Dodge
Established Member

Ok, I often get asked for items to give as retirement gifts etc and I have made alot of these so here goes if you fancy having a go at making one - They are really easy! I started making these when I used to demonstrate for Triton more years ago than I care to remember - seriously they are really easy to make.
You will need some timber of your choice, 2 metres of 4mm inlay banding again of your choice
You will also want the following parts from a clock supplier - I used Martin Dunn at the Clock Gallery - The bits cost a total of £36.30 inc VAT & Delivery)
1 x 94mm Wide Brass Loop Handle (A2080)
4 x 10mm Small Brass Ogee Feet (A2157)
1 x 103mm Insertion Movement (Q1103R)
Ok Here we go!
Firstly take a lump of timber, I used Oak, and chop a lump that you can finish to 250mm x 150mm x 70mm

Surface, thickness and cut to length.
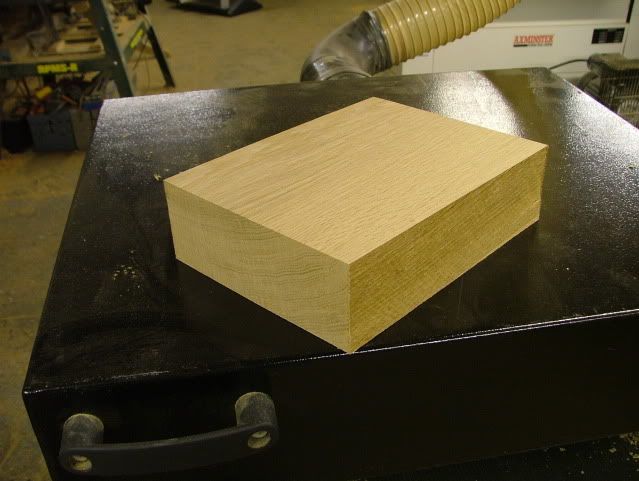
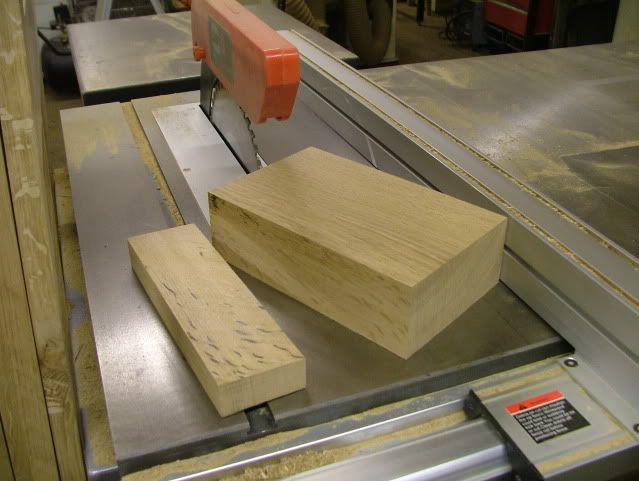
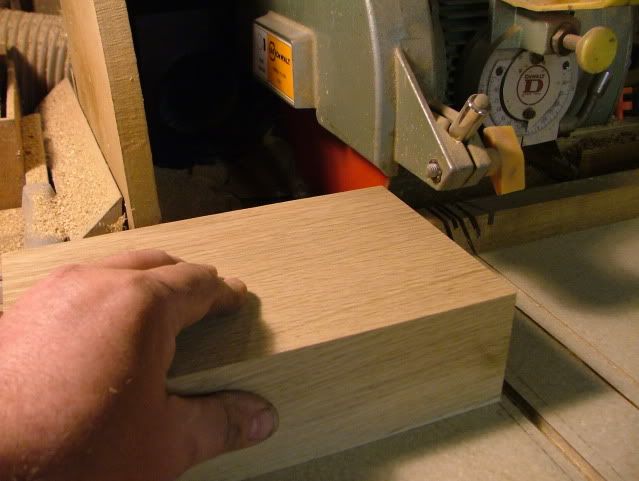
Next drill a 60mm diameter hole to accept the movement - I used an expanding bit in the pillar drill but sawtooth or similar will be fine
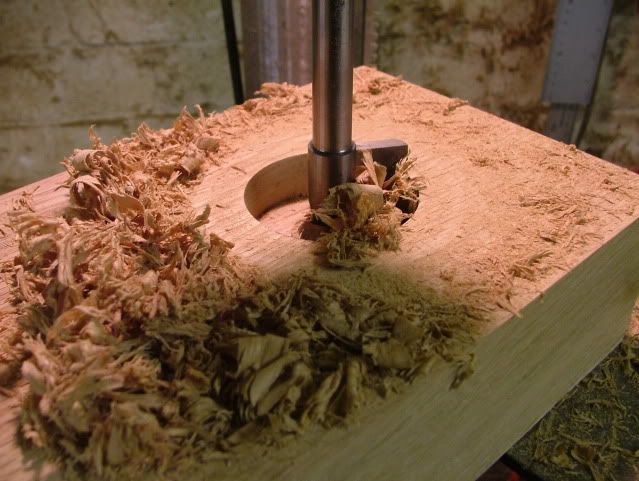
Next rout a 4mm groove around the front and side faces of the block to accept inlay banding
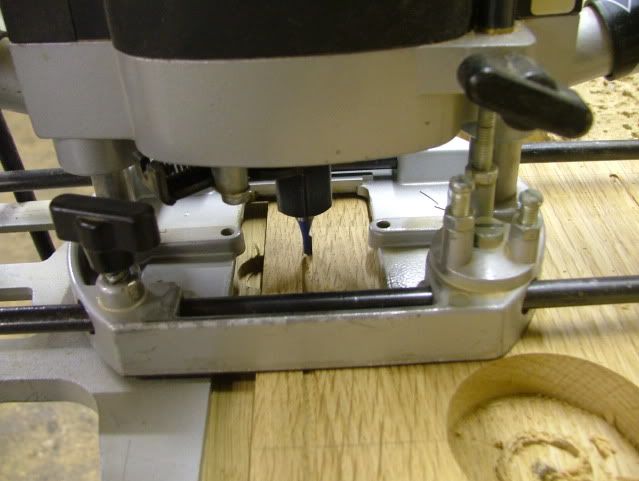
You will need to square the corners with a corner chisel - or normal bevel edges chisel - its up to you
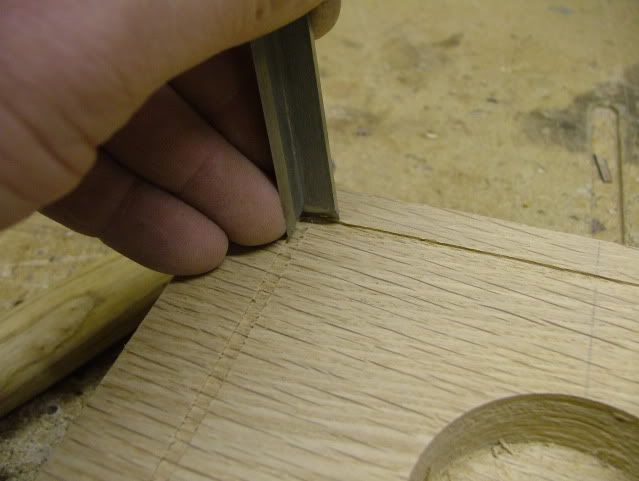
You can now cut the inlay banding, i used some left over kingwood banding
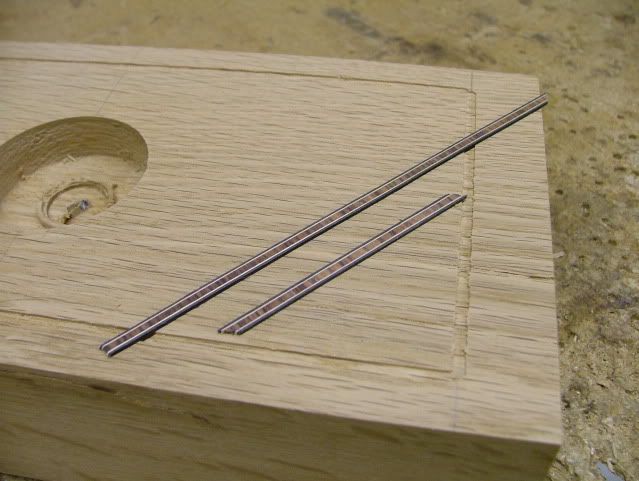
The inlay was then glued in using titebond glue and after all sides were done the excess was sanded off with the random orbit sander but you could use a cabinet scraper if preferred. You only need to leave it for about 15 mins so by the time you have done all sides they are ready to sand.
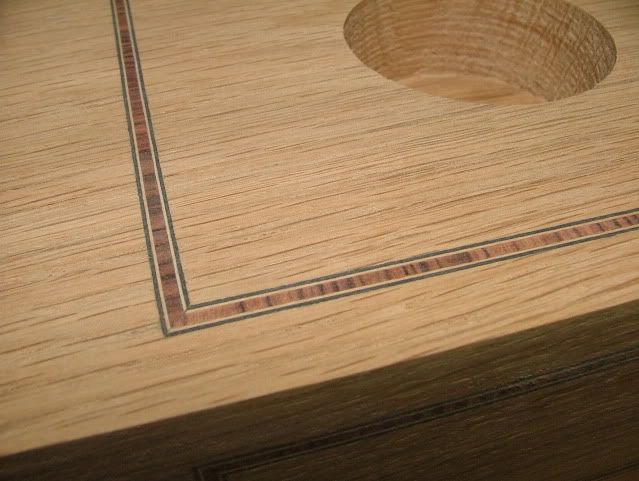
With the inlays in place I then routed the corners using a cock bead cutter like this
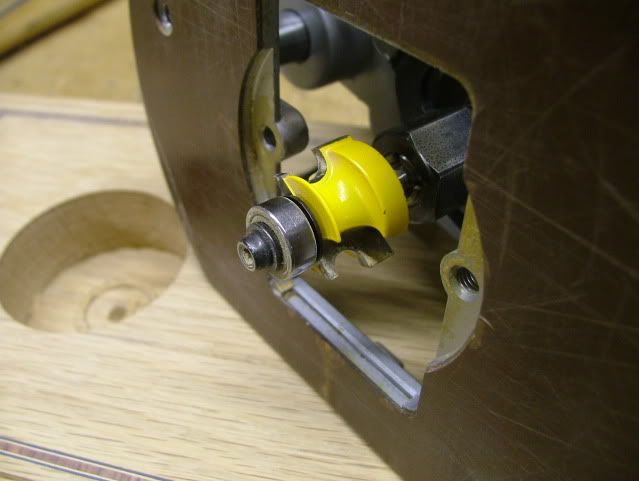
To produce a fake column on each of the corners
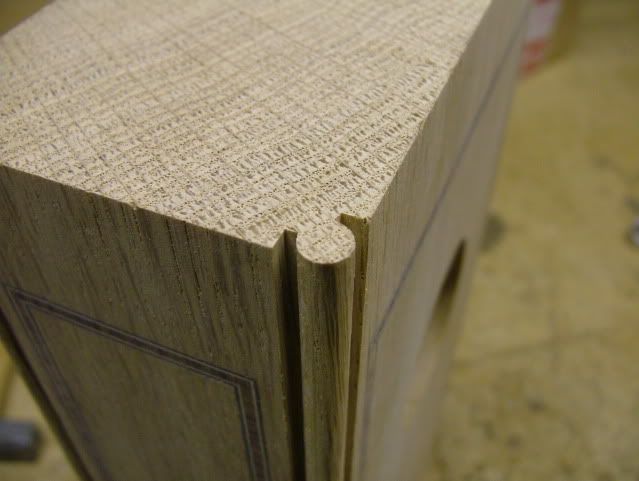
The basic centre of the clock is now complete
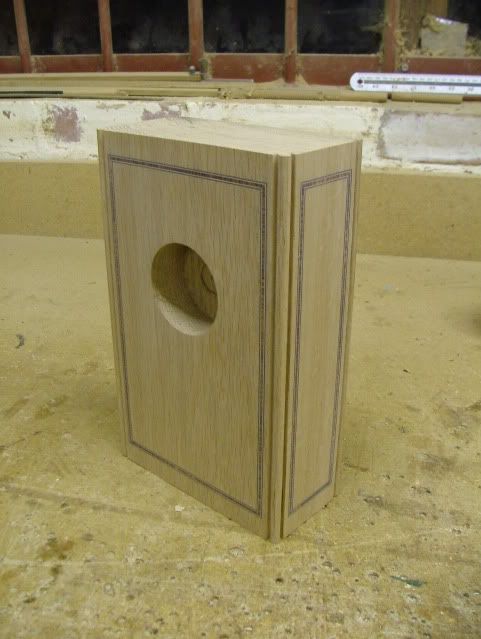
Next cut 2 pieces of timber 166mm x 86mm x 16mm to form the top and bottom of the clock, these can be routed with a cutter of your choice
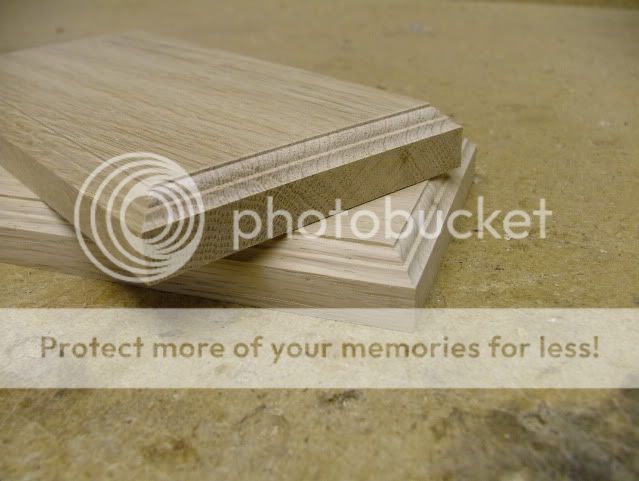
The piece that is to be used for the bottom needs some stop chamfers routed on it to line up to where the brass corner feet will be screwed.
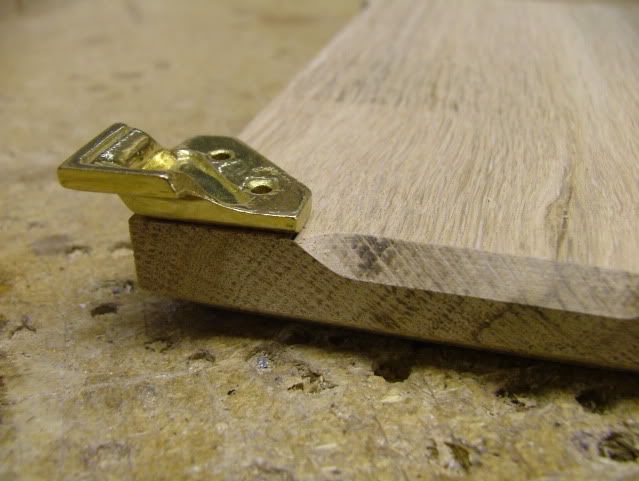
This bottom piece can then be screwed onto the main block, elongate the screw holes slightly to allow for any movement and the brass feet applied to each corner with some small round head screws.
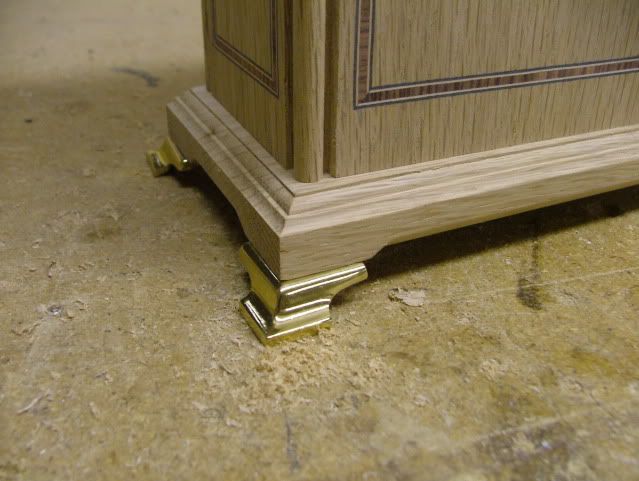
Take the other piece and rout the upper side with a decorative cut and apply another piece to the top measuring 140mm x 60mm x 20mm. Again rout this upper piece to a finished profile.
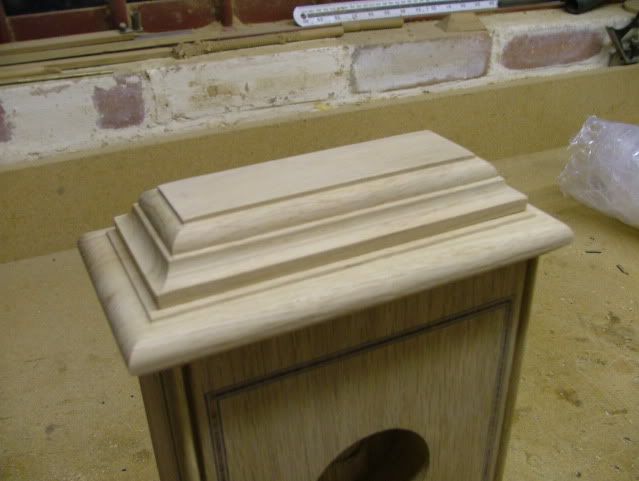
Next drill the holes for the handle through the upper sections and fit the handle countersinking the underside to allow the nuts to sink below the surface of the timber
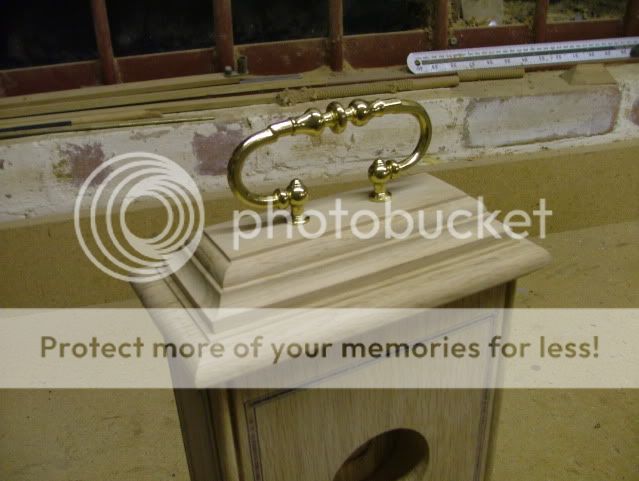
The top needs to be glued on - I appreciate there may be concerns re movement in the main block but if it well seasoned you shouldnt have any problems - I have made alot of these over the years and have never had one move. I used two part mitre glue for convenience/speed
With the brass removed, I then rubbed it down, three coats of celulose sanding sealer and then over waxed with Mylands Light Brown

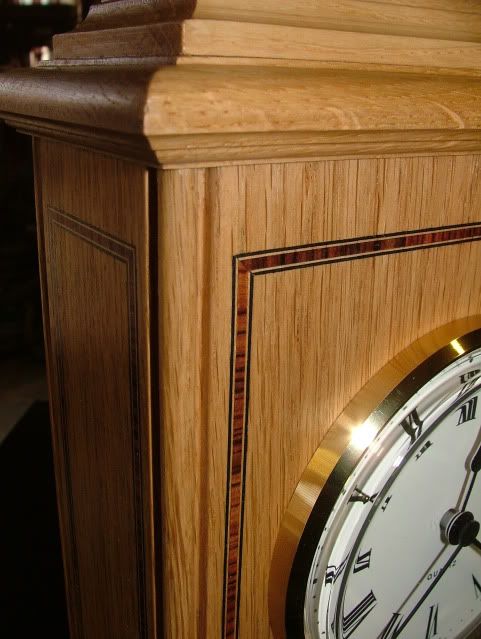
Hope you approve and look forward to seeing pictures of your versions posted here in due course, and yes started and finished in a tad over 3 hours
Rog