CroppyBoy1798
Established Member
Hi guys!
Thought this would be of interest here, however, as the title says this is perhaps more of a metalwork project than a woodwork one, but it is however a piece of woodwork machinery, so, make what of it you will 8)
Having caught a glimpse of the 'washing machine motor' thread over in 'Jigs and Tips', I figured one of these machines would be incredibly handy to have and hopefully save a lot of time!! After a snoop about and some help from a mate I aquired a motor, shaft and a couple of pillow blocks, not bad going!
. The motor, however, although a nice old, incredibly heavy and sturdy quiet running induction motor didnt have the power, so, my el cheapo Aldi table saw thats been sitting idle for the past few years had its heart removed!! :lol:
So, I decided I'd try make this machine out of metal, I feel its the best choice for the job, ie keep the machine strong and sturdy, but not as bulky and 'heavy' looking as well as (hopefully) allowing me to make an open end sander! Thus, I wont be 'that' constricted and can sand items double the width of the drum.
Anyway, have a look at the computer images below and you'll have an idea of what the plan is.
The machine frame will be made of 40mm box, all welded construction and will be free standing. I had planned on making a bench top model, but, having recently aquired a little more space in the shop I can afford to have it a free stander. (the legs will have four rubber/hardwood pads attached).
A sheet steel cover will be fixed over the gantry thereby covering the pulleys/belt as well as somewhat enclosing the drum and allowing for a dust collection port to be fitted.
The gantry, like the rest will be made of 40mm box, reinforced with fillets at the corners.
The motor runs at 2950RPM, far too fast for a direct or 1:1 ratio, thus the drum having a diameter of 4" will need a 4" pulley, so, with a 2.25" pulley on the motor that will give an RPM of about 1400-1500.
Underview of sanding drum. The drum is approx 14" long. The pillow block on the 'open' side will need to be inverted.
The tilt mechanism for the table. As this is a 'simple' home build the means of adjusting the table for thickness will be done via a crank handle which will raise the table nearer the drum (it will be hingle at the opposite end).
Infeed/front view. The power switch, motor, crank handle are all donors from the aldi saw!
So there you have it. Seems good in theory, hope it works out! I still have to figure out a tensioning system for the belt as the motor will be fixed in place, but I think I have an idea for that, ie a idler wheel that will put pressure on the belt thereby tensioning it.
Any questions, opinion, help, info, crit etc all welcome! :wink:
Thought this would be of interest here, however, as the title says this is perhaps more of a metalwork project than a woodwork one, but it is however a piece of woodwork machinery, so, make what of it you will 8)
Having caught a glimpse of the 'washing machine motor' thread over in 'Jigs and Tips', I figured one of these machines would be incredibly handy to have and hopefully save a lot of time!! After a snoop about and some help from a mate I aquired a motor, shaft and a couple of pillow blocks, not bad going!
So, I decided I'd try make this machine out of metal, I feel its the best choice for the job, ie keep the machine strong and sturdy, but not as bulky and 'heavy' looking as well as (hopefully) allowing me to make an open end sander! Thus, I wont be 'that' constricted and can sand items double the width of the drum.
Anyway, have a look at the computer images below and you'll have an idea of what the plan is.
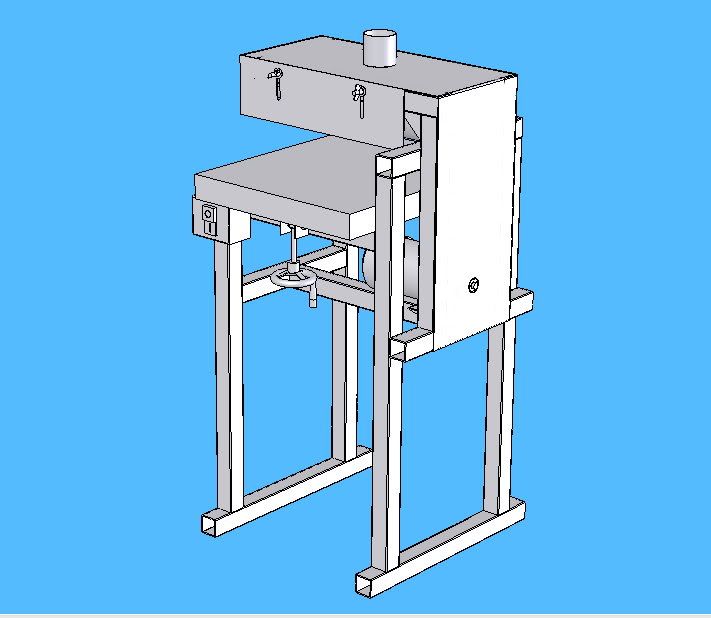
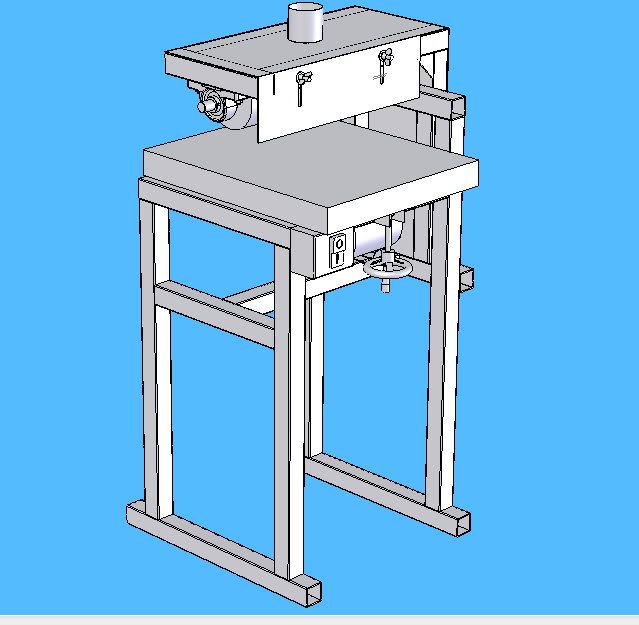
The machine frame will be made of 40mm box, all welded construction and will be free standing. I had planned on making a bench top model, but, having recently aquired a little more space in the shop I can afford to have it a free stander. (the legs will have four rubber/hardwood pads attached).
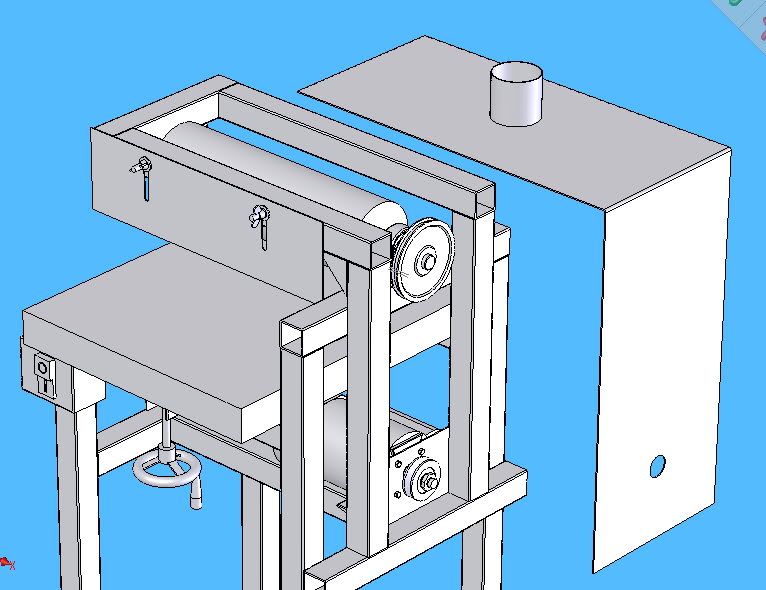
A sheet steel cover will be fixed over the gantry thereby covering the pulleys/belt as well as somewhat enclosing the drum and allowing for a dust collection port to be fitted.
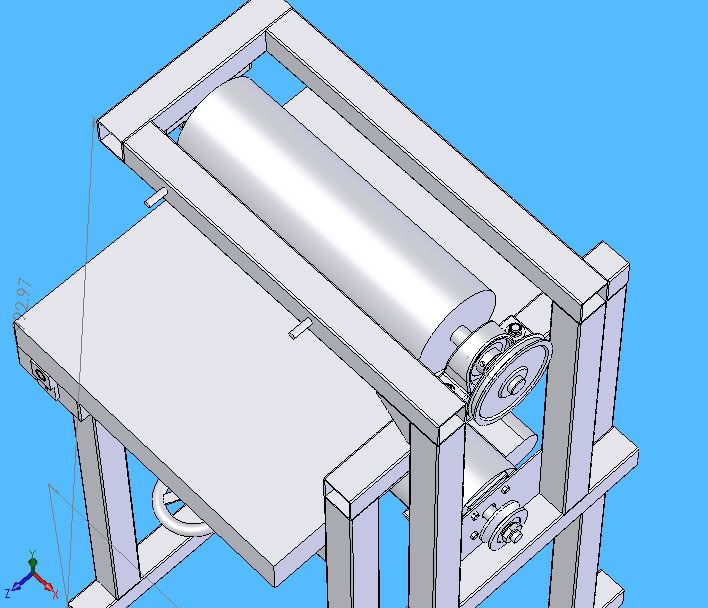
The gantry, like the rest will be made of 40mm box, reinforced with fillets at the corners.
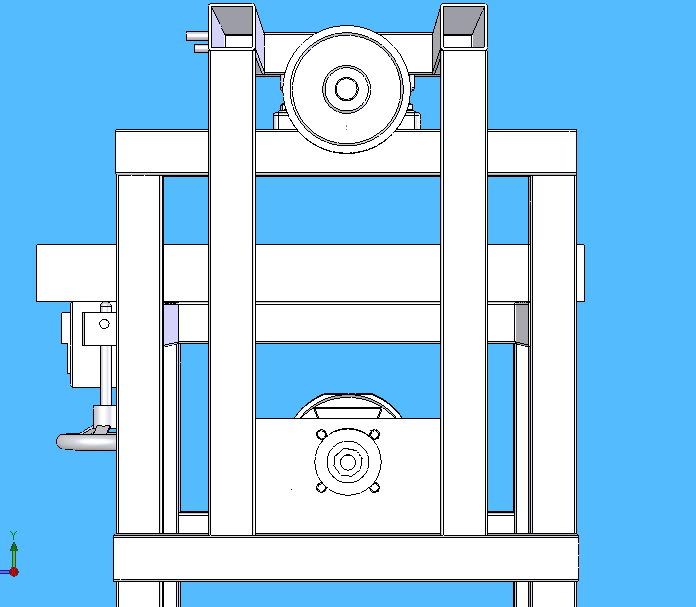
The motor runs at 2950RPM, far too fast for a direct or 1:1 ratio, thus the drum having a diameter of 4" will need a 4" pulley, so, with a 2.25" pulley on the motor that will give an RPM of about 1400-1500.
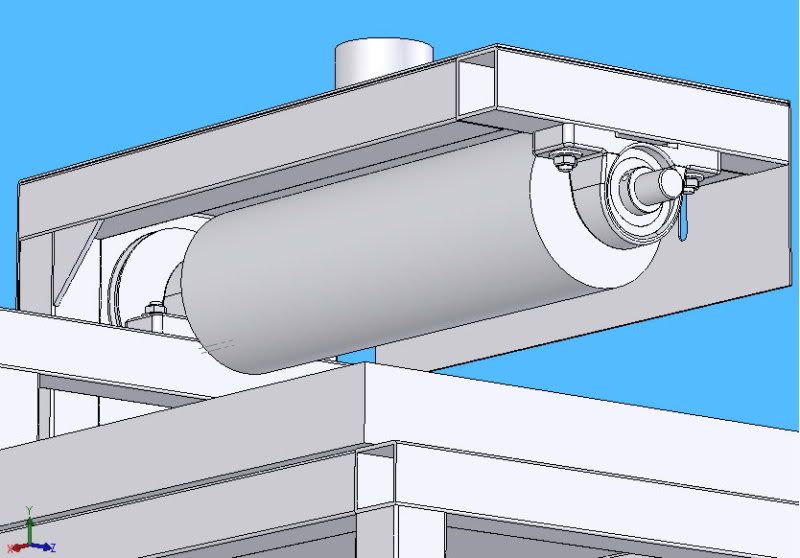
Underview of sanding drum. The drum is approx 14" long. The pillow block on the 'open' side will need to be inverted.
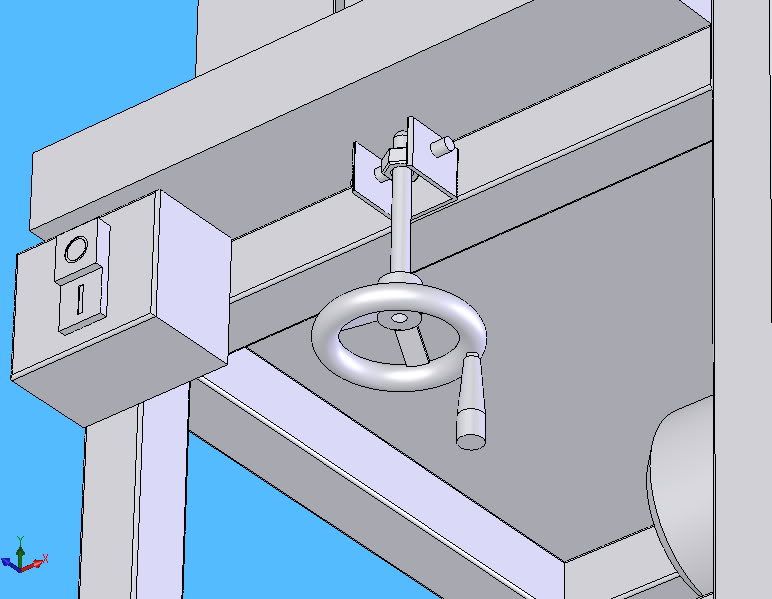
The tilt mechanism for the table. As this is a 'simple' home build the means of adjusting the table for thickness will be done via a crank handle which will raise the table nearer the drum (it will be hingle at the opposite end).
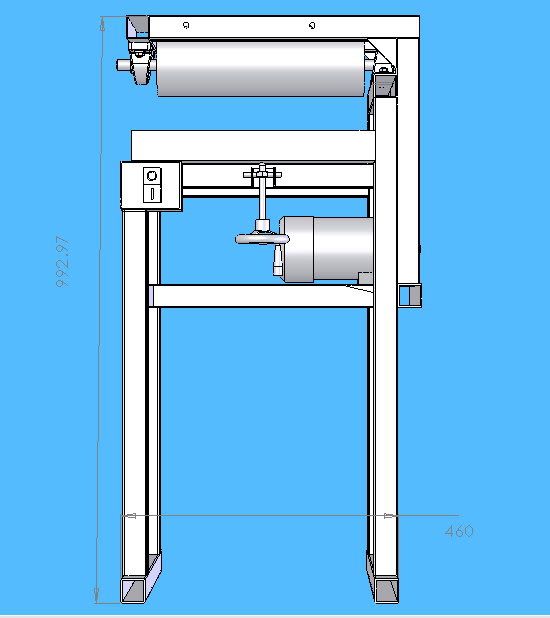
Infeed/front view. The power switch, motor, crank handle are all donors from the aldi saw!
So there you have it. Seems good in theory, hope it works out! I still have to figure out a tensioning system for the belt as the motor will be fixed in place, but I think I have an idea for that, ie a idler wheel that will put pressure on the belt thereby tensioning it.
Any questions, opinion, help, info, crit etc all welcome! :wink: