jimi43
Established Member
Hello good friends.....
Over the last few months I have been hard pushed to keep a secret that only a handful of people have shared but today I can thankfully spill the beans!
Those of you who know our fellow Member and Gentleman of this Parish and budding Roy Underhill impersonator...Richard T, will know of his amazing skill with metal and all things huge. :mrgreen:
Well today...a rather large and heavy package arrived via the Royal Mail...and I had quite forgotten about it (even though he told me only yesterday!
)....and so it was still a surprise.
Inside the package was hidden a gorgeous lump of steel which he has spent many moons fashioning into this masterpiece!!!!
Richard has been tinkering with infills for a while now and recently announced to me that he wished me to have a carcass so that I may fill it in...a bit like Planemaking By Numbers really! :mrgreen:
I have previously been known to tinker with the "black stuff"...but I would be about 200 years old... practising every day of the week...before I even approached the skill level of our mate Richard.
The canny amongst you will also notice that I have carefully arranged this beauty on top and in front of some wood!
This morning I accidentally went and saw "Bob" of Timberline fame....and found the largest lumps of English Boxwood he had in stock...
I'm not sure that, even then, they are going to be big enough for the handle...it depends on how they cut. If not...then it's Plan B...the large lump of English Walnut on which this monster rests. This was donated to me by Douglas...and the jury's out as to whether I go light or dark...but this may be decided for me as I said!
Richard remarked to me in a PM recently that the top was shaped...in the form of a Japanese wave...and as you can see....
...this is beautifully shaped and continues through eye-catching curves which Rubens would be proud of!
The "frog" must have taken more than a little blood, sweat and tears to shape...
It is perfectly aligned to merge with the slope of the rear mouth bevel...and should provide rock hard support for the iron once set.
You can see just how huge this lump is by looking down the plane from the inside....
The slope leads to a perfectly formed mouth...
....this is going to cut like a dream!
But it you truly want to see how much of a master craftsman Richard is...you need to try to find the dovetails...
I had to used light at exactly the right angle of incidence and use a polarising filter just to get this shot....
So there you have it...Richard's contribution to the UKW Infill Project and I'm sure that Richard will be along soon to describe in detail a summary of how he has got this far...
Meanwhile..I need to practice a bit with the lathe after making a dummy screw to test aspects of screwcap knob making....
This one's a teenie bit small and very much "Holteyesque" so I need to come up with a KT Tool design...and a MUCH large rod of brass!! :mrgreen:
I'm really looking forward to finishing this plane...I only hope that I can do justice to the work that Richard has done so far! =D> =D>
Well done my friend....simply brilliant!
Jim
Over the last few months I have been hard pushed to keep a secret that only a handful of people have shared but today I can thankfully spill the beans!
Those of you who know our fellow Member and Gentleman of this Parish and budding Roy Underhill impersonator...Richard T, will know of his amazing skill with metal and all things huge. :mrgreen:
Well today...a rather large and heavy package arrived via the Royal Mail...and I had quite forgotten about it (even though he told me only yesterday!
Inside the package was hidden a gorgeous lump of steel which he has spent many moons fashioning into this masterpiece!!!!
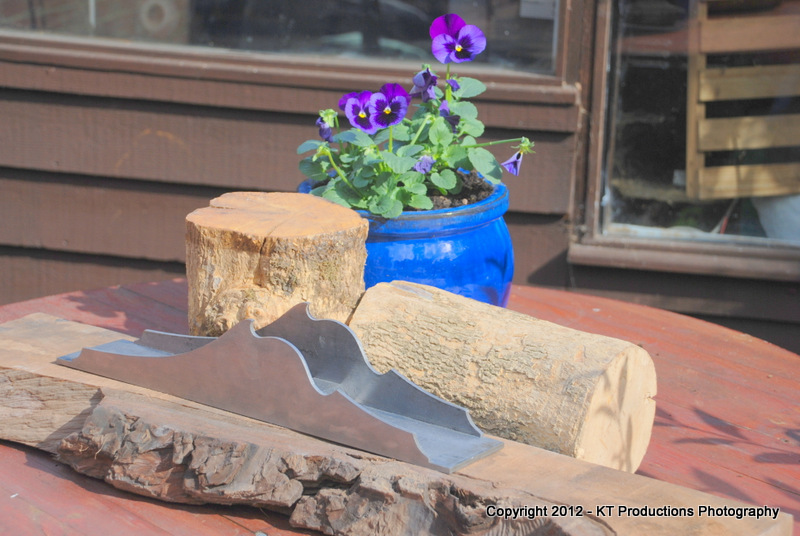
Richard has been tinkering with infills for a while now and recently announced to me that he wished me to have a carcass so that I may fill it in...a bit like Planemaking By Numbers really! :mrgreen:
I have previously been known to tinker with the "black stuff"...but I would be about 200 years old... practising every day of the week...before I even approached the skill level of our mate Richard.
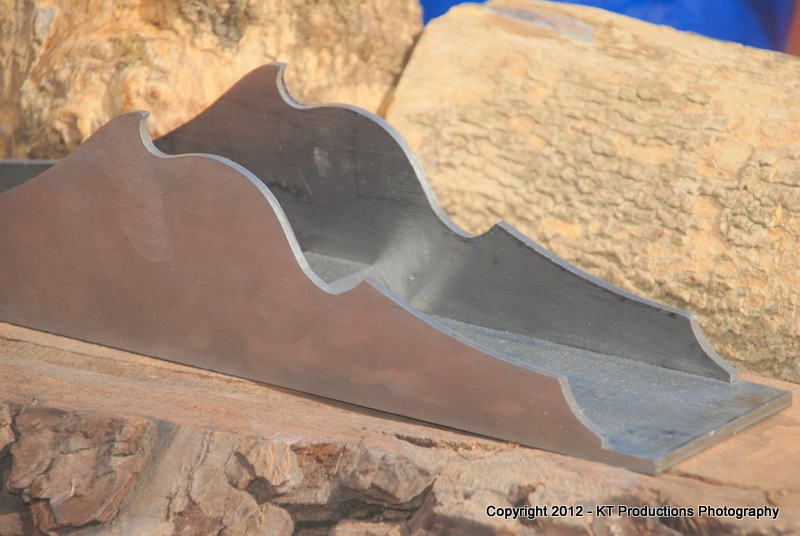
The canny amongst you will also notice that I have carefully arranged this beauty on top and in front of some wood!
This morning I accidentally went and saw "Bob" of Timberline fame....and found the largest lumps of English Boxwood he had in stock...
I'm not sure that, even then, they are going to be big enough for the handle...it depends on how they cut. If not...then it's Plan B...the large lump of English Walnut on which this monster rests. This was donated to me by Douglas...and the jury's out as to whether I go light or dark...but this may be decided for me as I said!
Richard remarked to me in a PM recently that the top was shaped...in the form of a Japanese wave...and as you can see....
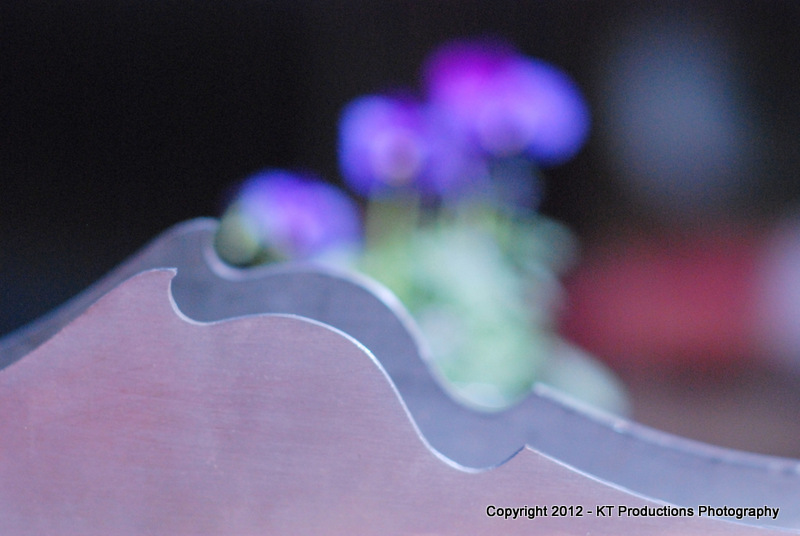
...this is beautifully shaped and continues through eye-catching curves which Rubens would be proud of!
The "frog" must have taken more than a little blood, sweat and tears to shape...
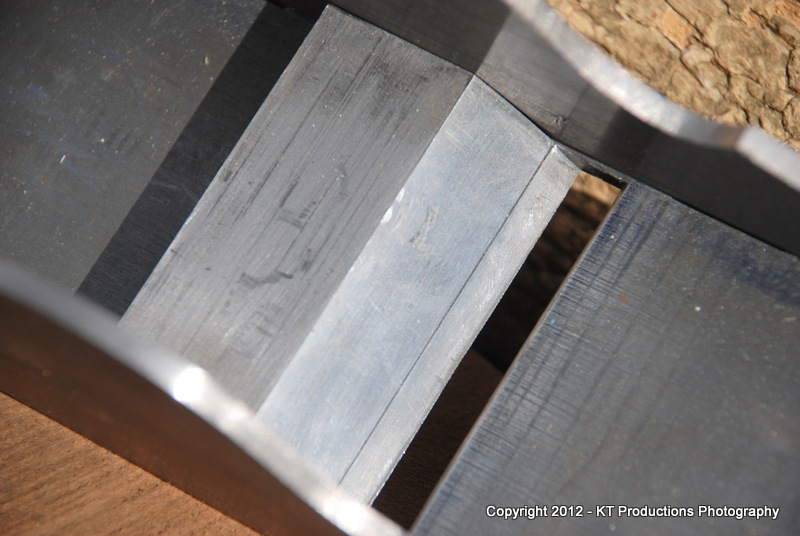
It is perfectly aligned to merge with the slope of the rear mouth bevel...and should provide rock hard support for the iron once set.
You can see just how huge this lump is by looking down the plane from the inside....
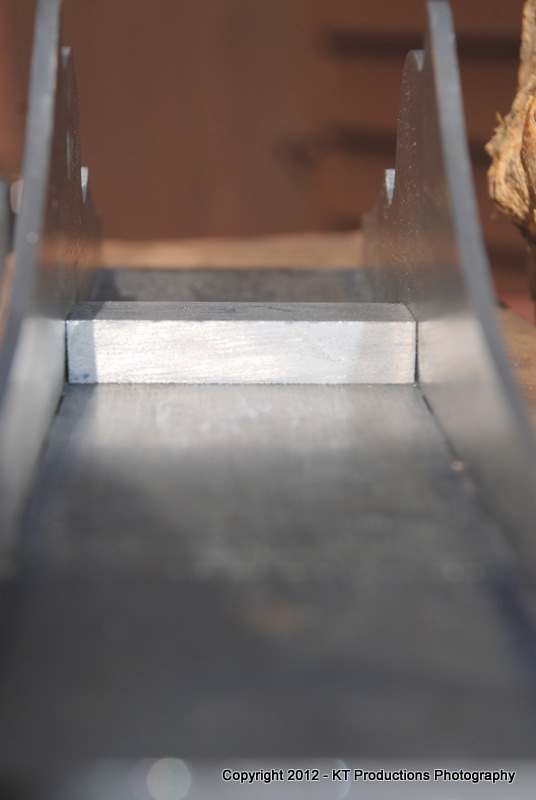
The slope leads to a perfectly formed mouth...
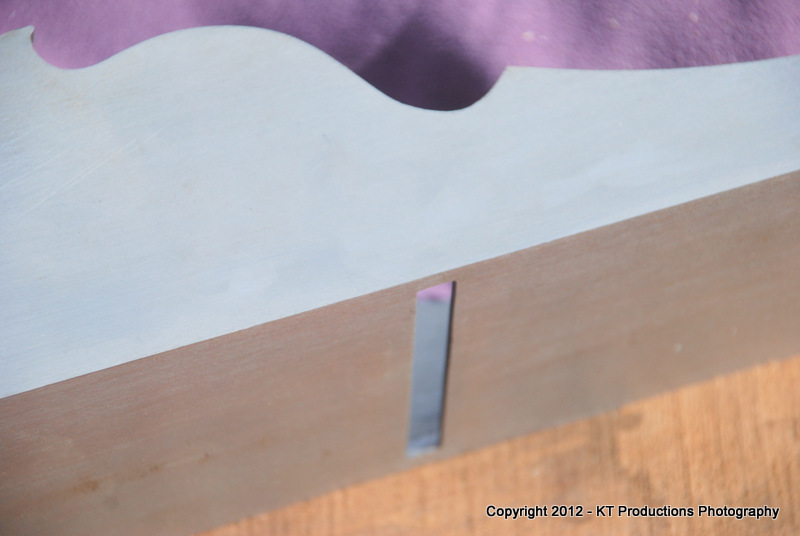
....this is going to cut like a dream!
But it you truly want to see how much of a master craftsman Richard is...you need to try to find the dovetails...
I had to used light at exactly the right angle of incidence and use a polarising filter just to get this shot....
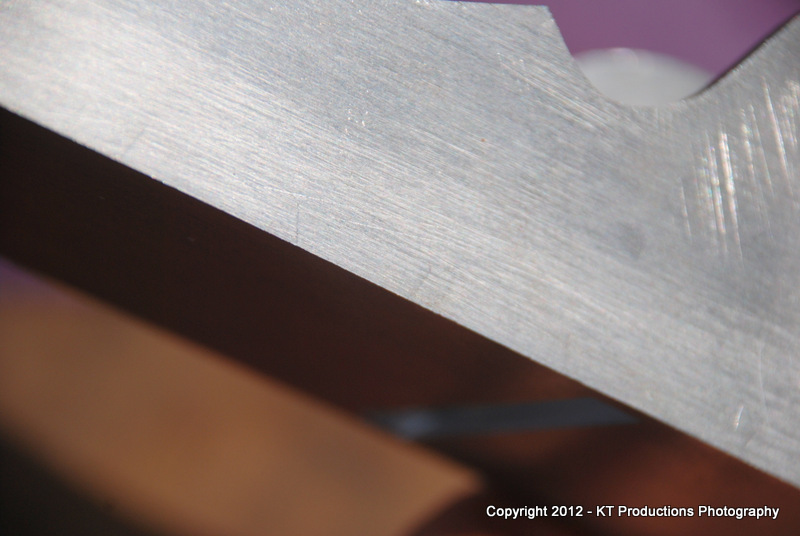
So there you have it...Richard's contribution to the UKW Infill Project and I'm sure that Richard will be along soon to describe in detail a summary of how he has got this far...
Meanwhile..I need to practice a bit with the lathe after making a dummy screw to test aspects of screwcap knob making....
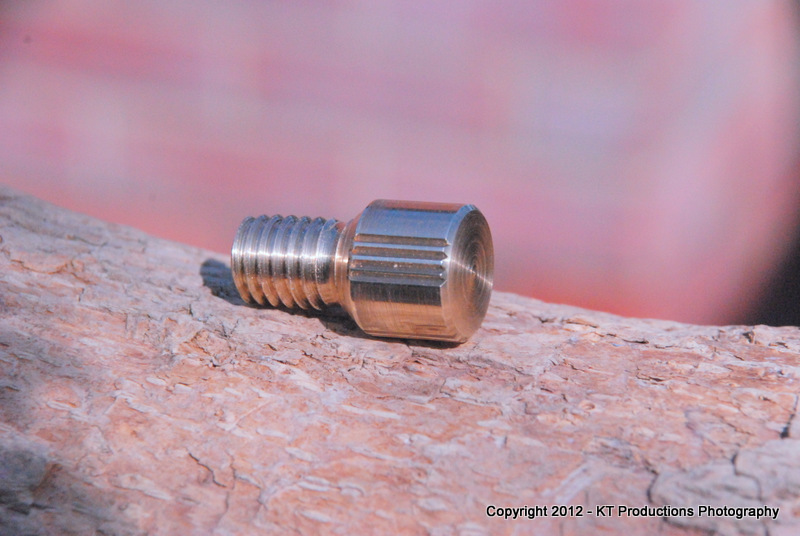
This one's a teenie bit small and very much "Holteyesque" so I need to come up with a KT Tool design...and a MUCH large rod of brass!! :mrgreen:
I'm really looking forward to finishing this plane...I only hope that I can do justice to the work that Richard has done so far! =D> =D>
Well done my friend....simply brilliant!
Jim