TheTiddles
Established Member
That'll screw up the search engines!
Cutting up sheet materials is something I'm doing quite a bit now and supporting it evenly and allowing access is really important so the baby Mafell can get its teeth into it.
Obviously I could have a large table area set aside for this purpose but where would be the fun in that? So saw horses it is, designed to be as cheap, simple and compact as possible when not in use. So with a little inspiration and "a few clicks of your spondulicks" as someone says we have a design intended to be made from a single sheet of 18mm ply. Simply scale by 0.1, procure an A5 size piece of 2mm acrylic (which conveniently happens to be 1.8mm) and tickle with a CO2 laser till you have something like this...
Which when assembled in the correct order, looks a bit like this,
The original and most definitely not the best version of saw horses (full marks for effort, none for performance) had a single task left to perform before they were taken outside and sawed to death, making their replacements.
The template (in the top right of the sheet) I made is a thin piece of polythene (as it's what I had left) cut to the exact size and stuck to a piece of 12mm MR-MDF for bulking and to give the guide bush something to run against. I used a bearing guided cutter to trim the MDF to the PE then to make sure it stayed aligned a few countersunk screws in strategic locations. But more of that later,
With the sheet broken down to bite-sized pieces it's time for routing which I'm using my big 1/2" machine for and about three passes per slot.
Here's the finished result, I used a 1/4" radius bearing guided cutter in my smaller router to ease the edges, by the time I'd finished all that routing I had vibration blisters on two of my fingers and they "rang" when I pinched my fingers together, never had that happen before.
So, with it all structurally complete I needed to check it for strength, which was potentially hazardous, but thankfully a local ner-do-well was on hand and was easily persuaded to take the risk with a bottle of super-strength cider and some magic beans.
Job done, all in about £20 and a couple of hours work. It takes up very little space, is easily transported and is really rather splendid. Happy with that.
Aidan
Cutting up sheet materials is something I'm doing quite a bit now and supporting it evenly and allowing access is really important so the baby Mafell can get its teeth into it.
Obviously I could have a large table area set aside for this purpose but where would be the fun in that? So saw horses it is, designed to be as cheap, simple and compact as possible when not in use. So with a little inspiration and "a few clicks of your spondulicks" as someone says we have a design intended to be made from a single sheet of 18mm ply. Simply scale by 0.1, procure an A5 size piece of 2mm acrylic (which conveniently happens to be 1.8mm) and tickle with a CO2 laser till you have something like this...
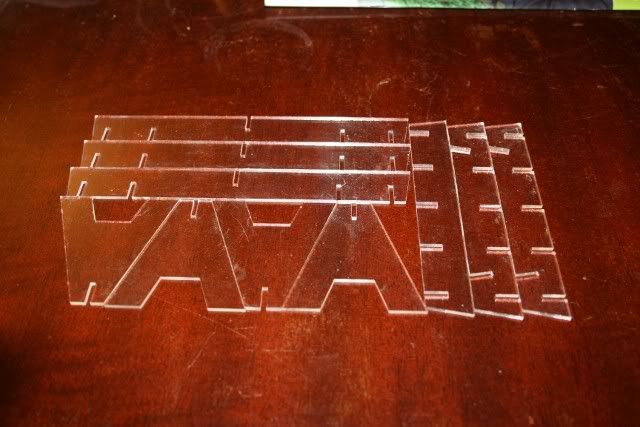
Which when assembled in the correct order, looks a bit like this,
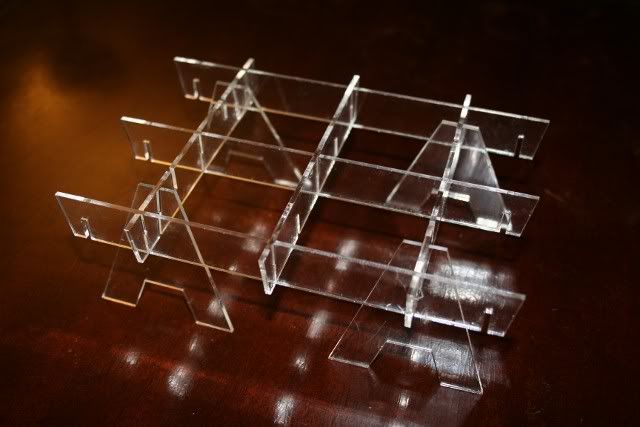
The original and most definitely not the best version of saw horses (full marks for effort, none for performance) had a single task left to perform before they were taken outside and sawed to death, making their replacements.
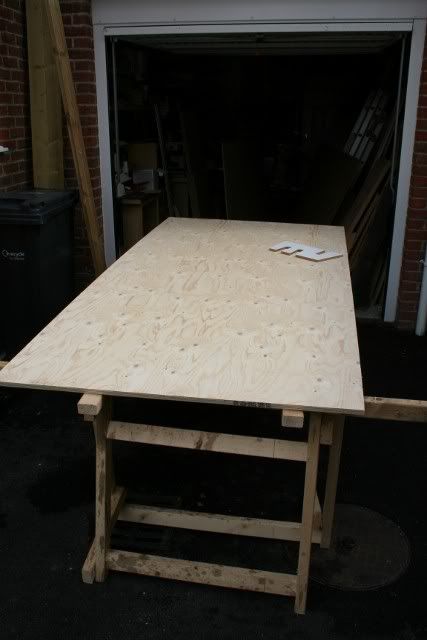
The template (in the top right of the sheet) I made is a thin piece of polythene (as it's what I had left) cut to the exact size and stuck to a piece of 12mm MR-MDF for bulking and to give the guide bush something to run against. I used a bearing guided cutter to trim the MDF to the PE then to make sure it stayed aligned a few countersunk screws in strategic locations. But more of that later,
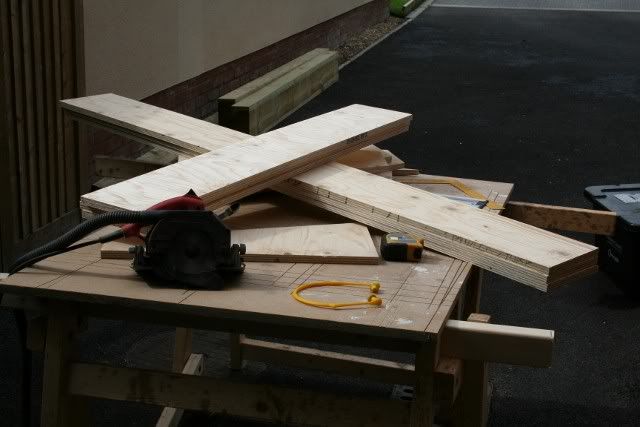
With the sheet broken down to bite-sized pieces it's time for routing which I'm using my big 1/2" machine for and about three passes per slot.
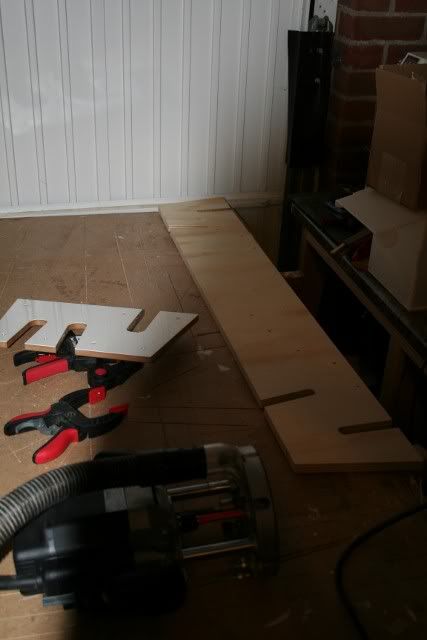
Here's the finished result, I used a 1/4" radius bearing guided cutter in my smaller router to ease the edges, by the time I'd finished all that routing I had vibration blisters on two of my fingers and they "rang" when I pinched my fingers together, never had that happen before.
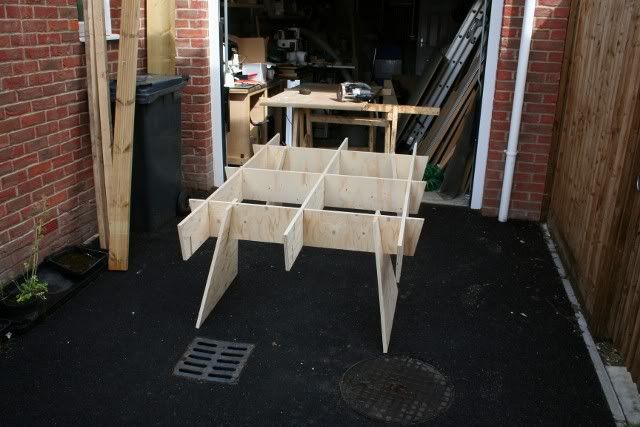
So, with it all structurally complete I needed to check it for strength, which was potentially hazardous, but thankfully a local ner-do-well was on hand and was easily persuaded to take the risk with a bottle of super-strength cider and some magic beans.
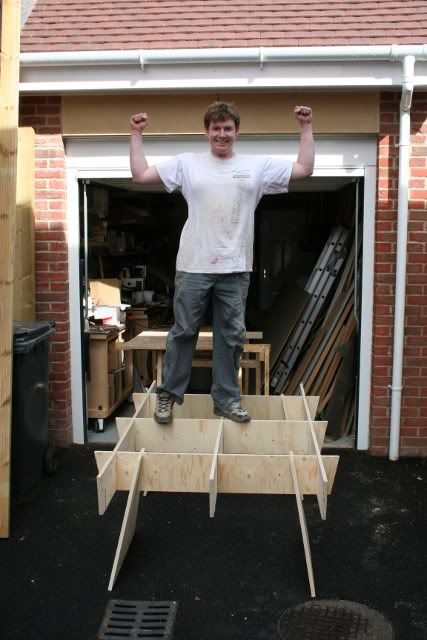
Job done, all in about £20 and a couple of hours work. It takes up very little space, is easily transported and is really rather splendid. Happy with that.
Aidan