Pekka Huhta
Established Member
I started building an infill plane in 2009. It all started when I had an idea for a new adjusting mechanism and I wanted to build a plane around it. Another major idea for the plane came from UKWorkshop when I saw the infill smoother Aled was building. It had a screw-on construction, and as I have been building different planes with adjustable mouths, I figured out that it would be dead simple to build an infill plane with an adjustable mouth just by bolting the "sole" in front of the mouth 10 mm higher and inserting the sliding mouthpiece just below it. I almost felt stupid for not figuring it out earlier, it was so obvious
Although I love old tools, I sometimes dislike the... ornaments, in lack of a better word. Look at the side of an old Norris or Spiers. If you look at the shapes and not at the tool, you just see a quite clumsy wave shape in the side. The tool itself is beautiful, but the details are not. It's not a flowing line, not particularly ergonomic, there is nothing to explain why it is what it is. So I wanted the lines of my plane to be flowing, smooth, and that created the very simple side line of the plane. A tad of Finnish Design, if you like
As I could not decide what width I wanted, I decided to build two different planes, for 2¼" and 2½" irons.
I made a set of drawings, but I wanted to see how the plane felt to my hand, so I built a quick mock-up from plywood and workshop offcuts.
I have a friend who got the parts laser cut in his company. I was able to machine the sides of the soles + all the fixing holes at my previous job. After that I just started putting things together. The holes were chamferred and the whole frame bolted together. I also noticed that you should not put too deep chamfers there: first set of sides was ruined by too deep chamfers, as you could not file the slots in screwheads off. Also, the screws had to be with a straight slot, as the phillips slots were so deep that you had to file away the whole head before the slot disappeared.
I used acid to dissolve the zinc coating on screws as I figured out that the zinc could show as a narrow ring around the screw head. And while I was at it, I also hammered the screw heads flat, to make sure that the screws fit perfectly in the hand-drilled chamfers.
Next thing was the handles. I had a lump of Karelian birch and I sawed the infills and handles out of it. The wood is beautiful, but if you look at the picture where I have split the wood you can see that there is absolutely no grain orientation (other than "every way"). You need pretty sharp tools with that stuff.
The knobs were turned with my small lathe. It may be pretty, but it isn't particularly practical. I ended up turning both of the knobs at the same time to save time. I drilled the hole for the screw first and centered the blank around that hole, as i knew thet I could not drill the hole to the center afterwards. I only drilled the bigger hole for the fixing part after sawing the knobs off.
...and that was it from 2009. There were multiple problems: I had designed the sides slightly wrong so that the lever cap hole was about 3-4 mm misplaced, which made the levercap look like shait as it was sticking almost vertcally up if I tightened the screw. The knobs were far too high and both looked and felt awful. The Karelian birch was not totally dry and the infills shrunk so that there was a 0,5 mm gap all around the infill. I also wanted to make my own castings and I needed a forge. So I built a forge, which took about a year to finish and then I just let the whole project sit on the shelf to wait for inspiration.
And on the contrary what you would expect: lo and behold, the inspiration came a few months ago (hammer) I had just finished my oak bookcase and wanted to do something else before starting a new renovation project in the house.
I will try to update as I go. I have now cast the lever caps (will have to edit the pics before posting) and turned a new knob. And built the new adjuster mechanism. Now it's time to finish the infill for the first plane and start putting things together...
Pekka
Although I love old tools, I sometimes dislike the... ornaments, in lack of a better word. Look at the side of an old Norris or Spiers. If you look at the shapes and not at the tool, you just see a quite clumsy wave shape in the side. The tool itself is beautiful, but the details are not. It's not a flowing line, not particularly ergonomic, there is nothing to explain why it is what it is. So I wanted the lines of my plane to be flowing, smooth, and that created the very simple side line of the plane. A tad of Finnish Design, if you like
I made a set of drawings, but I wanted to see how the plane felt to my hand, so I built a quick mock-up from plywood and workshop offcuts.
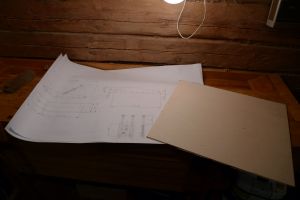
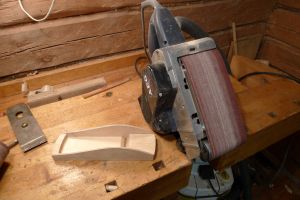
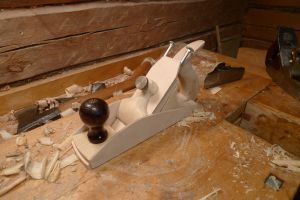
I have a friend who got the parts laser cut in his company. I was able to machine the sides of the soles + all the fixing holes at my previous job. After that I just started putting things together. The holes were chamferred and the whole frame bolted together. I also noticed that you should not put too deep chamfers there: first set of sides was ruined by too deep chamfers, as you could not file the slots in screwheads off. Also, the screws had to be with a straight slot, as the phillips slots were so deep that you had to file away the whole head before the slot disappeared.
I used acid to dissolve the zinc coating on screws as I figured out that the zinc could show as a narrow ring around the screw head. And while I was at it, I also hammered the screw heads flat, to make sure that the screws fit perfectly in the hand-drilled chamfers.
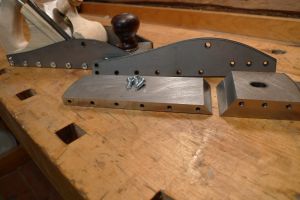
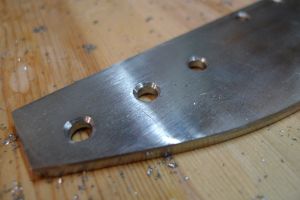
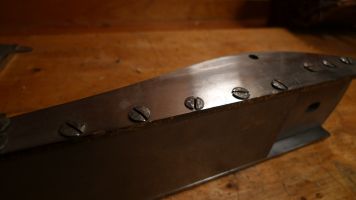
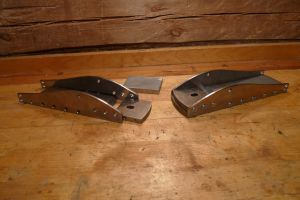
Next thing was the handles. I had a lump of Karelian birch and I sawed the infills and handles out of it. The wood is beautiful, but if you look at the picture where I have split the wood you can see that there is absolutely no grain orientation (other than "every way"). You need pretty sharp tools with that stuff.
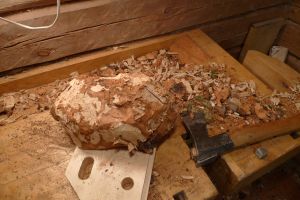
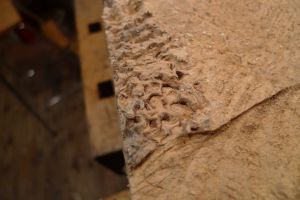
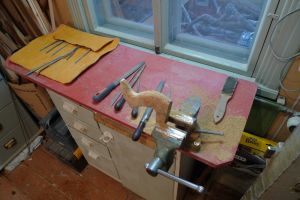
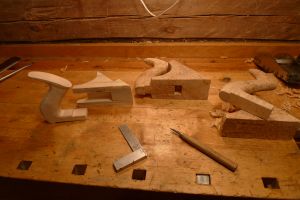
The knobs were turned with my small lathe. It may be pretty, but it isn't particularly practical. I ended up turning both of the knobs at the same time to save time. I drilled the hole for the screw first and centered the blank around that hole, as i knew thet I could not drill the hole to the center afterwards. I only drilled the bigger hole for the fixing part after sawing the knobs off.
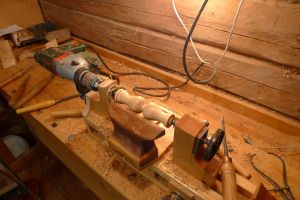
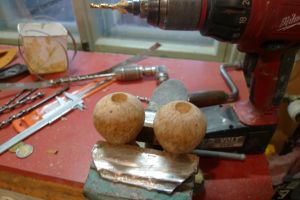
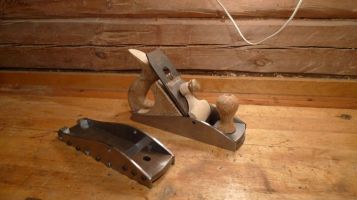
...and that was it from 2009. There were multiple problems: I had designed the sides slightly wrong so that the lever cap hole was about 3-4 mm misplaced, which made the levercap look like shait as it was sticking almost vertcally up if I tightened the screw. The knobs were far too high and both looked and felt awful. The Karelian birch was not totally dry and the infills shrunk so that there was a 0,5 mm gap all around the infill. I also wanted to make my own castings and I needed a forge. So I built a forge, which took about a year to finish and then I just let the whole project sit on the shelf to wait for inspiration.
And on the contrary what you would expect: lo and behold, the inspiration came a few months ago (hammer) I had just finished my oak bookcase and wanted to do something else before starting a new renovation project in the house.
I will try to update as I go. I have now cast the lever caps (will have to edit the pics before posting) and turned a new knob. And built the new adjuster mechanism. Now it's time to finish the infill for the first plane and start putting things together...
Pekka