My competition entry is a small mantle clock , with arts and crafts influences, based on a design found in a text book called "In the craftsman style".
The design calls for the use of a timber with a mild, uncomplicated grain which will allow the design to dominate.
Here is a picture of the clock;
A few months ago I called to see Nigel at English Hardwoods in Geddington and we managed to find a chunk of English Pear. Nigel also kindly gave me a small piece of Bog Oak for the checkered inlay.
I also made an order from Merritt's Antiques, in Douglassville, USA for the clock parts, movement, dial, hands and pendulum.
Here is a picture of the materials;
I started work a month or so ago by planning and thicknessing the Pearwood and then using my bandsaw I divided the timber into various pieces which I cut roughly to size.
Here is an action shot of the resawing;
The yellow gadget is my Magswitch guide which works a treat.
and the fruits of my labour (sorry for the pun).
I left the pieces in my study for a month or so before picking up the action again this weekend.
More pictures and progress to follow this week.
Cheers, Tony.
The design calls for the use of a timber with a mild, uncomplicated grain which will allow the design to dominate.
Here is a picture of the clock;
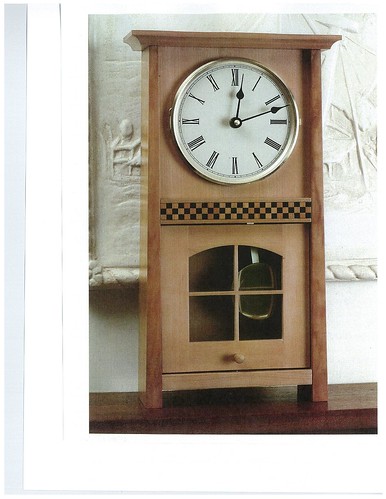
A few months ago I called to see Nigel at English Hardwoods in Geddington and we managed to find a chunk of English Pear. Nigel also kindly gave me a small piece of Bog Oak for the checkered inlay.
I also made an order from Merritt's Antiques, in Douglassville, USA for the clock parts, movement, dial, hands and pendulum.
Here is a picture of the materials;
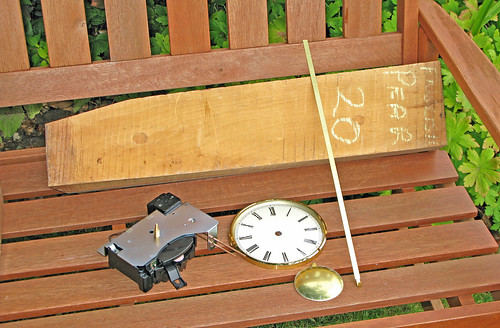
I started work a month or so ago by planning and thicknessing the Pearwood and then using my bandsaw I divided the timber into various pieces which I cut roughly to size.
Here is an action shot of the resawing;
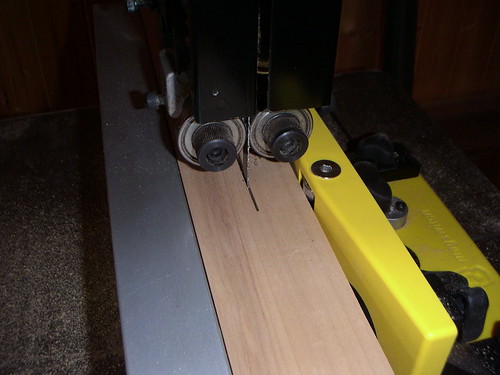
The yellow gadget is my Magswitch guide which works a treat.
and the fruits of my labour (sorry for the pun).
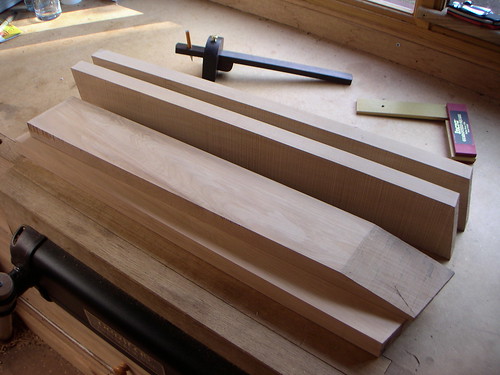
I left the pieces in my study for a month or so before picking up the action again this weekend.
More pictures and progress to follow this week.
Cheers, Tony.