sploo
Somewhat extinguished member
I've been building a version of Marc's Kitchen Helper (http://www.thewoodwhisperer.com/videos/ ... en-helper/) and was scratching my head on how best to create the arches in the horizontal sections.
I'd usually just throw something at the CNC machine (i.e. cheat) but it's out of action at the moment.
Marc's technique is to rough cut the curve on the bandsaw, then sand with a flexible sanding block, but I fancied trying something different.
My solution was to use an improvised circle cutting jig with a router, to cut suitable arcs for the two different lengths on sheets of 1/4" (6mm) MDF.
I then screwed 1/2" (12mm) blocks on the underside of the MDF to trap the material to be cut, and also glued on a piece of sandpaper to help resist movement.
A quick rough cut on the bandsaw to remove some waste material, then a trimming bit on the router table makes quick work of the pieces.
It took a little bit of time to make the templates, but machining the stock is then so fast (and with a good finish) that it's worth the time, even for this short production run. If I were making multiple copies it'd be a huge time saver.
On the subject of safety; note that the stock being cut is 3/4" (18mm) thick, so applying pressure on the top of the jig holds the stock against the sandpaper. If the blocks on the underside were also 3/4" it might risk movement of the stock (being pulled into the router bit) as it (the stock) wouldn't be held against the sandpaper with as much force.
I'd usually just throw something at the CNC machine (i.e. cheat) but it's out of action at the moment.
Marc's technique is to rough cut the curve on the bandsaw, then sand with a flexible sanding block, but I fancied trying something different.
My solution was to use an improvised circle cutting jig with a router, to cut suitable arcs for the two different lengths on sheets of 1/4" (6mm) MDF.
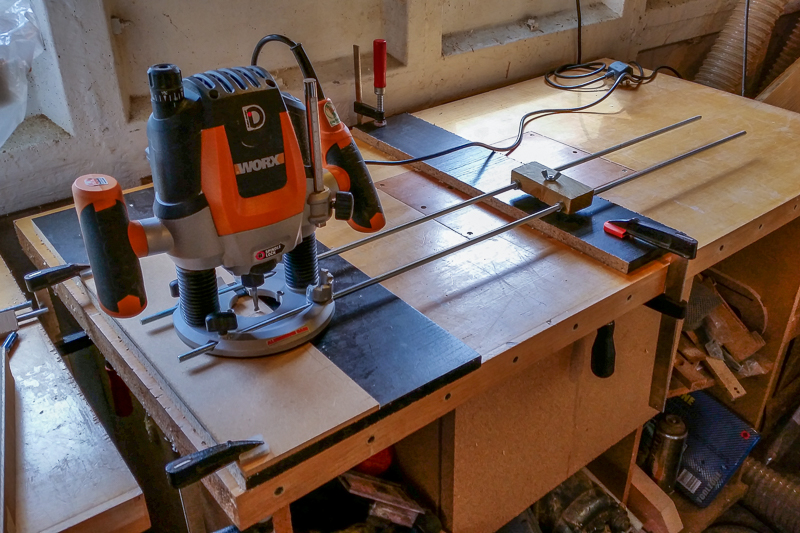
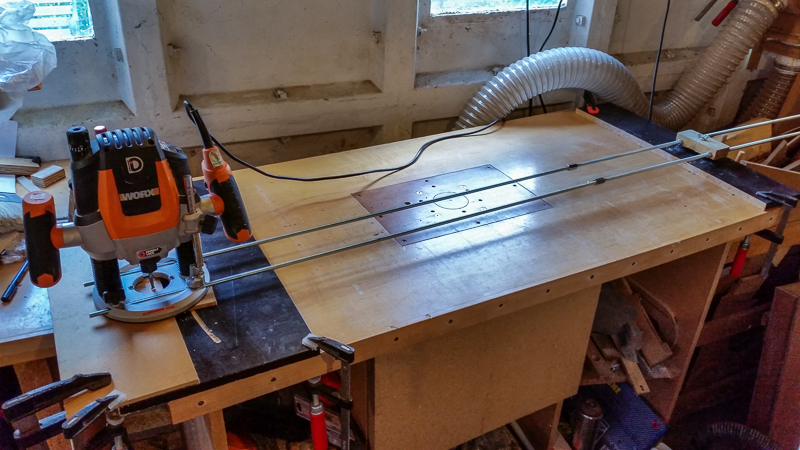
I then screwed 1/2" (12mm) blocks on the underside of the MDF to trap the material to be cut, and also glued on a piece of sandpaper to help resist movement.

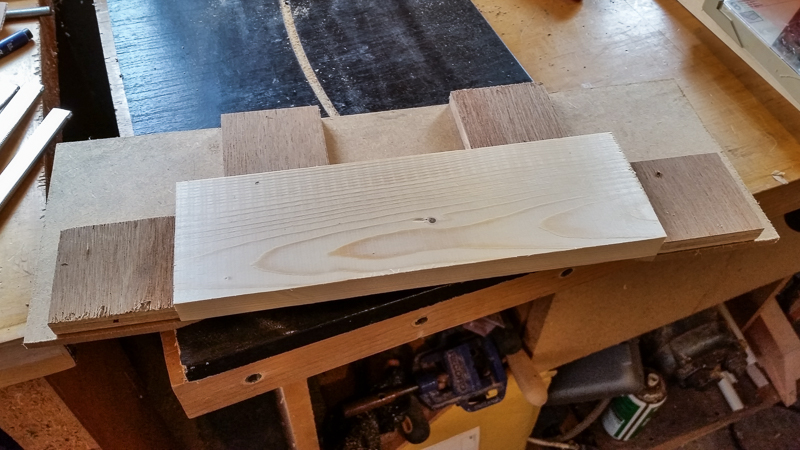
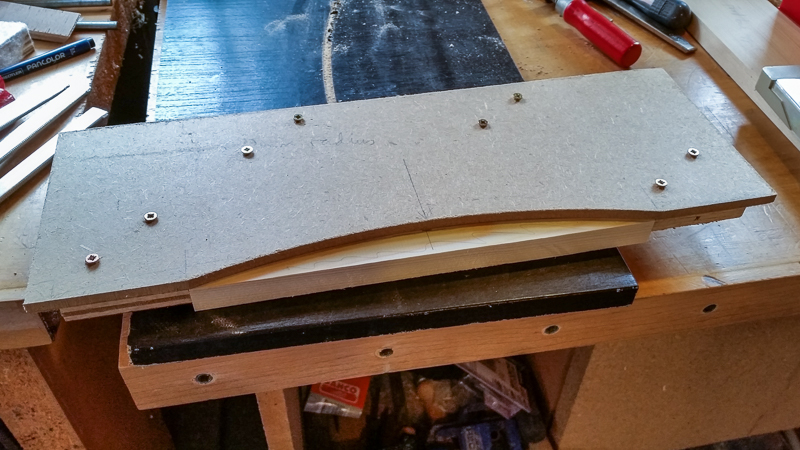
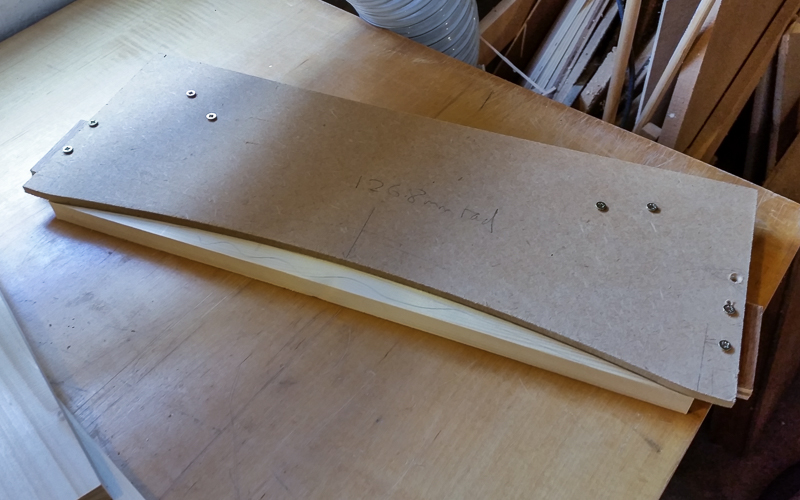
A quick rough cut on the bandsaw to remove some waste material, then a trimming bit on the router table makes quick work of the pieces.
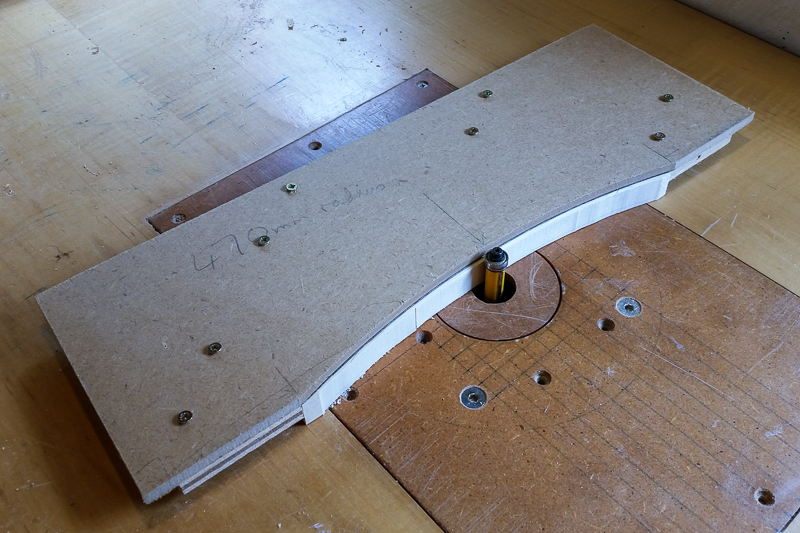
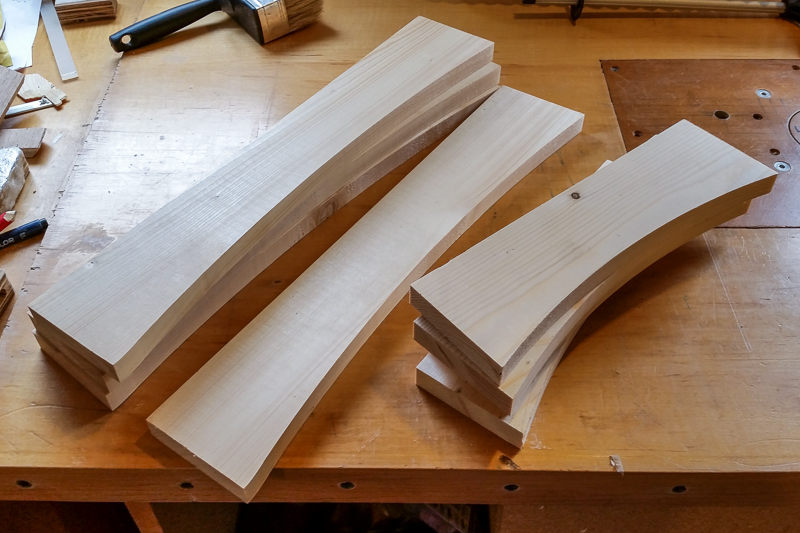
It took a little bit of time to make the templates, but machining the stock is then so fast (and with a good finish) that it's worth the time, even for this short production run. If I were making multiple copies it'd be a huge time saver.
On the subject of safety; note that the stock being cut is 3/4" (18mm) thick, so applying pressure on the top of the jig holds the stock against the sandpaper. If the blocks on the underside were also 3/4" it might risk movement of the stock (being pulled into the router bit) as it (the stock) wouldn't be held against the sandpaper with as much force.