After all the feedback received here and elsewhere it is time for action rather than prevarication. I've run up a "dummy" window similar in size to the ones that require replacement just to see what problems I come across, and to try out the hardware before committing myself to oak. All I've sacrificed so far is 6m of 50mm x 100mm and some time. No criticism of "squeeze out" or general standard of finish please - this is to test the concept and will be cannabalised of it's hardware when finished! Nor have I fitted any draft seal but don't anticipate this will cause any problems on the "real thing".
I've based the section on this one rather than the hand drawn one in the original thread.
The sash was built up with 5 laminations alternating at the corners.
OK - I know you can only see 4 laminations, but I've left the final one that will form the "storm proof" final layer until after I've routed out the Eurogroove and fitted the lock.
For the frame I decided to try and reduce the number of laminations from 5 down to 3 by using half lap joints at the corners. After a bit of routing I end up with this.
Then a couple of cuts on the band saw and I have this - looking OK so far.
B******s! I forgot to allow for the glazing recess!
So try again.
OK - that's worked out better.
Forgot to take piccies of the rest of the process - but this is what I've ended up with.
Opened up for internal cleaning, which on the face of it looks good ..........
........... but getting both top and bottom to slide the same distance simultaneously is near impossible, and awkward to get your fingers around the RH side of the window to apply the neccesary pressure. SWMBO won't like.
As Brian (Modernist) correctly predicted, there was insufficient room for the locking handling. This is the result of pinching 5mm from elsewhere, and the sash opens fine ..............
.......... but the handle still fouls the frame when locked in the "night latch" position - which is normal night time position for us.
I'm confident that I can "find" another 3mm which will be more than enough to resolve this problem, but want to resolve the "Easy Clean" issue first. We have some UPVC windows elsewhere which are "easy clean" without having to slide the whole assembly to one side, and there is still room to climb out - I've done it several times when painting the walls, and I'm a bit on the portly side!
This is far preferable to the Reddiseal Egress Easy Clean hinges I've used in this test piece. Anyone have any recommendations as to which of the thousands of hinges that are available offer this type of movement?
I appreciate this is all basic stuff for you professional joiners - but it's cutting edge stuff for a hobbyist like me! Thanks for the advice offered so far. I just need to resolve the handle fouling issue, and source a more suitable hinge before committing to Oak. But identifying and resolving these types of problem was what this excercise was designed to do, so not down hearted.
I've based the section on this one rather than the hand drawn one in the original thread.
The sash was built up with 5 laminations alternating at the corners.
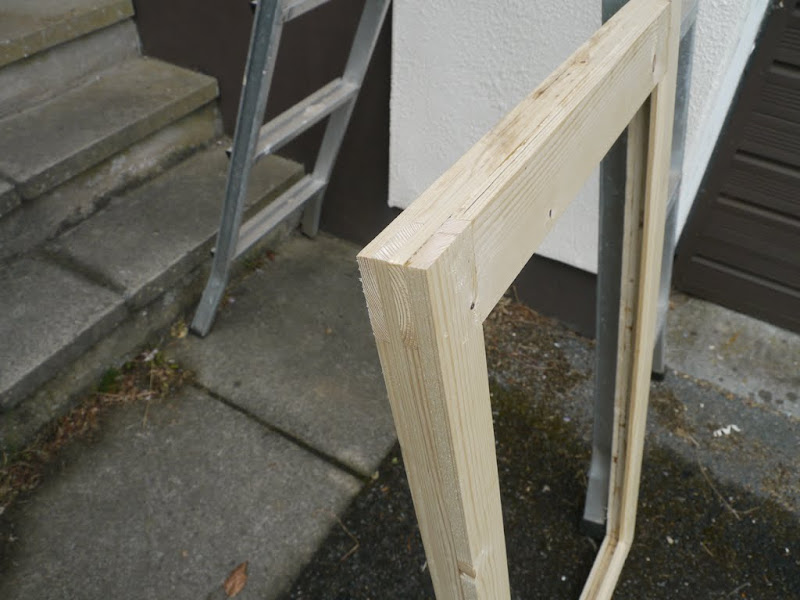
OK - I know you can only see 4 laminations, but I've left the final one that will form the "storm proof" final layer until after I've routed out the Eurogroove and fitted the lock.
For the frame I decided to try and reduce the number of laminations from 5 down to 3 by using half lap joints at the corners. After a bit of routing I end up with this.
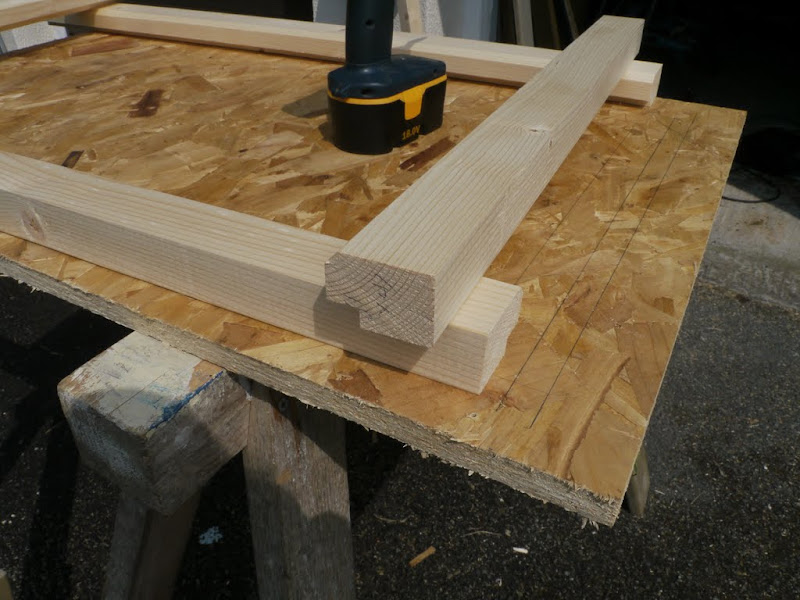
Then a couple of cuts on the band saw and I have this - looking OK so far.
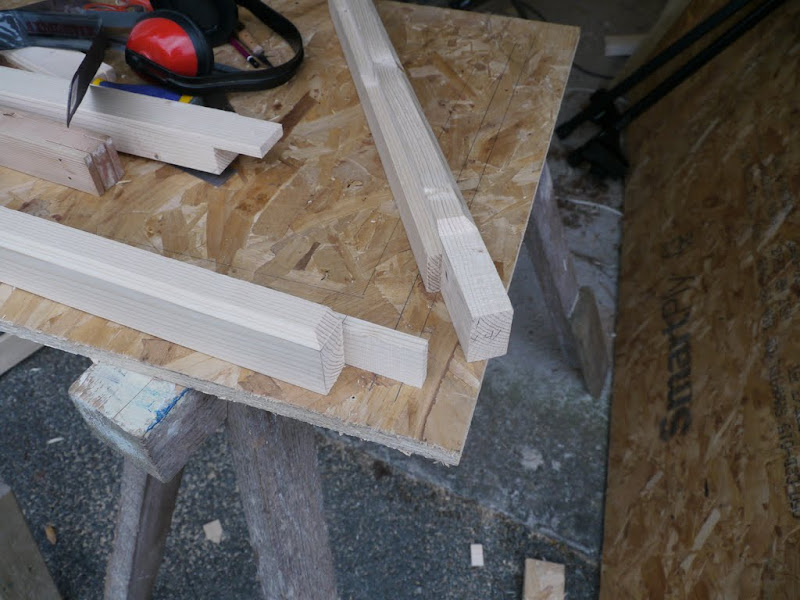
B******s! I forgot to allow for the glazing recess!
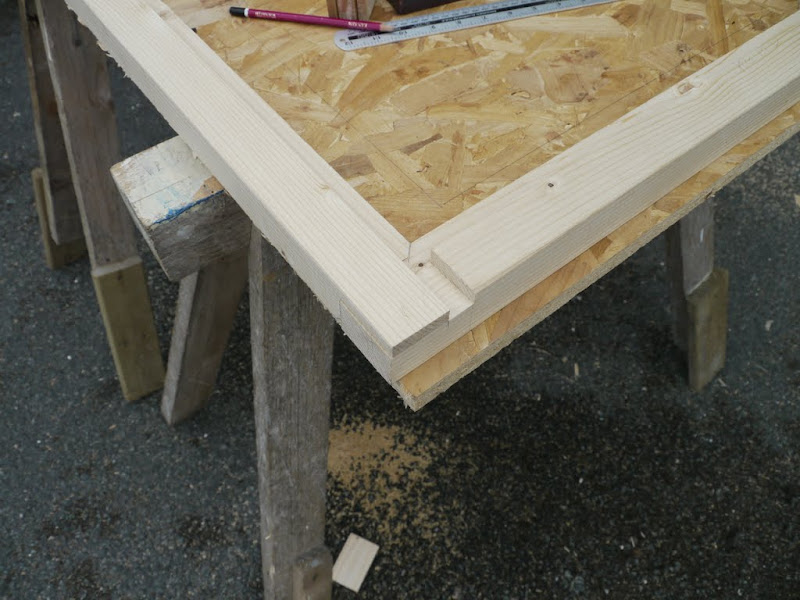
So try again.
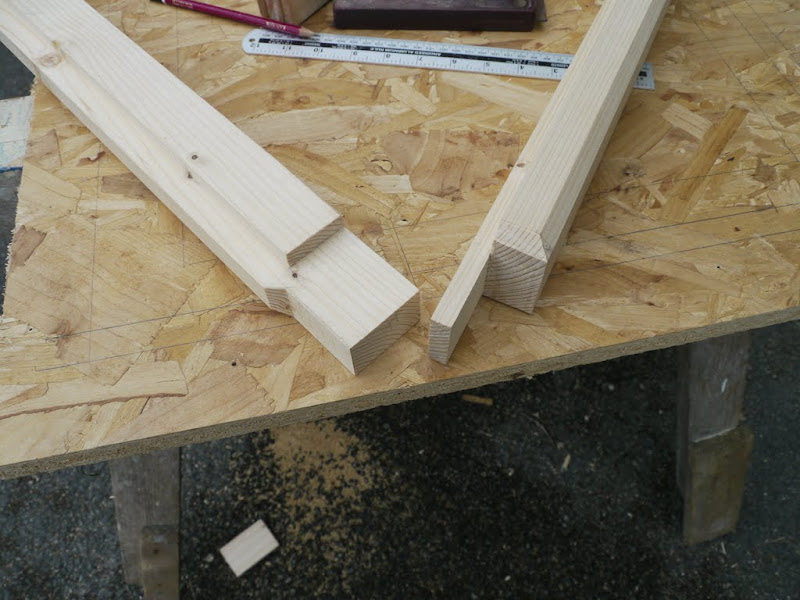
OK - that's worked out better.
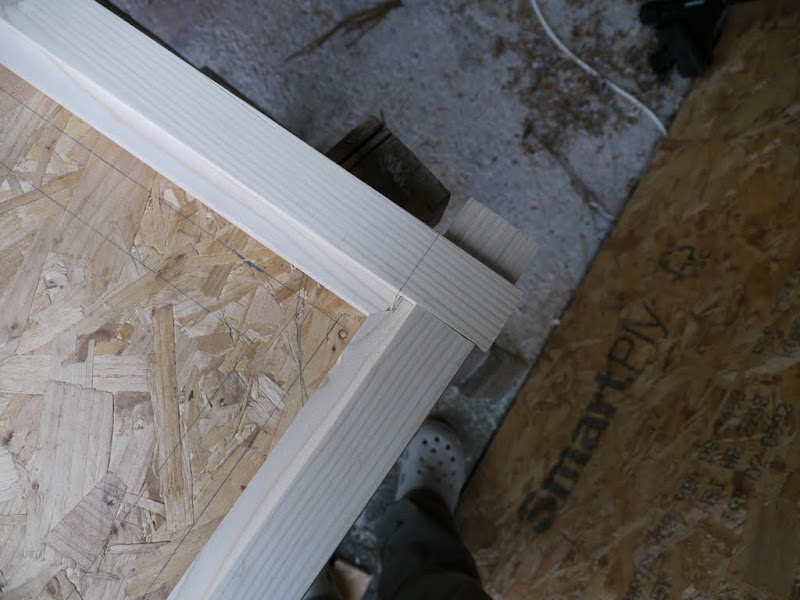
Forgot to take piccies of the rest of the process - but this is what I've ended up with.
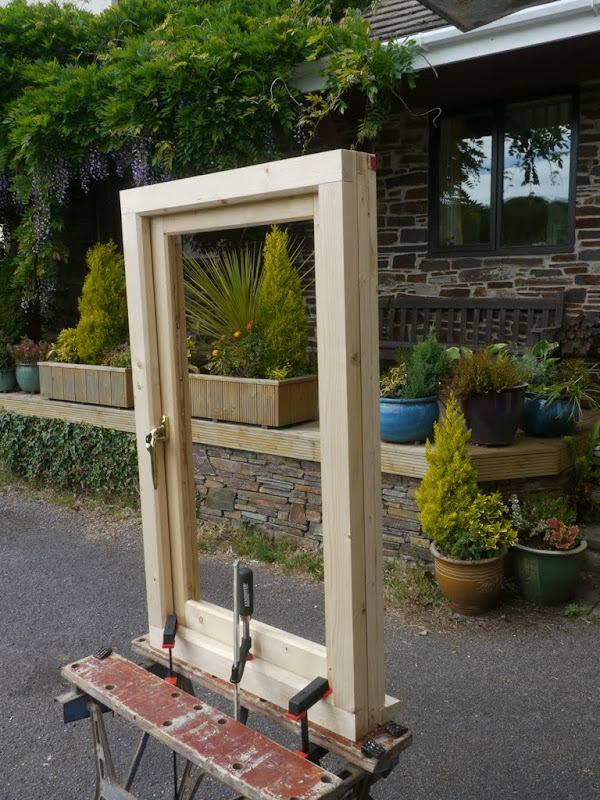
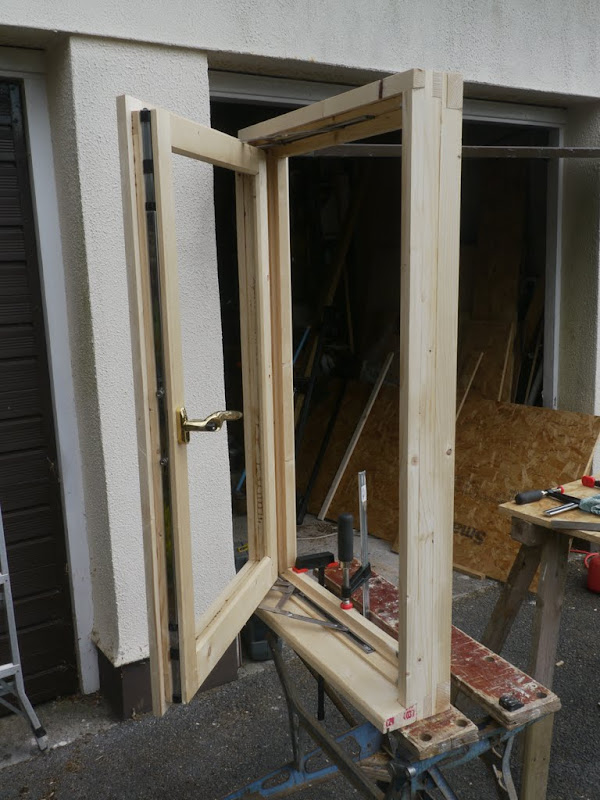
Opened up for internal cleaning, which on the face of it looks good ..........
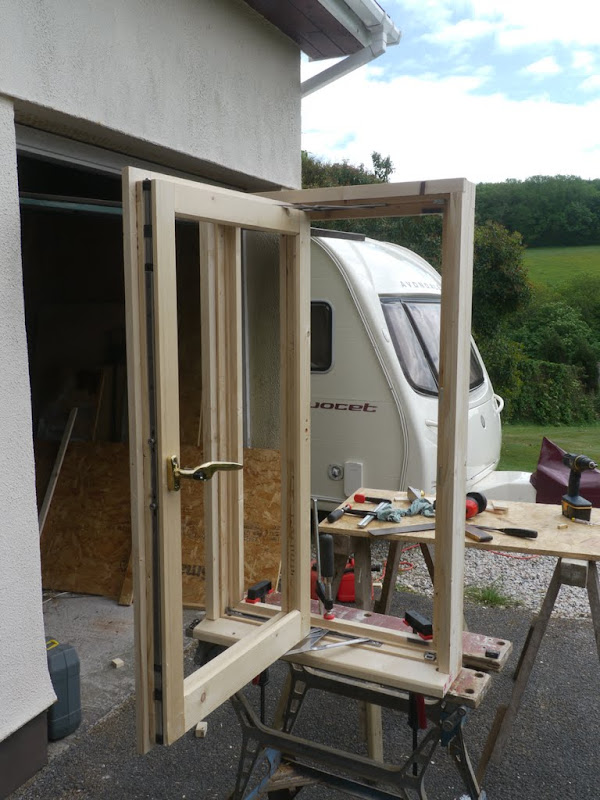
........... but getting both top and bottom to slide the same distance simultaneously is near impossible, and awkward to get your fingers around the RH side of the window to apply the neccesary pressure. SWMBO won't like.
As Brian (Modernist) correctly predicted, there was insufficient room for the locking handling. This is the result of pinching 5mm from elsewhere, and the sash opens fine ..............
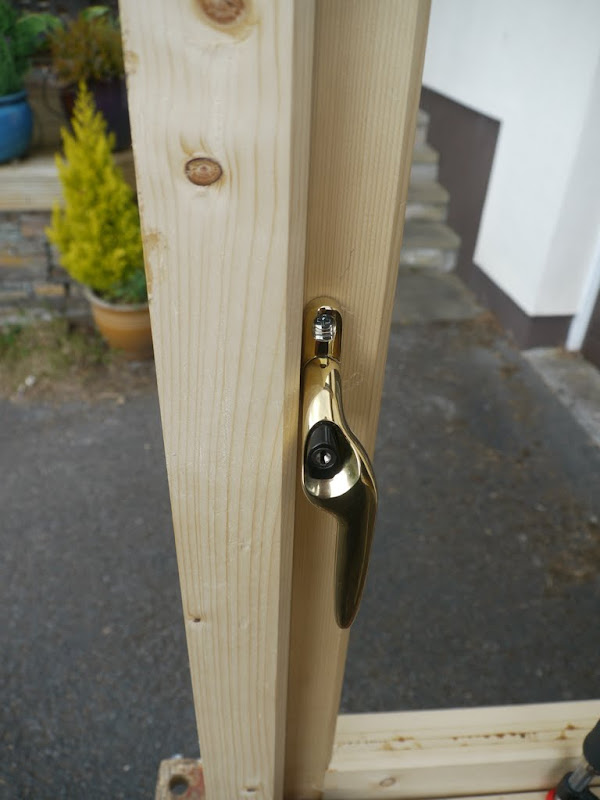
.......... but the handle still fouls the frame when locked in the "night latch" position - which is normal night time position for us.
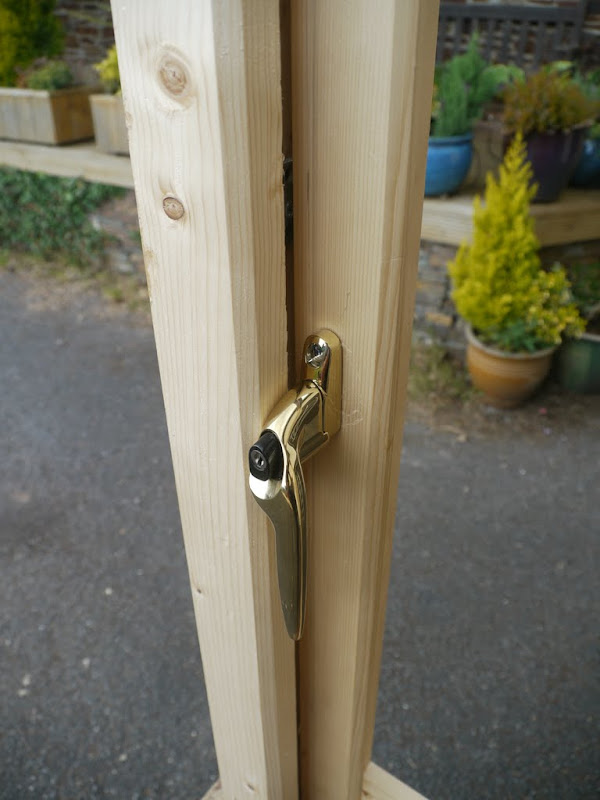
I'm confident that I can "find" another 3mm which will be more than enough to resolve this problem, but want to resolve the "Easy Clean" issue first. We have some UPVC windows elsewhere which are "easy clean" without having to slide the whole assembly to one side, and there is still room to climb out - I've done it several times when painting the walls, and I'm a bit on the portly side!
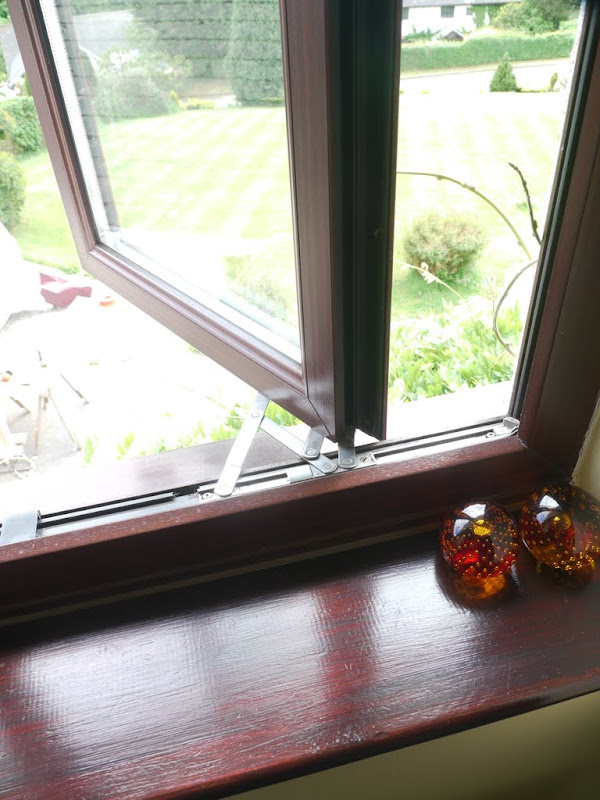
This is far preferable to the Reddiseal Egress Easy Clean hinges I've used in this test piece. Anyone have any recommendations as to which of the thousands of hinges that are available offer this type of movement?
I appreciate this is all basic stuff for you professional joiners - but it's cutting edge stuff for a hobbyist like me! Thanks for the advice offered so far. I just need to resolve the handle fouling issue, and source a more suitable hinge before committing to Oak. But identifying and resolving these types of problem was what this excercise was designed to do, so not down hearted.