PaulO
Established Member
I recently made this humidor for a friend, it is the second I have made. The first was made using american black walnut and maple, this one uses american cherry and roupala lacewood.
The construction is based on a single box made with through dovetails, with the top and bottom floating. The box is then cut in two, and the bottom half lined with spanish cedar.
Started with a rough sawn american cherry plank 1" thick, marked up the positions of the cuts for the four sides.
The stock was planed and thicknessed then ripped to length. Faces sides, edges and grain direction marked.
The sides will be 18mm thick (pins) and the front and back 12mm thick (tails)
The ends were shot square, this only took a few shavings as the tablesaw had got close. At this stage I also made sure that the sides and front/back where equal length.
I also planed the face side. This first picture shows some of the ripples left by the planer. You can also see my pencil squiggles used to check the progress of my sets of shavings
All ripples gone after a couple of sets of shavings.
I marked up the tail pattern on the front and back together. I do the design on a spreadsheet on my PC to make sure that I am going to leave enough room for a chisel to clear the waste, as well as aesthetics. You can see a particularly wide pin, which includes an allowance for my table saw kerf when I split it. I am not using super skinny pins, you will see why later.
Here I am scribing the shoulder line, about 0.1mm thinner than the tail stock thickness. This 0.1mm reduction makes them slightly tighter thanks to the way I mark pins. As this is the show side I am only scribing the shoulder between tails.
Here is the reason for not having super skinny pins, I decided to try using my tablesaw to cut the tails instead of my L-N dovetail saw. This should guarantee squareness, and reduce the amount of paring at the shoulder. The depth of cut was set to be a few tenths of a mm shy of the shoulder. The jig is set up for 1:7 tails, and as long as that is all it cuts, the jig prevents tearout at the back.
Don't worry, there is still plenty of handwork required.Remove the bulk of the waste with a fret saw, a jewellers saw is unnecessary thanks to the wide kerf.
Then chisel back to the line. For the final cut the chisel is registered in the shoulder line then tapped in square or 1 or 2 degrees of undercut. You can see that I have placed tape on the chisel at just over 1/2 thickness. I chop to 1/2 depth from both sides.
The construction is based on a single box made with through dovetails, with the top and bottom floating. The box is then cut in two, and the bottom half lined with spanish cedar.
Started with a rough sawn american cherry plank 1" thick, marked up the positions of the cuts for the four sides.
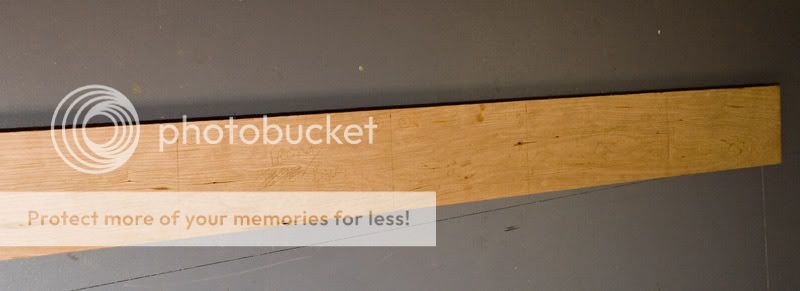
The stock was planed and thicknessed then ripped to length. Faces sides, edges and grain direction marked.
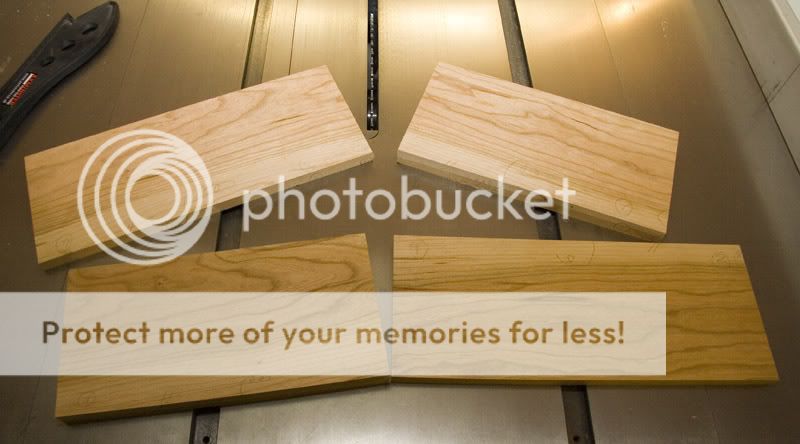
The sides will be 18mm thick (pins) and the front and back 12mm thick (tails)
The ends were shot square, this only took a few shavings as the tablesaw had got close. At this stage I also made sure that the sides and front/back where equal length.
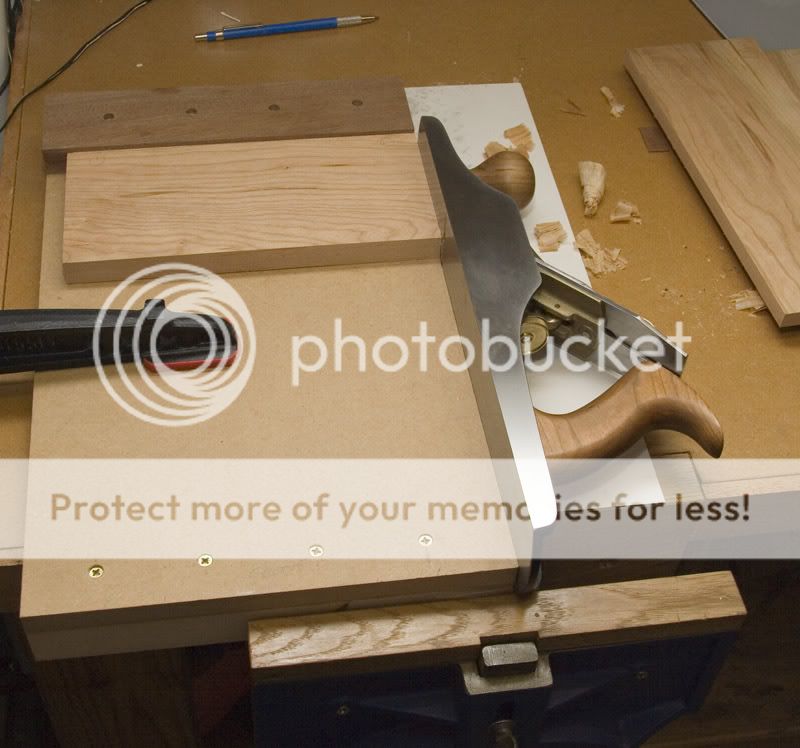
I also planed the face side. This first picture shows some of the ripples left by the planer. You can also see my pencil squiggles used to check the progress of my sets of shavings
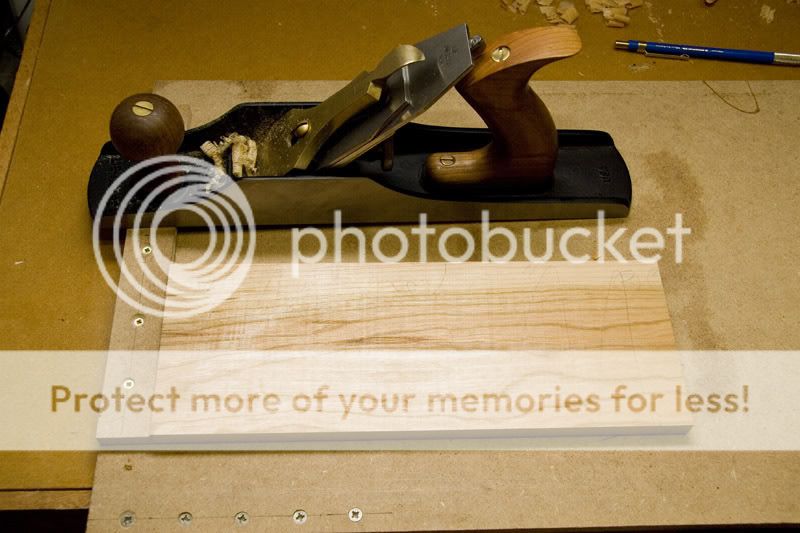
All ripples gone after a couple of sets of shavings.
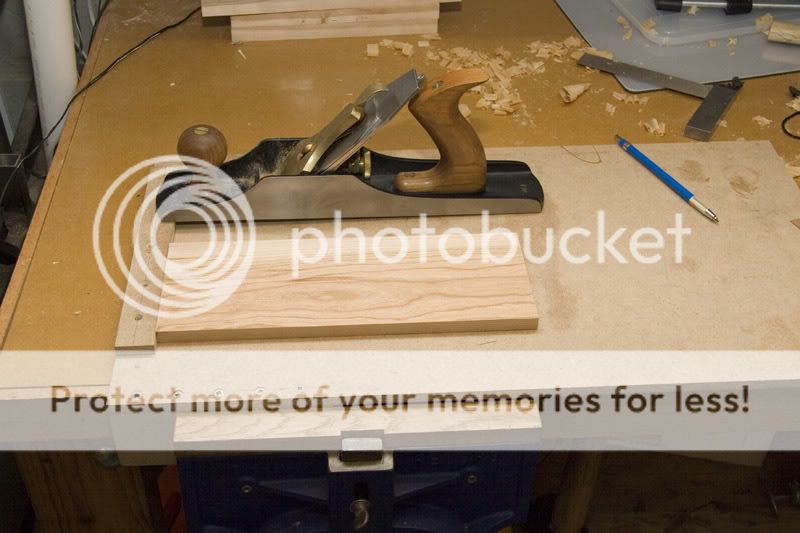
I marked up the tail pattern on the front and back together. I do the design on a spreadsheet on my PC to make sure that I am going to leave enough room for a chisel to clear the waste, as well as aesthetics. You can see a particularly wide pin, which includes an allowance for my table saw kerf when I split it. I am not using super skinny pins, you will see why later.
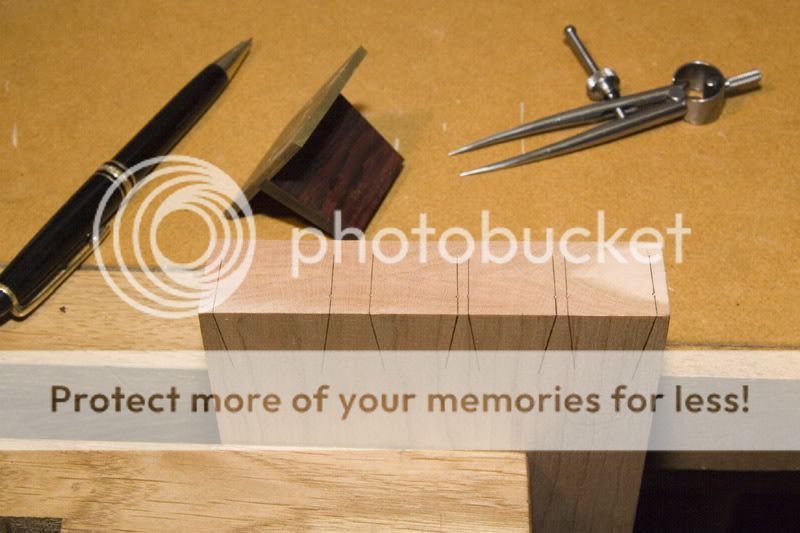
Here I am scribing the shoulder line, about 0.1mm thinner than the tail stock thickness. This 0.1mm reduction makes them slightly tighter thanks to the way I mark pins. As this is the show side I am only scribing the shoulder between tails.
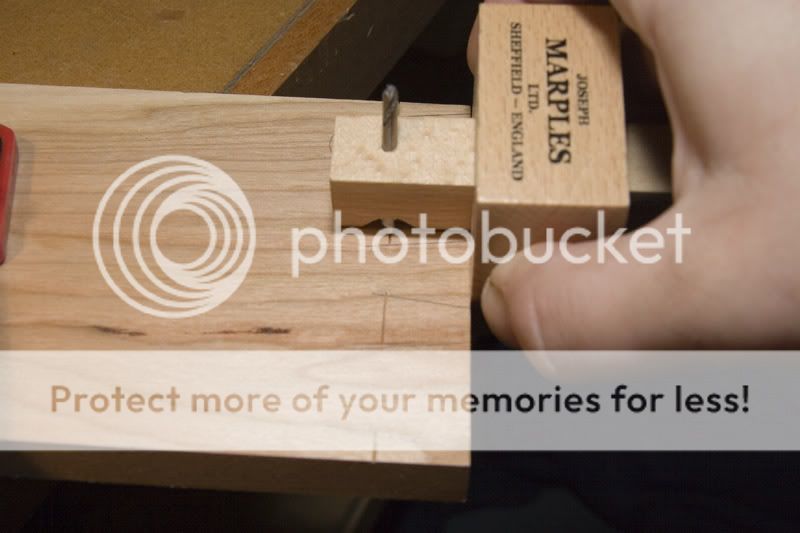
Here is the reason for not having super skinny pins, I decided to try using my tablesaw to cut the tails instead of my L-N dovetail saw. This should guarantee squareness, and reduce the amount of paring at the shoulder. The depth of cut was set to be a few tenths of a mm shy of the shoulder. The jig is set up for 1:7 tails, and as long as that is all it cuts, the jig prevents tearout at the back.
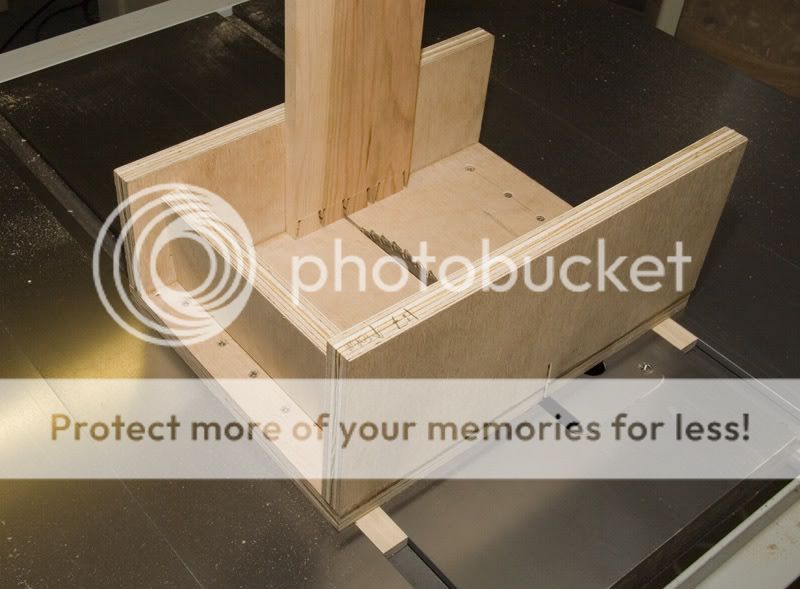
Don't worry, there is still plenty of handwork required.Remove the bulk of the waste with a fret saw, a jewellers saw is unnecessary thanks to the wide kerf.
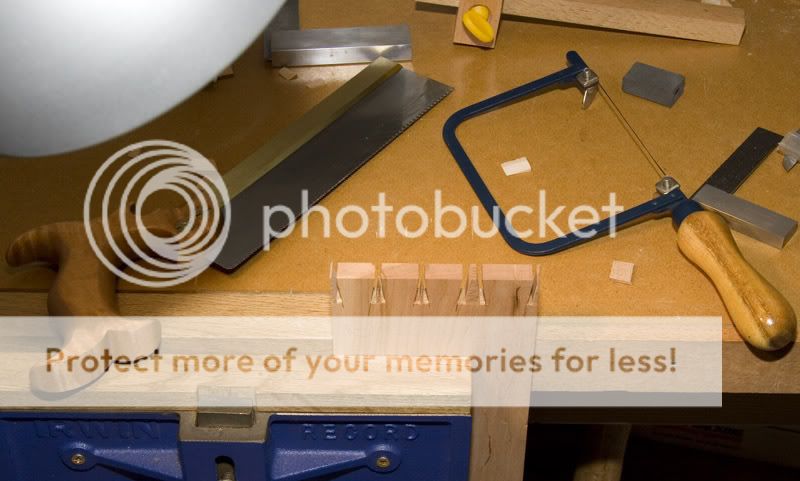
Then chisel back to the line. For the final cut the chisel is registered in the shoulder line then tapped in square or 1 or 2 degrees of undercut. You can see that I have placed tape on the chisel at just over 1/2 thickness. I chop to 1/2 depth from both sides.
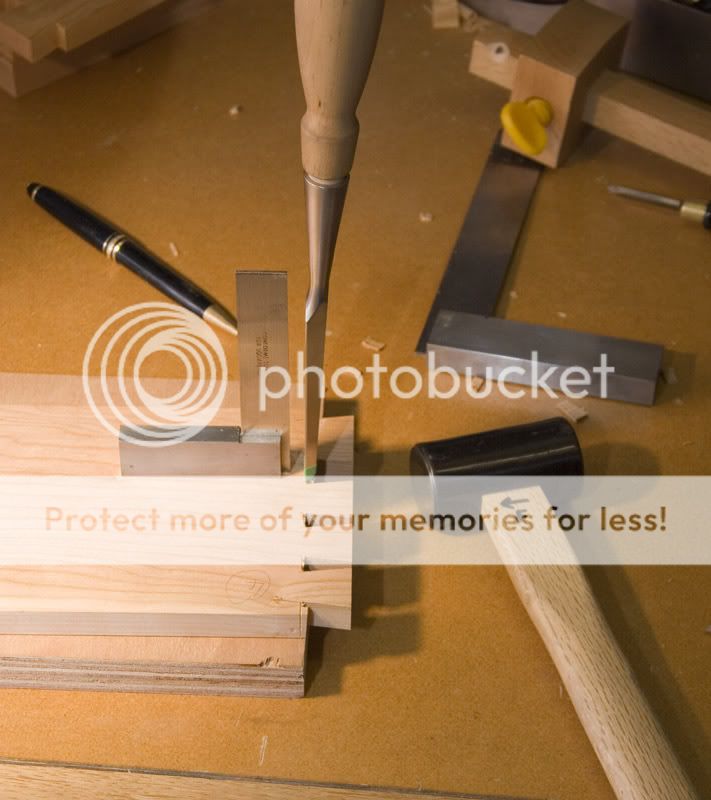