Hi all.
I managed to salvage a no7 plane base from a skip and thought id like to make a new handle and knob for it. Something a bit different so i stuck lots of ash and jarrah pieces together.
Very new to this lathe turning malarchy. When i was trying to turn the knob with a small gouge chisel, it kept biting in and splitting small chunks off.(doing the red section in the picture was the worst)
Managed to finish it using a skew chisel and 80grit, but ended up not getting the shape i really wanted. Was hoping to make another one and was wondering if you could give me any tips on how to do it properly :wink:
Really wasnt much fun trying to turn this end grain
Thanks
Simon
I managed to salvage a no7 plane base from a skip and thought id like to make a new handle and knob for it. Something a bit different so i stuck lots of ash and jarrah pieces together.
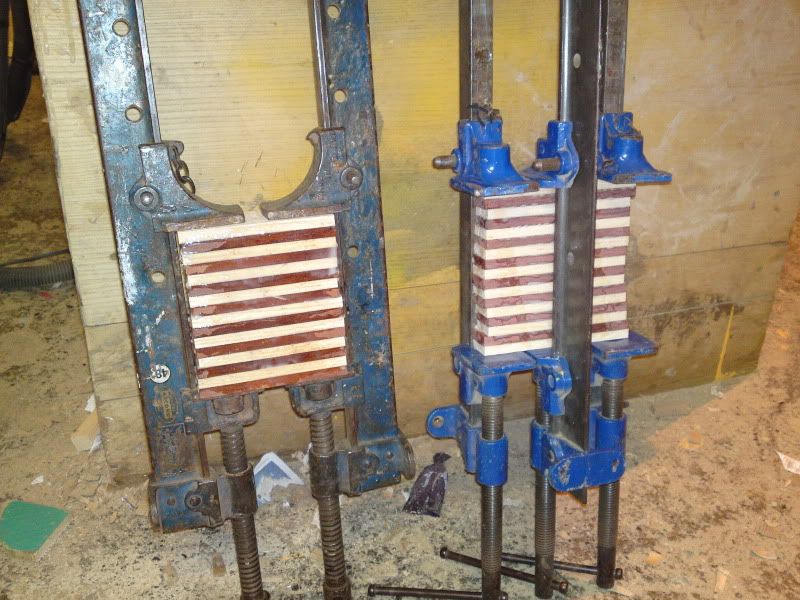
Very new to this lathe turning malarchy. When i was trying to turn the knob with a small gouge chisel, it kept biting in and splitting small chunks off.(doing the red section in the picture was the worst)
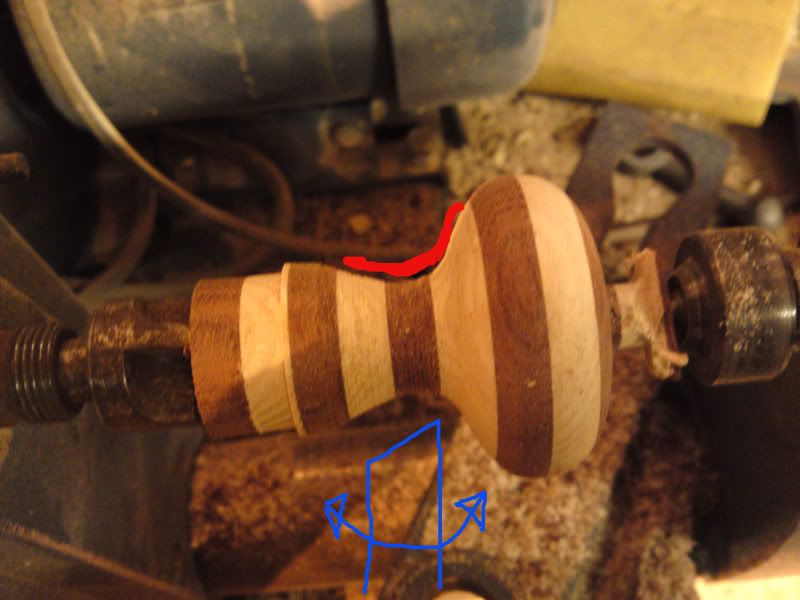
Managed to finish it using a skew chisel and 80grit, but ended up not getting the shape i really wanted. Was hoping to make another one and was wondering if you could give me any tips on how to do it properly :wink:
Really wasnt much fun trying to turn this end grain
Thanks
Simon