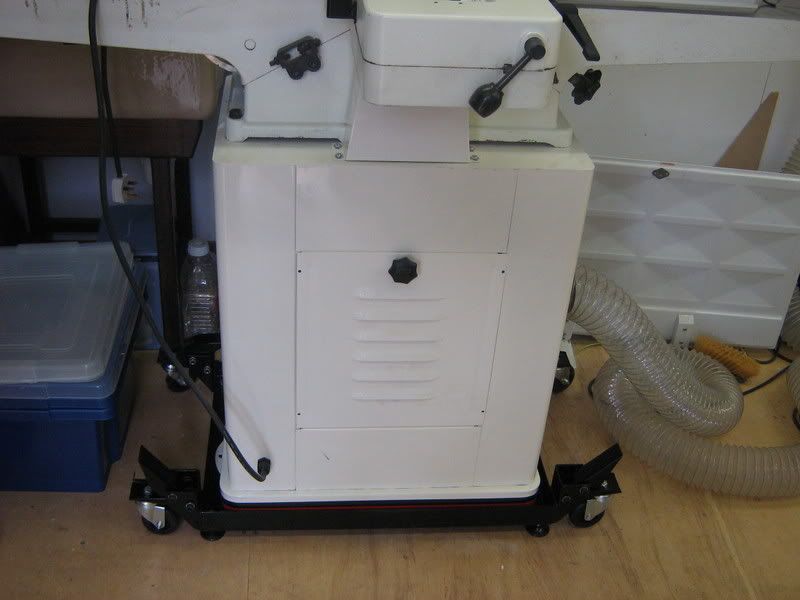
Wheels shown in the Up or Fixed position
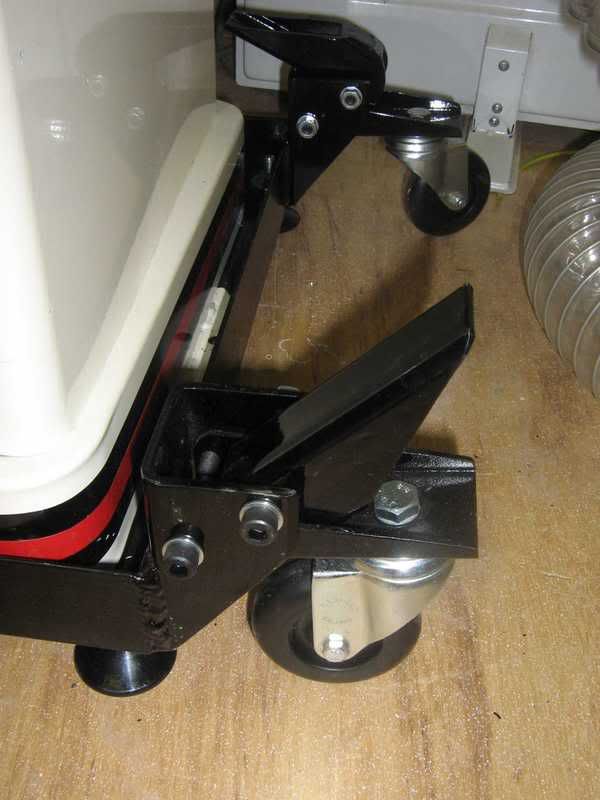
Wheels down or Mobile position
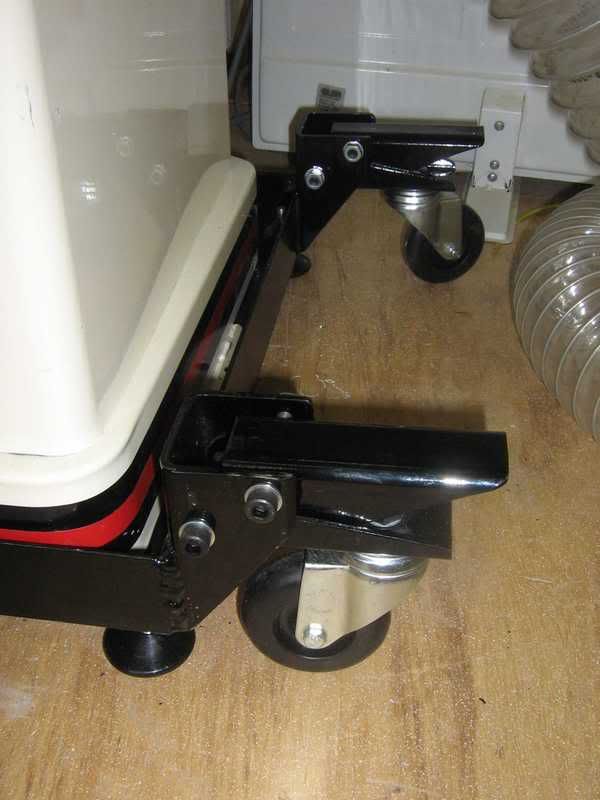
The lifting castor mount design is a shameless copy of the Axminster one but modified so that it can be made from stock materials.
I used 50mm steel angle and 40, 50 and 60 mm square box section tube
All readily available from steel stock holders in yellow pages.
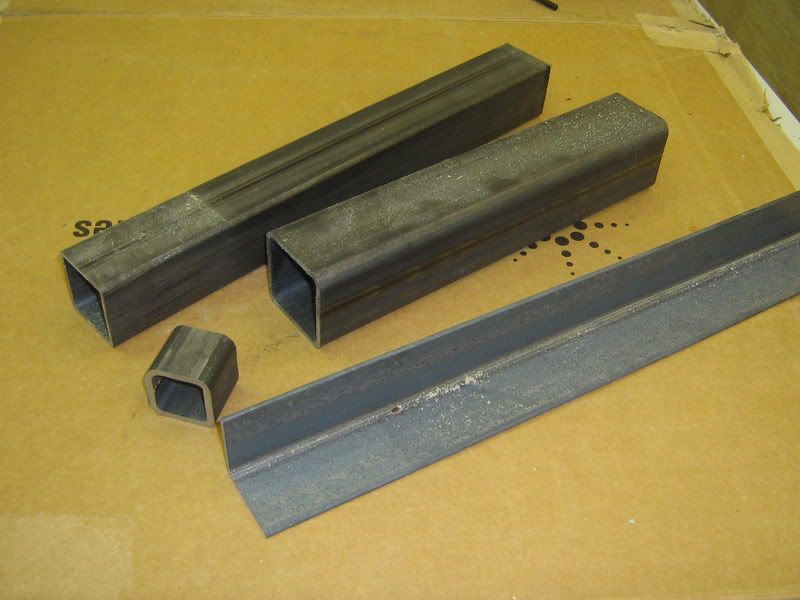
The castors are also standard items
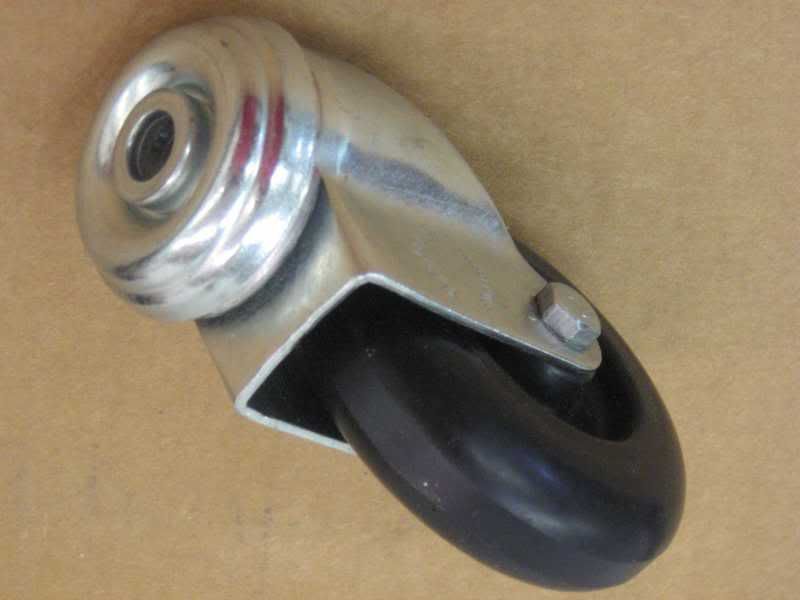
The parts were all cut on the bandsaw which I modified by making new pulleys to drop the speed down from wood cutting speeds to much slower metal cutting speeds. I bought a metal blade from Dragon Saws.
The rounded corners and smooth edges were done on a nutool 1" linisher.
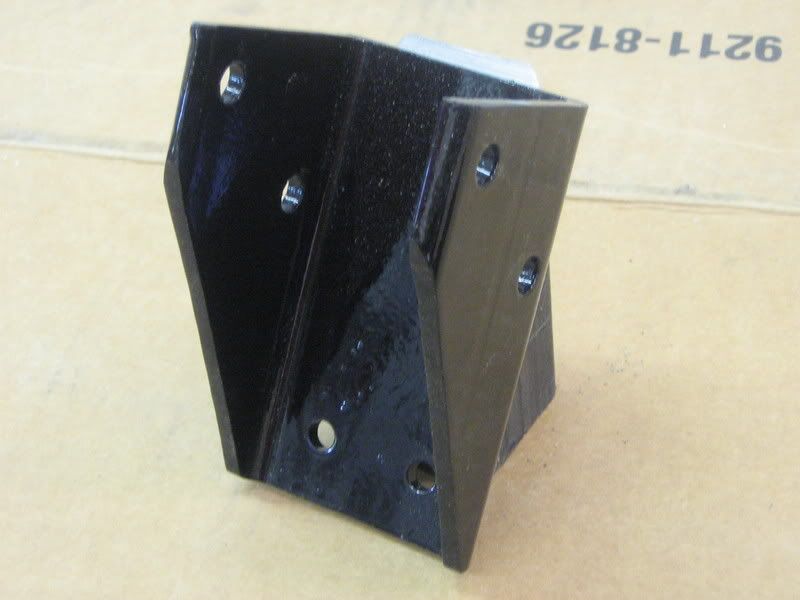
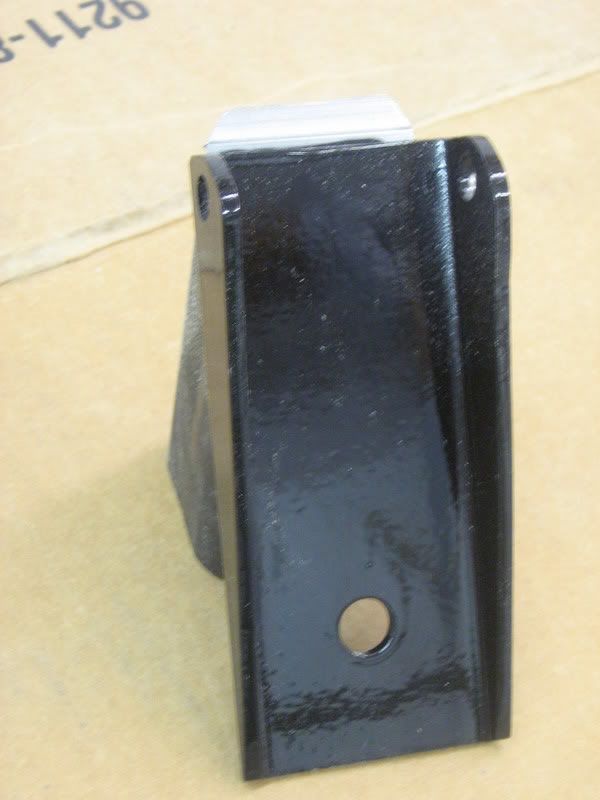
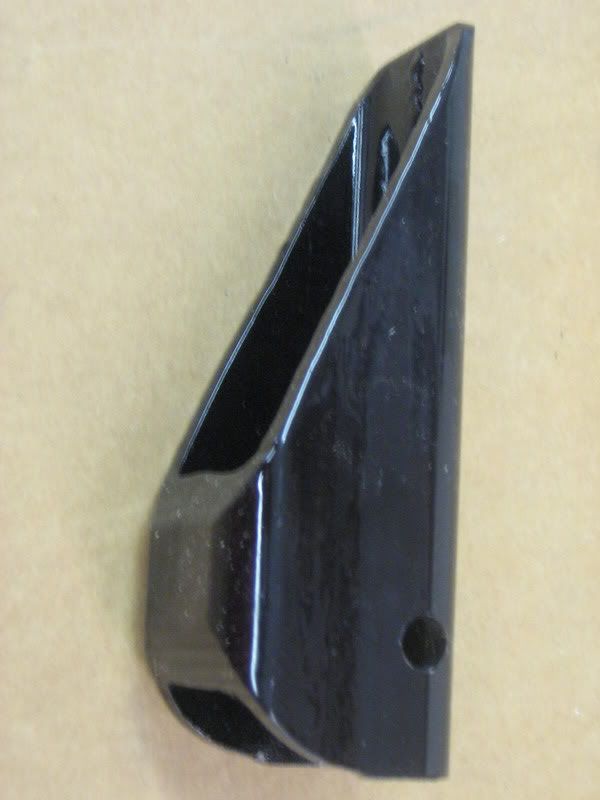
Note the foot lever has a cam profile with the curved edge having a changing radius from the pivot hole.
The parts are assembled as shown using M8 x 70mm socket cap bolts.
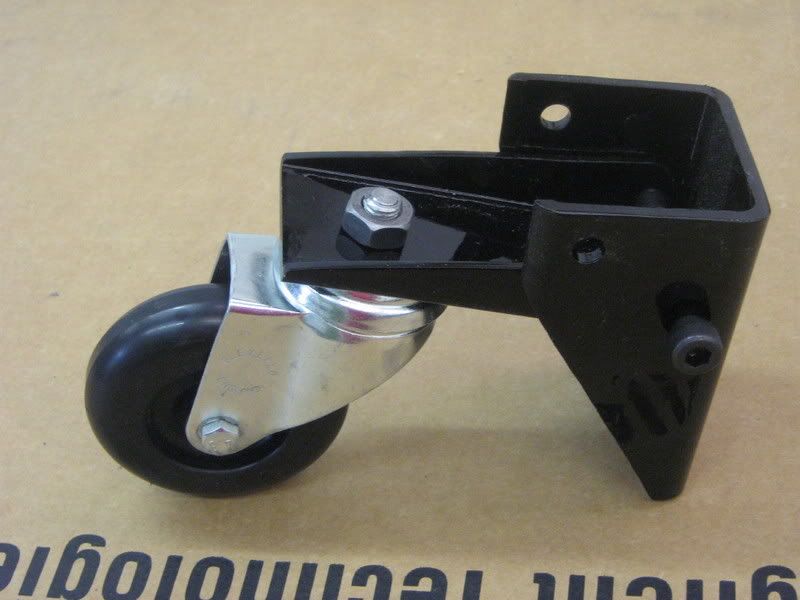
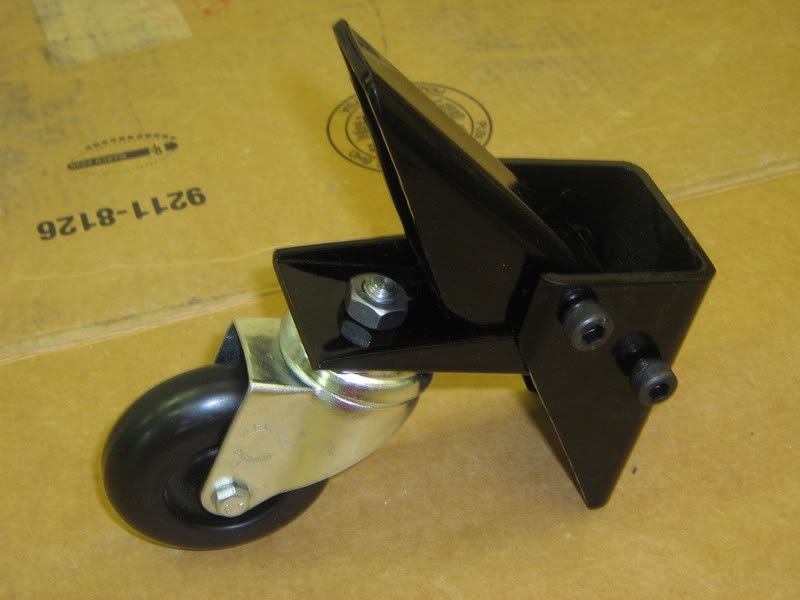
The item shown is one of a pair of loose units going to be bolted onto the Axminster base to give it 4 castoring wheels.
The others were welded directly onto the angle iron frame.
The final task was to fit 'elephants foot' adjustable feet which can be seen in the first few pictures. When in use, the machines rest on these feet for stability.
If anyone want more details then I have Visio drawings showing the critical dimensions and an excel spreadsheet wth cam data - PM me with a direct email address for the files if you want more info.
Bob
UPDATE: 25-02-11
The original files for this project have been lost in computer moves. However there has been some recent interest so I have done some drawings based on the parts I made. These can be found here http://homepage.ntlworld.com/bob.minchi ... ring_feet/
HTH
Bob