Pekka Huhta
Established Member
I got an idea for a infill molding plane a couple of years ago. I think that it’s a quite new concept; at least I haven’t seen anything like it before. The idea was to have a separate frame where you could install different infills. When needing a new profile, you would only have to build a short length of infill and a cutter.
The concept is built on many old ideas. It’s easy to grind a new cutter for a #55, but adjustment is sheer **** and you don’t have a mouth for the plane at all. Firstly I was thinking of building separate wooden soles for a #45 or a #55, but attaching the soles to the skates was a bit difficult and I thought that the original planes would restrict the concept too much.
The plane certainly has the looks of old infill planes, but actually I think that it borrows much more from Krenov: you have two “cheeks” as on a Krenov plane and the rest of the parts built in between, only difference is that the infills are removable.
Finally, there's a lot of an old patternmaker's plane with separate soles and irons, but the idea is much simpler and has a much older feel.
So, there’s a lot of borrowed ideas on the plane, but I think it’s quite unique anyway.
I got a good excuse for building the plane when I needed new skirting boards for my small hallway. I had found a small length of an original skirting board from my house, which I wanted to replicate. I could have planed the profile with several planes as I have done earlier (see my blog (Story 1, Story 2)
Usually I take pictures from everything I build, but I got a bit too excited with the frame, so there aren’t any pictures about the process. All in all, it was very straightforward dovetailing job, much easier than any “proper” infill plane. The pin for the cap iron was made from a 10 mm brass rod which was inserted inside a shorter 12 mm brass tube. The ends of the tube acted as a shoulder to keep the sides of the frame on the proper distance from each other. This was done just because I don’t have a metalworking lathe so that I could have just turned a pin with the shoulders built in.
For the infills I got an offcut of an oak plank a bit over 4” thick and two feet wide. Although there were checks and splits on the wood, there was plenty of good oak for the infills. I learned that the blank for the infills should be at least a few inches longer on both ends than the finished infills, since the ends of the sole profile are a bit different than the majority of the profile in the middle.
Profiling the sole is dead easy. You just have to take a length of sawblade, cut a kerf in a short length of the original profile, mark the sawblade, rough out the waste with a grinder and finally file the scraper ready with a few needle files. Almost as fast as explaining it.
Roughing out the sole is quick. Only thing to be considered is that you should re-sharpen the scraper before final passes on the sole. When roughing out, you tilt the scraper to remove material fast. When finishing the profile you have to keep the scraper perpendicular to the sole in order to get the profile right. And you have to have a sharp scraper in order to get it cutting when it’s perpendicular to the sole.
A set of hollows and rounds and a narrow shoulder plane are of great help when finishing the profile. I’m not sure wether you could do it with a scraper only, probably you would have to finish the profile with sandpaper wrapped over dowels or something. Scraping will not necessarily produce a straight profile, it may be curved or kinked depending on your scraping technique.
As you note, there is only the depth stop on the profile. I could have included an integral fence as well, but I wanted a continuous fence screwed on the infills, since that would aid keeping the infills aligned.
Then there was some metalwork to be done. The cap iron was cut from a piece of 8 mm brass bar and then filed to shape and polished. The adjuster screw was the only pre-fabricated part of the plane, it was some sort of an adjuster screw with imperial threads. I re-drilled and tapped it for M6 thread and riveted a brass screw to it.
I got a bit carried away with the iron, so there’s no pictures of the marking out. I just sawed the infill to the correct bed angle and drew the profile to the iron using the backside of the mouth as a template. Then I just sawed the excess off with a jewellers saw, filed the bevel and finally tempered the iron on my charcoal furnace.
At this stage I had fitted the infills, so they had to be finished. I soaked the infills for half a day in raw linseed oil and pine turpentine. Next I added a few coats of dark shellack, used fine rottenstone powder to fill the grain, sanded the surface with wet&dry and lamp oil and after adding a few more coats of shellack, polished and waxed the plane with home brewn “tool wax” containing boiled linseed oil, beeswax, pine turpentine and tar.
Finally there was the time for fine tuning and planing the moldings. Originally the escapement for shavings was very narrow, so the shavings got stuck. After enlarging it, modifying the fence and shaping the cap iron a bit the shavings exited nicely.
Next problem was that the plane refused to cut the complete molding, it just stopped cutting after a while. This was due to the fact that the infills were very very slightly misaligned. I had to shave a few passes from the profile with a shoulder plane, but after that the plane worked perfectly.
The plane is a tad shorter than molding planes usually are. That added to the separate fence makes the plane look quite tall, I’m not sure if I’m completely satisfied with the proportions. But all in all, it’s a pretty little plane and I proofed to myself that my idea really works.
Pekka
The concept is built on many old ideas. It’s easy to grind a new cutter for a #55, but adjustment is sheer **** and you don’t have a mouth for the plane at all. Firstly I was thinking of building separate wooden soles for a #45 or a #55, but attaching the soles to the skates was a bit difficult and I thought that the original planes would restrict the concept too much.
The plane certainly has the looks of old infill planes, but actually I think that it borrows much more from Krenov: you have two “cheeks” as on a Krenov plane and the rest of the parts built in between, only difference is that the infills are removable.
Finally, there's a lot of an old patternmaker's plane with separate soles and irons, but the idea is much simpler and has a much older feel.
So, there’s a lot of borrowed ideas on the plane, but I think it’s quite unique anyway.
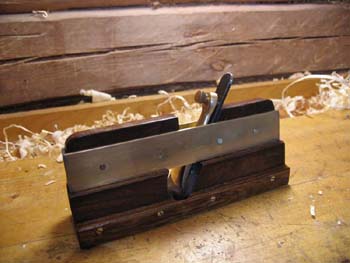
I got a good excuse for building the plane when I needed new skirting boards for my small hallway. I had found a small length of an original skirting board from my house, which I wanted to replicate. I could have planed the profile with several planes as I have done earlier (see my blog (Story 1, Story 2)
Usually I take pictures from everything I build, but I got a bit too excited with the frame, so there aren’t any pictures about the process. All in all, it was very straightforward dovetailing job, much easier than any “proper” infill plane. The pin for the cap iron was made from a 10 mm brass rod which was inserted inside a shorter 12 mm brass tube. The ends of the tube acted as a shoulder to keep the sides of the frame on the proper distance from each other. This was done just because I don’t have a metalworking lathe so that I could have just turned a pin with the shoulders built in.
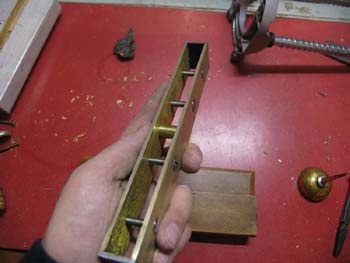
For the infills I got an offcut of an oak plank a bit over 4” thick and two feet wide. Although there were checks and splits on the wood, there was plenty of good oak for the infills. I learned that the blank for the infills should be at least a few inches longer on both ends than the finished infills, since the ends of the sole profile are a bit different than the majority of the profile in the middle.
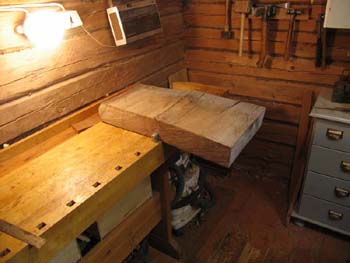
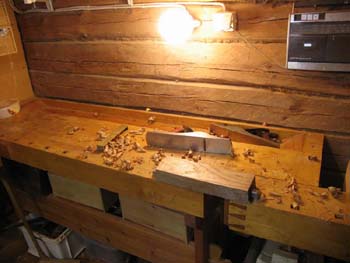
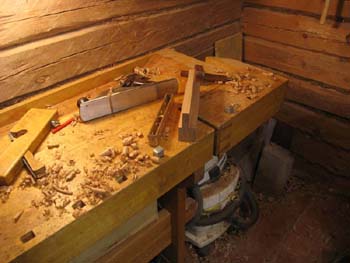
Profiling the sole is dead easy. You just have to take a length of sawblade, cut a kerf in a short length of the original profile, mark the sawblade, rough out the waste with a grinder and finally file the scraper ready with a few needle files. Almost as fast as explaining it.
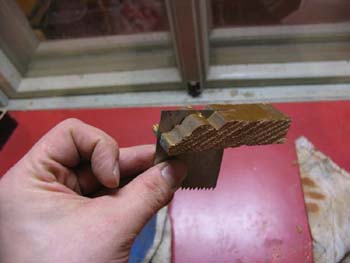
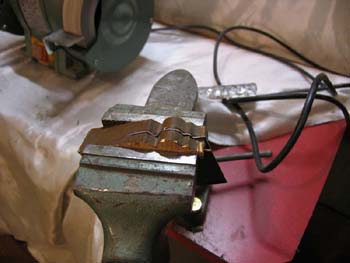
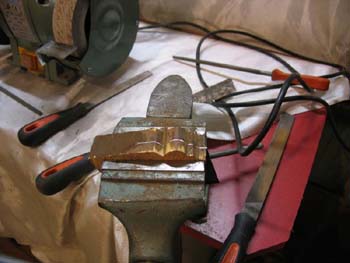
Roughing out the sole is quick. Only thing to be considered is that you should re-sharpen the scraper before final passes on the sole. When roughing out, you tilt the scraper to remove material fast. When finishing the profile you have to keep the scraper perpendicular to the sole in order to get the profile right. And you have to have a sharp scraper in order to get it cutting when it’s perpendicular to the sole.
A set of hollows and rounds and a narrow shoulder plane are of great help when finishing the profile. I’m not sure wether you could do it with a scraper only, probably you would have to finish the profile with sandpaper wrapped over dowels or something. Scraping will not necessarily produce a straight profile, it may be curved or kinked depending on your scraping technique.
As you note, there is only the depth stop on the profile. I could have included an integral fence as well, but I wanted a continuous fence screwed on the infills, since that would aid keeping the infills aligned.
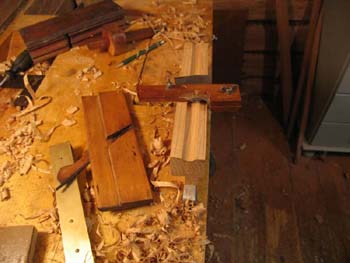
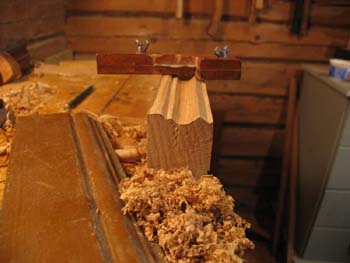
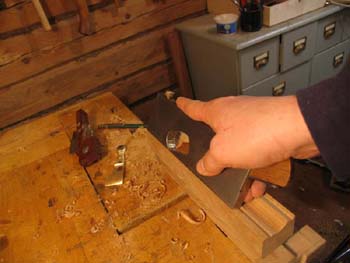
Then there was some metalwork to be done. The cap iron was cut from a piece of 8 mm brass bar and then filed to shape and polished. The adjuster screw was the only pre-fabricated part of the plane, it was some sort of an adjuster screw with imperial threads. I re-drilled and tapped it for M6 thread and riveted a brass screw to it.
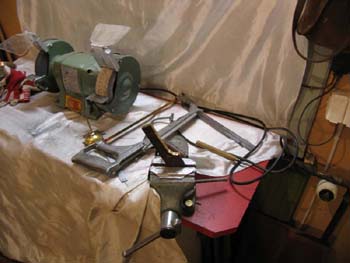
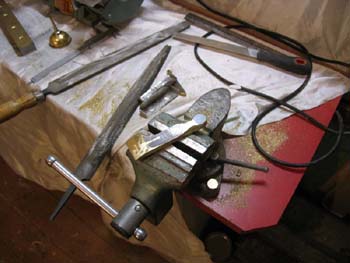
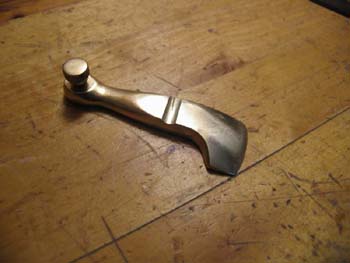
I got a bit carried away with the iron, so there’s no pictures of the marking out. I just sawed the infill to the correct bed angle and drew the profile to the iron using the backside of the mouth as a template. Then I just sawed the excess off with a jewellers saw, filed the bevel and finally tempered the iron on my charcoal furnace.
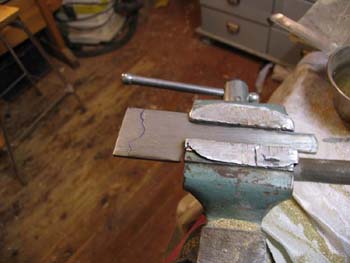
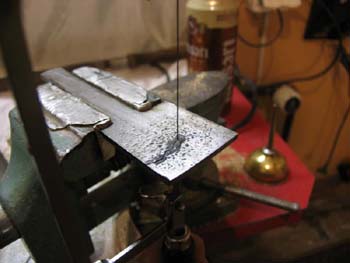
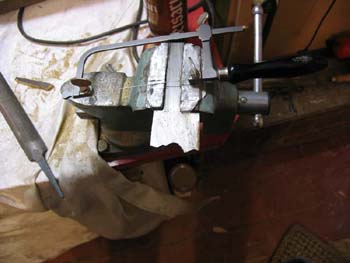
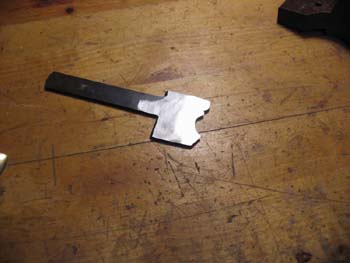
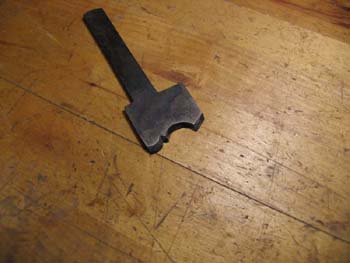
At this stage I had fitted the infills, so they had to be finished. I soaked the infills for half a day in raw linseed oil and pine turpentine. Next I added a few coats of dark shellack, used fine rottenstone powder to fill the grain, sanded the surface with wet&dry and lamp oil and after adding a few more coats of shellack, polished and waxed the plane with home brewn “tool wax” containing boiled linseed oil, beeswax, pine turpentine and tar.
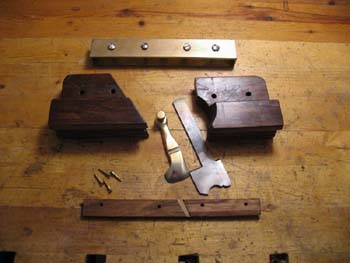
Finally there was the time for fine tuning and planing the moldings. Originally the escapement for shavings was very narrow, so the shavings got stuck. After enlarging it, modifying the fence and shaping the cap iron a bit the shavings exited nicely.
Next problem was that the plane refused to cut the complete molding, it just stopped cutting after a while. This was due to the fact that the infills were very very slightly misaligned. I had to shave a few passes from the profile with a shoulder plane, but after that the plane worked perfectly.
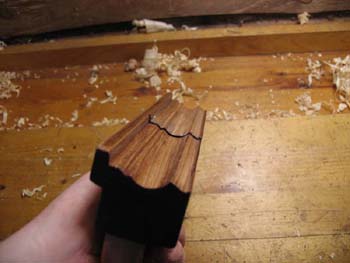
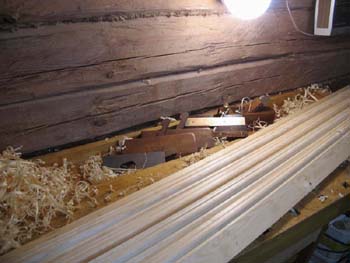
The plane is a tad shorter than molding planes usually are. That added to the separate fence makes the plane look quite tall, I’m not sure if I’m completely satisfied with the proportions. But all in all, it’s a pretty little plane and I proofed to myself that my idea really works.
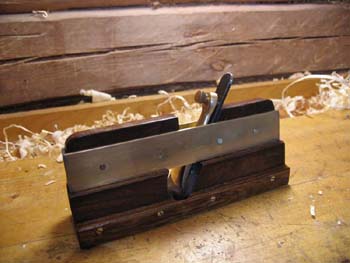
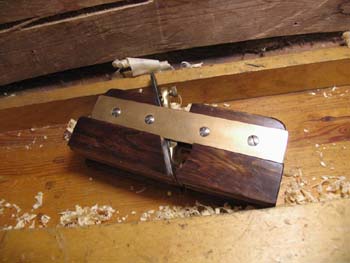
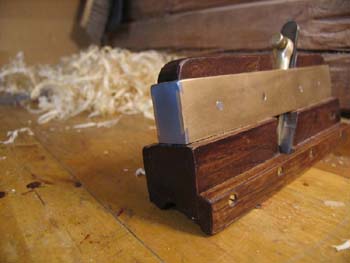
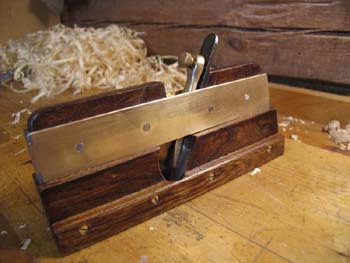
Pekka