stuartpaul
Established Member
Well, - I've asked enough questions on this forum I thought it about time I actually started some woodwork!
I'm as determined as I can be to try and keep a WIP all the way through, - a novel thing for me to attempt but here goes.
I knew that I'd be using sliding dovetails so the last few weekends have been spent on Mr M's mortice jig:
I'm reasonable happy that this will enable the sliding dovetails to be relatively straightforward (I might end up regretting that statement!).
The design:
The client (MIL) knows nothing about woodwork but knows what she wants! An oval pedestal table. The only constraints were the overall size, no more than 20" high and wide.
Given that I have the design ability of a month old cow pat this bit hasn't been easy for me. I'm OK copying but it's the relationship between proportions that usually causes me problems. After much effort with sketchup I've finally (I think!) settled on a final design.
Now I suspect that many will notice that this isn't in sketchup but mk 1 lining paper. I did have the luxury of a design studio which will also double as my finishing room (SWMBO calls it a dining room). This does give me the benefit of a full size drawing which I always do anyway.
I'm not 100% convinced with all the dimensions and there may well be some 'adjustments' on route. I'll see how things go.
The size of the top is dictated by the final width so with pins and string I end up with a top that's 20 x 30" (the inner line). Appears to be about right.
Material:
One of my biggest woodworking 'kicks' is from recycling old timber. This time it's an old victorian dining table (broken up by others) which should provide plenty of material. At a little over 3/4" I should be able to remove the finish and have some nice mahogany to play with.
Unfortunately the panels are suffering from some degree of bowing, probably due to me leaving them leant against the garage wall. This may mean have to cut and rejoin to get the top flat.
The legs for the dining table have quite a lot of molding on them but with a minimum diameter of 3" I'm hoping to be able to turn the pedestal from one. With a bit of luck I might be able to retain some of the molding in the final version. As I've got 4 there is room for experimenting!
This morning was spent 'recommissioning' the lathe which would have been much easier if I'd actually decommissioned it! It's been sat virtually untouched for about 5 years. The odd switch on to make sure it still worked and exercise belt and bearings but that's about it.
As I clearly haven't done any turning for the same period of time this is going to be a slow and steady part of the project and is where I intend to start.
Now it's either rugby or turning. Hmmmm
Given that this project only involves 7 pieces of wood I find it hard to believe how much effort it's likely to take. I've never taken on anything like this before so I'll be doing some learning on the way.
I'm as determined as I can be to try and keep a WIP all the way through, - a novel thing for me to attempt but here goes.
I knew that I'd be using sliding dovetails so the last few weekends have been spent on Mr M's mortice jig:
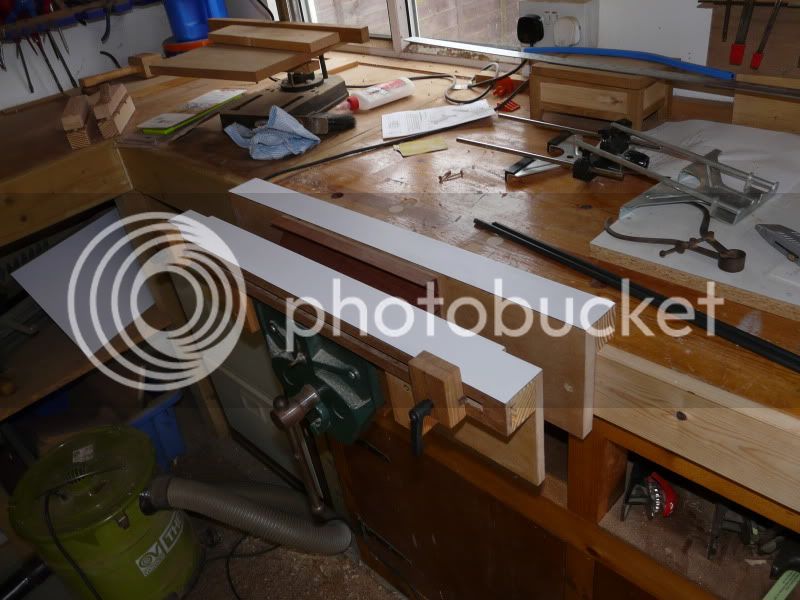
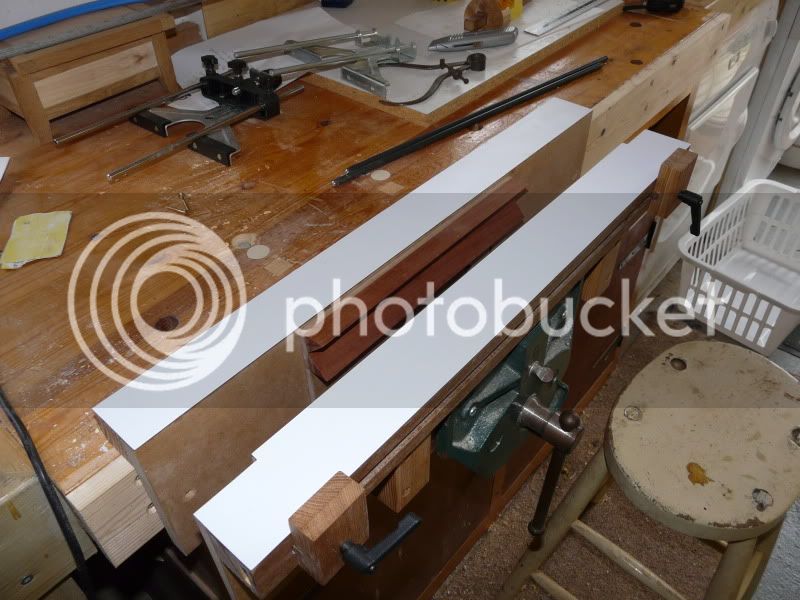
I'm reasonable happy that this will enable the sliding dovetails to be relatively straightforward (I might end up regretting that statement!).
The design:
The client (MIL) knows nothing about woodwork but knows what she wants! An oval pedestal table. The only constraints were the overall size, no more than 20" high and wide.
Given that I have the design ability of a month old cow pat this bit hasn't been easy for me. I'm OK copying but it's the relationship between proportions that usually causes me problems. After much effort with sketchup I've finally (I think!) settled on a final design.
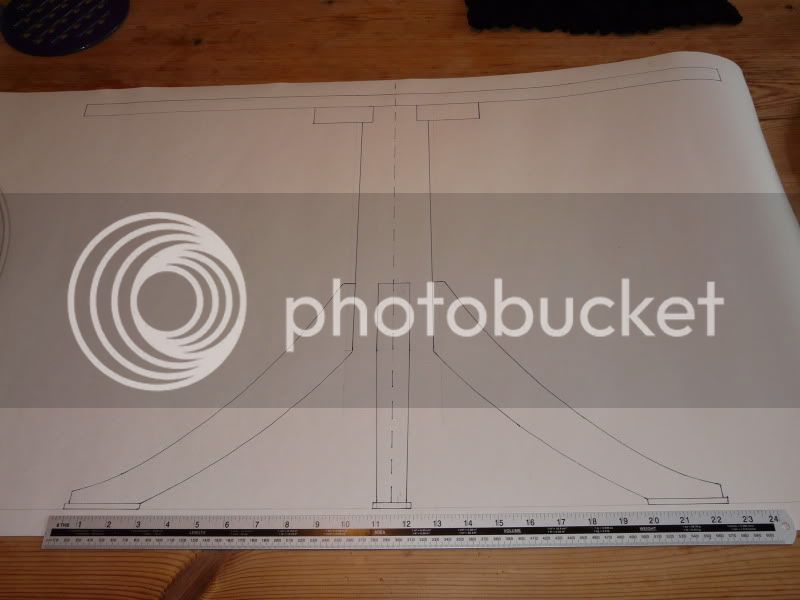
Now I suspect that many will notice that this isn't in sketchup but mk 1 lining paper. I did have the luxury of a design studio which will also double as my finishing room (SWMBO calls it a dining room). This does give me the benefit of a full size drawing which I always do anyway.
I'm not 100% convinced with all the dimensions and there may well be some 'adjustments' on route. I'll see how things go.

The size of the top is dictated by the final width so with pins and string I end up with a top that's 20 x 30" (the inner line). Appears to be about right.
Material:
One of my biggest woodworking 'kicks' is from recycling old timber. This time it's an old victorian dining table (broken up by others) which should provide plenty of material. At a little over 3/4" I should be able to remove the finish and have some nice mahogany to play with.
Unfortunately the panels are suffering from some degree of bowing, probably due to me leaving them leant against the garage wall. This may mean have to cut and rejoin to get the top flat.
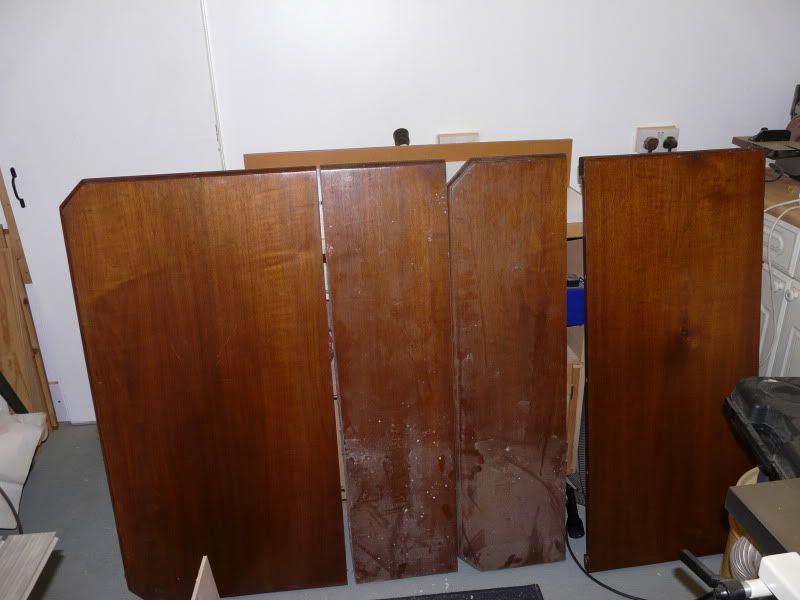
The legs for the dining table have quite a lot of molding on them but with a minimum diameter of 3" I'm hoping to be able to turn the pedestal from one. With a bit of luck I might be able to retain some of the molding in the final version. As I've got 4 there is room for experimenting!
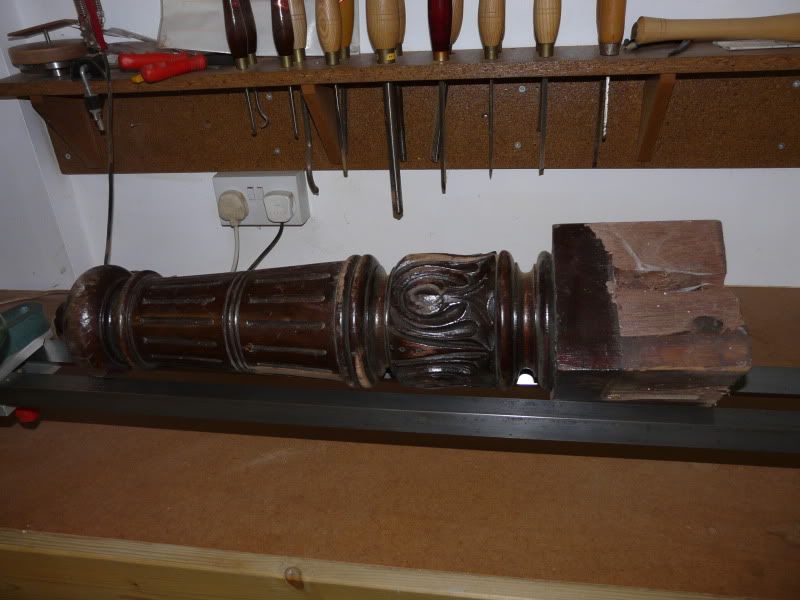
This morning was spent 'recommissioning' the lathe which would have been much easier if I'd actually decommissioned it! It's been sat virtually untouched for about 5 years. The odd switch on to make sure it still worked and exercise belt and bearings but that's about it.
As I clearly haven't done any turning for the same period of time this is going to be a slow and steady part of the project and is where I intend to start.
Now it's either rugby or turning. Hmmmm
Given that this project only involves 7 pieces of wood I find it hard to believe how much effort it's likely to take. I've never taken on anything like this before so I'll be doing some learning on the way.