jimi43
Established Member
Part war of attrition...part friendship...and mostly encouragement was all I needed to get my backside out into the shop again and make a prototype tool...as "suggested" by our very own Toby...(tobytools)! 8)
So having absolutely no idea where to start...a few more head scratchings and observations of other fine tools lead me to make one...for Toby...a request...and by chance one for me too! (how clever was that!! :wink: )
Steel....O1...of course...3mm ground gauge plate...
Toby requested 6 1/2" of tooth area and a total length of 8" so that's the dimensions. In retrospect...and if I ever make another..I should have cut it a few inches longer, leaving enough steel to use as hold-down space...but it worked out ok...
Handle was to be a tanged version as opposed to scales...so that was marked up too using a chisel as a template.
Now...this is where the pondering starts...I suppose it would have been nice to cut the teeth all by hand or employ piskies to do it for me...but I have long since lost interest in the magic of repetitive tasks like this with hand tools...and there is no way I have the skills to get the teeth all at the right pitch AND even...so I thought I would use the milling machine.
Over the last few weeks I had been pondering how to do this...I notice that Noel Liogier uses their mill and a tiny bullnose cutter...at an angle to create waves of teeth with round bottoms...very clever. But I had a 60 deg dovetail cutter...(don't ask me why)...and I figured that should do the trick.
At first I thought I would mount the steel upright on a right-angle plate but then I had a brainwave...the mill tilts doesn't it! (homer)
I'd completely forgotten!!!
The "side" was set just forward of upright...so about 80-85 degrees...LN are 80 degrees but I think that's too forward myself..so I pulled it back a tad.
It was a slow start...but as I became more confident I could speed up so it went quite quickly after that.
The stock is 60 mm wide...3mm thick so this will make two floats...
I am in the process of making a precision "RAS"...using a Proxxon drill and some neat cutters...which would have made the cutting job a breeze...but since it isn't ready yet...I had to resort to the old hacksaw....
...a long job...this stuff is pretty thick...good job I didn't choose 5mm!
Then to cut the tang...
I use a lot of box...and burr oak...mahogany...so I needed to get some offcuts to test...and chose a piece of boxwood...seemed tough enough...
Just did two opposing faces...to get an idea of the flatness...the smoothness and the crispness of interface...
...yup...I'm happy with that...and thanks to Philly for telling me to test it BEFORE I hardened it...(just in case!). Cheers Phil!! 8)
So...now to stamp it with the KT mark...using old hammer stamps...(yes bootfair!)....
Done.....
OH...sorry...the letters are a bit off square...you get this when you are working a manual process as I was trying to line up the "T" with the grain of the steel.....all the best makers do this ya know...ask CLIFTON!! :wink:
So...to the handles...
Any preferences guys?
Toby...this just needs hardening now..so I should get the kiln fired up this week and then I am going to put a bluing on it to protect the steel...
Oh...and sharpen it of course!
I'll leave you to make one of your superb hawthorn handles for it...
Enjoy... :wink:
Jimi
So having absolutely no idea where to start...a few more head scratchings and observations of other fine tools lead me to make one...for Toby...a request...and by chance one for me too! (how clever was that!! :wink: )
Steel....O1...of course...3mm ground gauge plate...
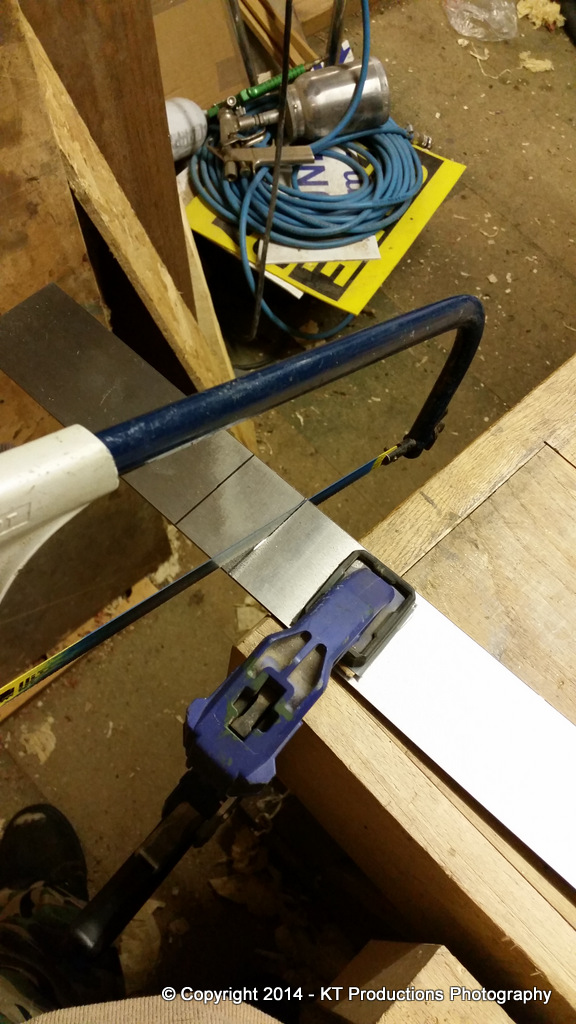
Toby requested 6 1/2" of tooth area and a total length of 8" so that's the dimensions. In retrospect...and if I ever make another..I should have cut it a few inches longer, leaving enough steel to use as hold-down space...but it worked out ok...
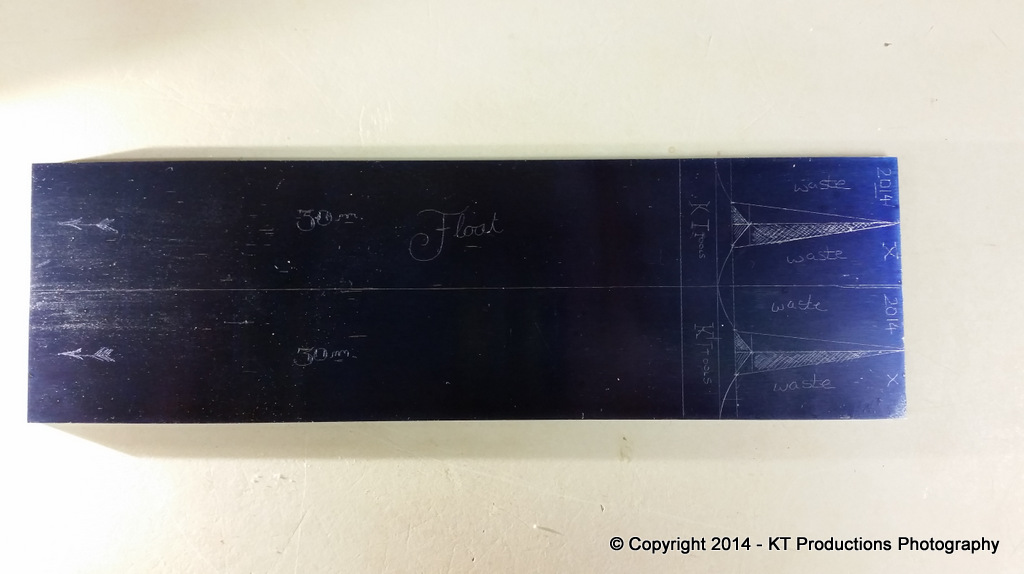
Handle was to be a tanged version as opposed to scales...so that was marked up too using a chisel as a template.
Now...this is where the pondering starts...I suppose it would have been nice to cut the teeth all by hand or employ piskies to do it for me...but I have long since lost interest in the magic of repetitive tasks like this with hand tools...and there is no way I have the skills to get the teeth all at the right pitch AND even...so I thought I would use the milling machine.
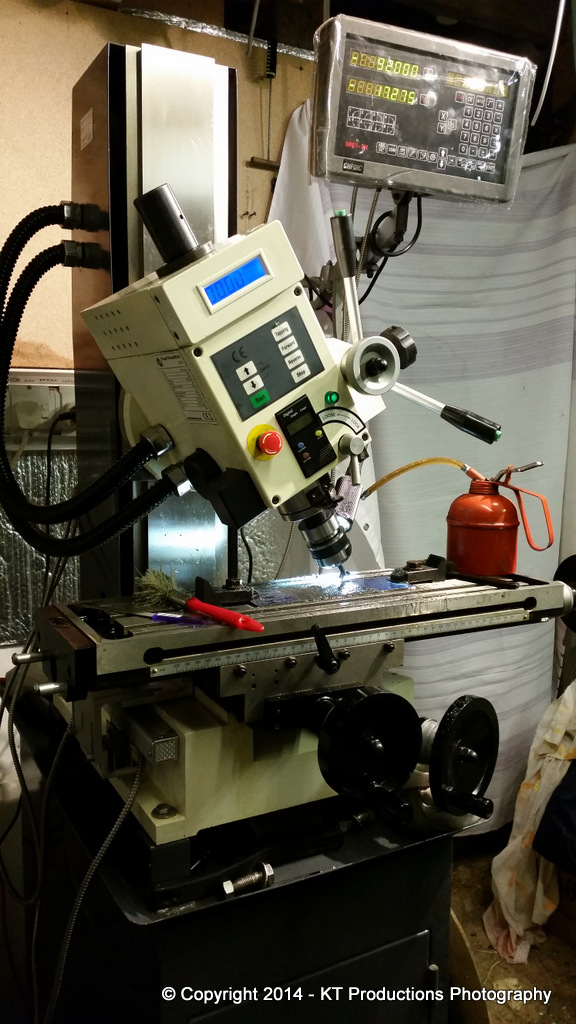
Over the last few weeks I had been pondering how to do this...I notice that Noel Liogier uses their mill and a tiny bullnose cutter...at an angle to create waves of teeth with round bottoms...very clever. But I had a 60 deg dovetail cutter...(don't ask me why)...and I figured that should do the trick.
At first I thought I would mount the steel upright on a right-angle plate but then I had a brainwave...the mill tilts doesn't it! (homer)
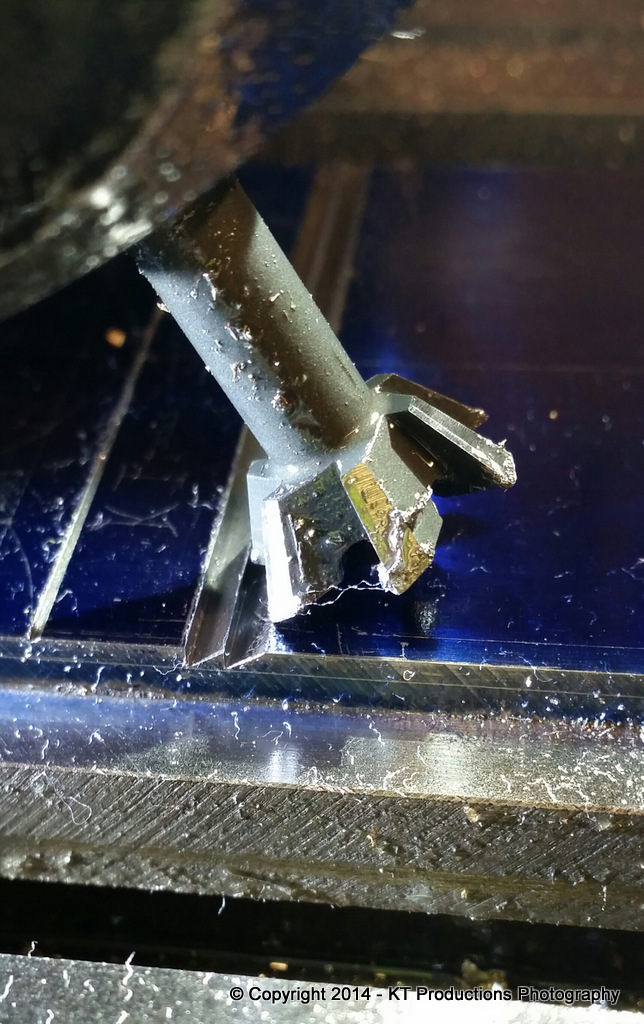
I'd completely forgotten!!!
The "side" was set just forward of upright...so about 80-85 degrees...LN are 80 degrees but I think that's too forward myself..so I pulled it back a tad.
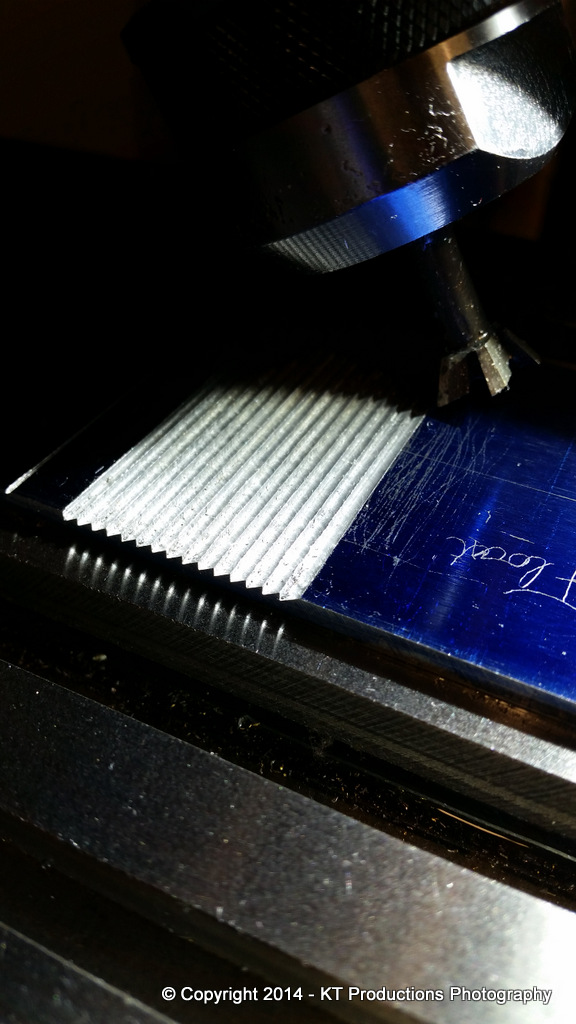
It was a slow start...but as I became more confident I could speed up so it went quite quickly after that.
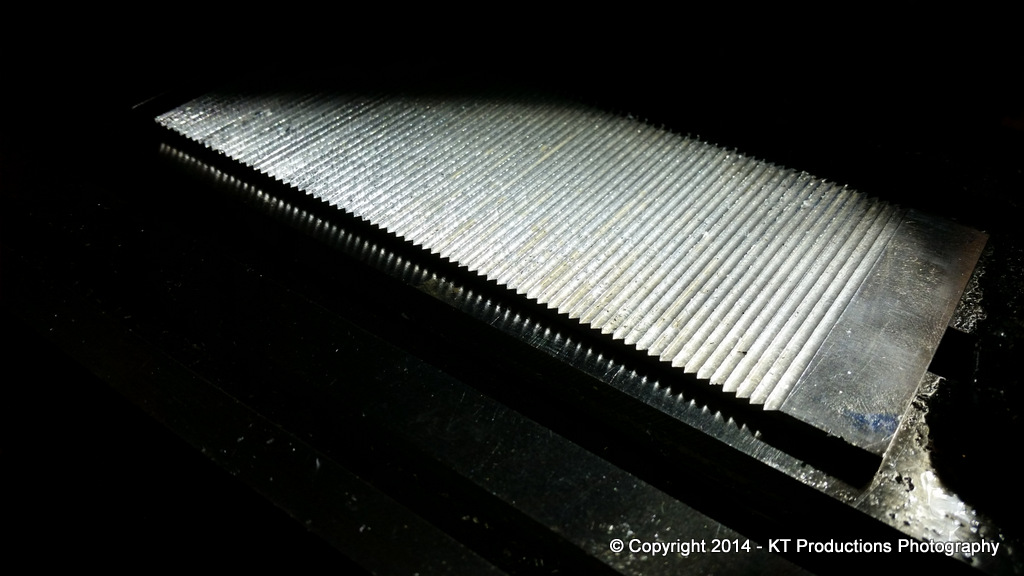
The stock is 60 mm wide...3mm thick so this will make two floats...
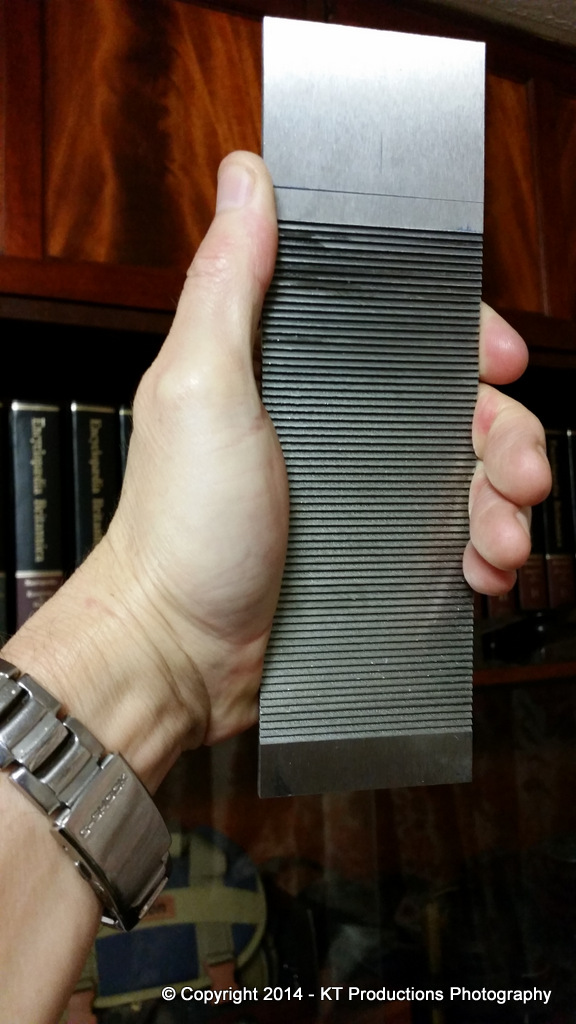
I am in the process of making a precision "RAS"...using a Proxxon drill and some neat cutters...which would have made the cutting job a breeze...but since it isn't ready yet...I had to resort to the old hacksaw....
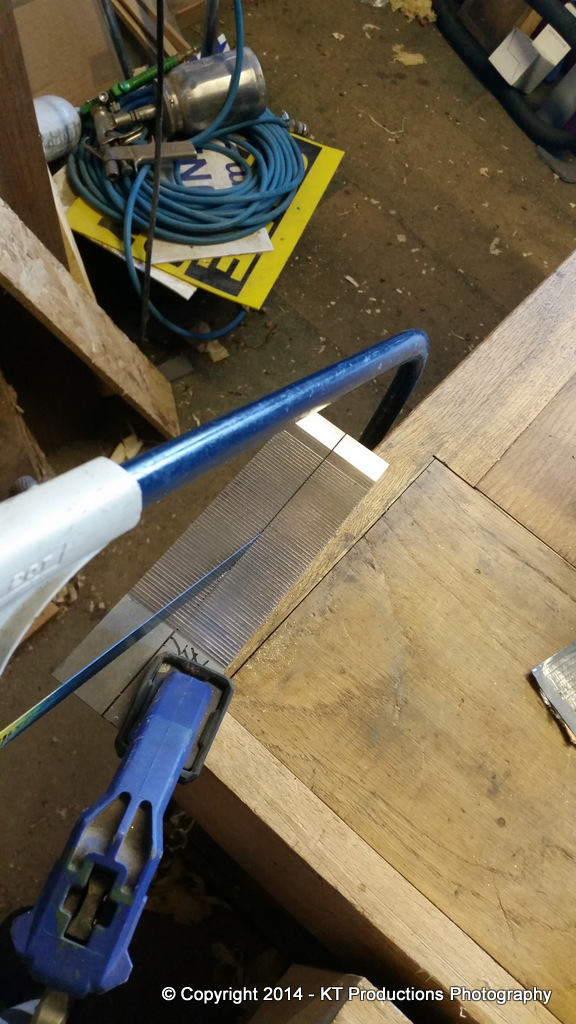
...a long job...this stuff is pretty thick...good job I didn't choose 5mm!
Then to cut the tang...
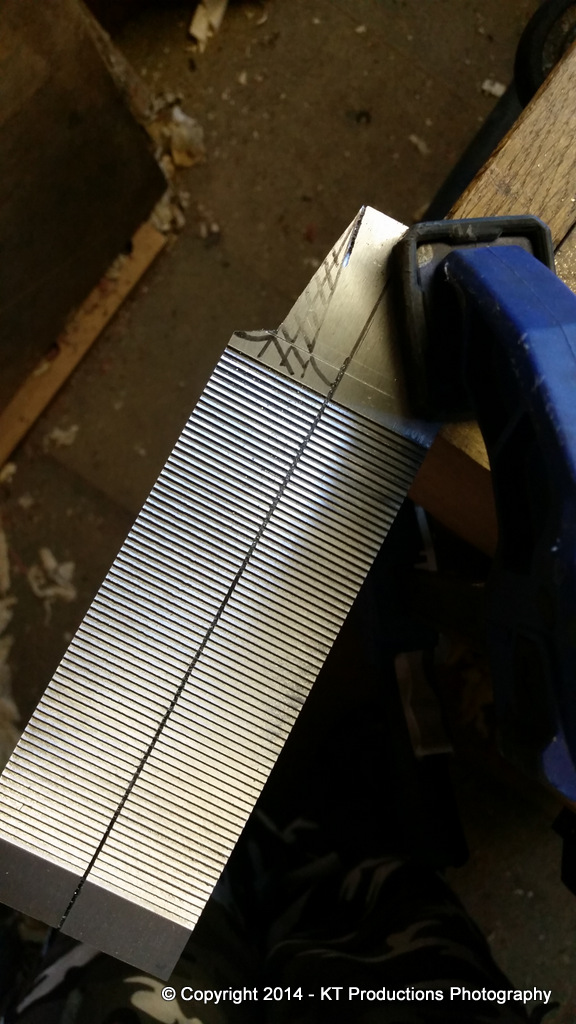
I use a lot of box...and burr oak...mahogany...so I needed to get some offcuts to test...and chose a piece of boxwood...seemed tough enough...
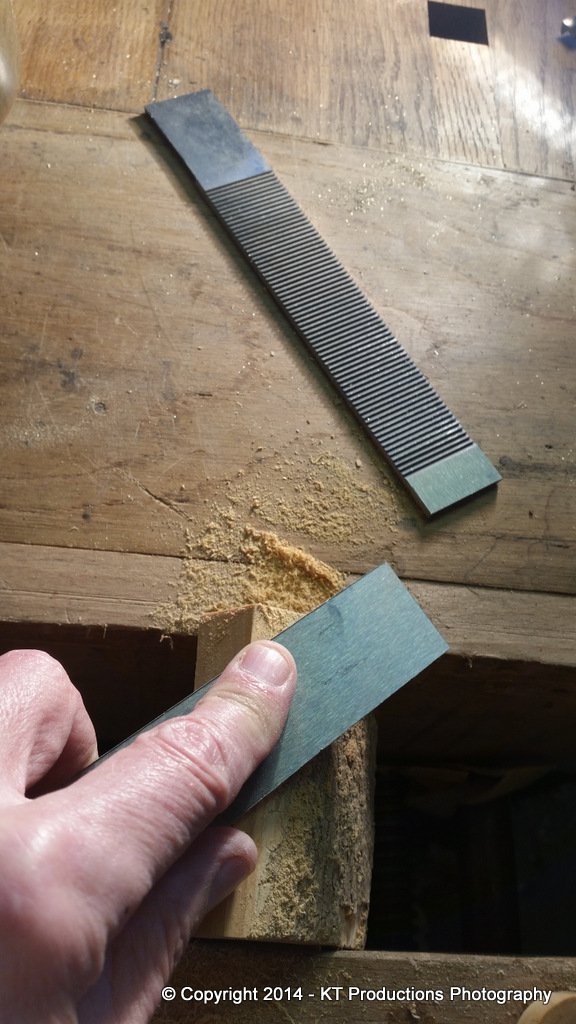
Just did two opposing faces...to get an idea of the flatness...the smoothness and the crispness of interface...
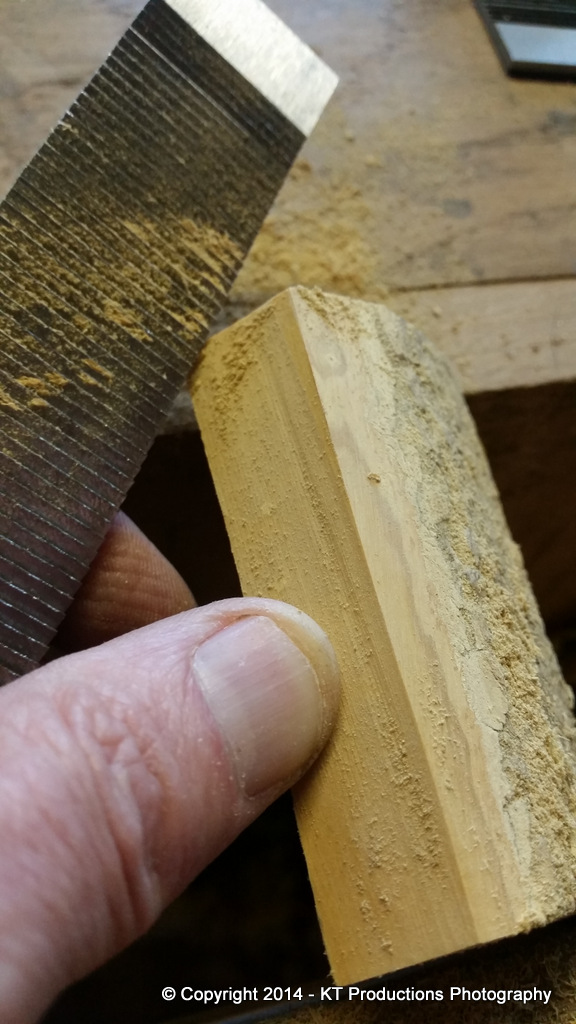
...yup...I'm happy with that...and thanks to Philly for telling me to test it BEFORE I hardened it...(just in case!). Cheers Phil!! 8)
So...now to stamp it with the KT mark...using old hammer stamps...(yes bootfair!)....
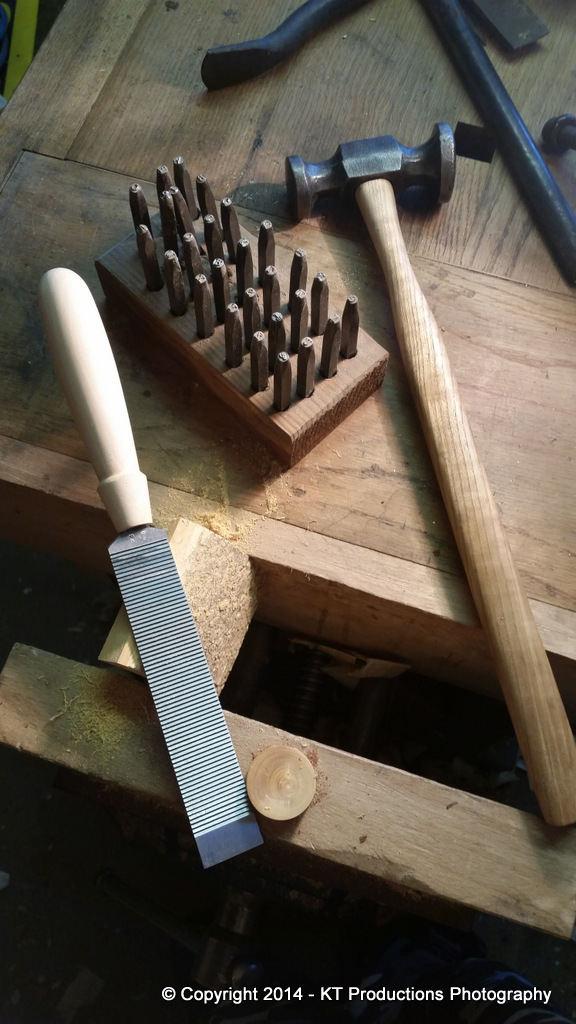
Done.....
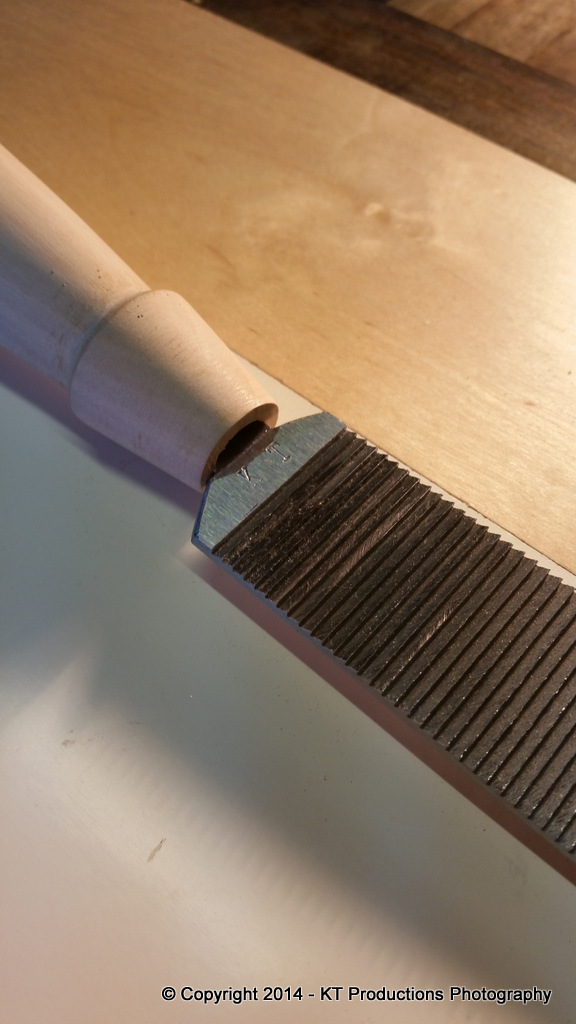
OH...sorry...the letters are a bit off square...you get this when you are working a manual process as I was trying to line up the "T" with the grain of the steel.....all the best makers do this ya know...ask CLIFTON!! :wink:
So...to the handles...
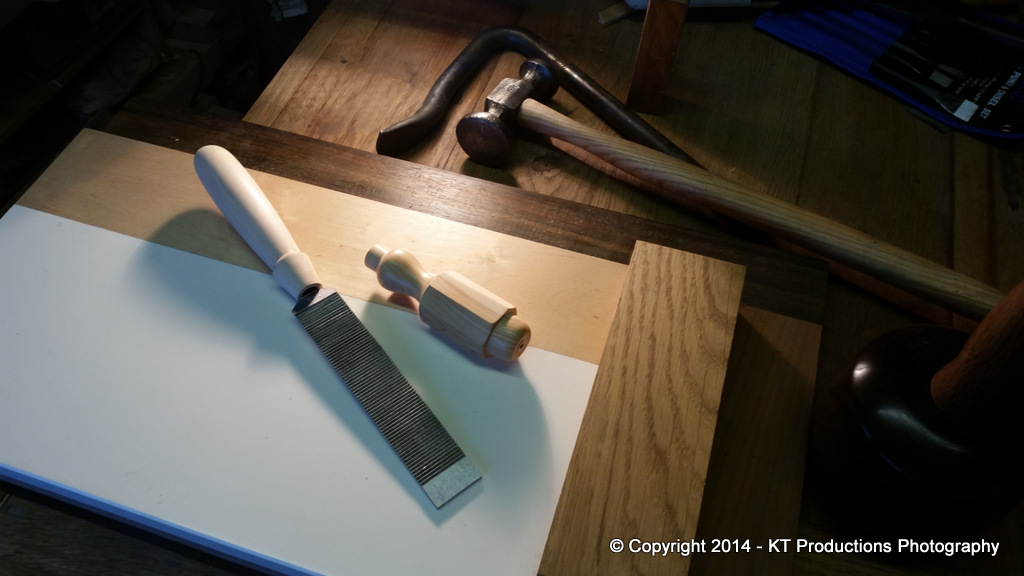
Any preferences guys?
Toby...this just needs hardening now..so I should get the kiln fired up this week and then I am going to put a bluing on it to protect the steel...
Oh...and sharpen it of course!
I'll leave you to make one of your superb hawthorn handles for it...
Enjoy... :wink:
Jimi