jimi43
Established Member
Hi Guys....not sure if this is the right forum as I don't post very often but thought you would be interested in this little gem I picked up recently.
I acquired this Swiss made "INCA" table saw the other week at a bootfair and it was in a pretty awful (and dangerous) state:
The above picture was from eBay of the actual saw where the guy was trying (and failing) to sell it.
A little research told me this was an INCA 59 saw and was quite sought after...particularly in the USA.
There was extensive but not deep rust on a lot of parts...particularly the stand and so a respray was the only way to go...
The old Gryphon motor worked fine but again was really rusty...
The wiring was particularly bad with totally perished rubber "insulation" which wasn't!!
How the guy didn't electrocute himself simply amazes me!
Anyway....a little stripping down and polishing...rust neutralising and painting and she now rocks and rolls....OH...and I replaced the wiring!!
The colour matching was more towards the INCA green than the "Startrite" metalic green....since I couldn't get this colour...it is "FORD FOREST GREEN"...
The motor was not an INCA one so that became enamel blue...just for a bit of contrast...
The cast aluminium bed needed complete sanding down through the grades and came out quite well...it had some deep gouges..
I cleaned the main bed up and left it basically untouched...there was some paint flaking in some places...but not many...
I need to get a new blade as the one in it was quite rusty and had one tooth of the TCTs missing...I didn't really want any more coming off at a few thousand revs! I need to source one with a 15mm arbour...160mm...not sure where I will find one of them in the UK!!
Any comments...help...advice or anyone with knowledge of this gem...gratefully received...
Cheers guys
Jim
I acquired this Swiss made "INCA" table saw the other week at a bootfair and it was in a pretty awful (and dangerous) state:
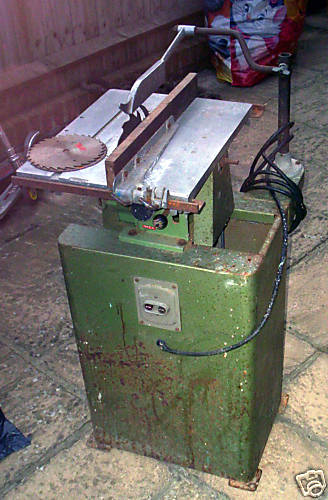
The above picture was from eBay of the actual saw where the guy was trying (and failing) to sell it.
A little research told me this was an INCA 59 saw and was quite sought after...particularly in the USA.
There was extensive but not deep rust on a lot of parts...particularly the stand and so a respray was the only way to go...
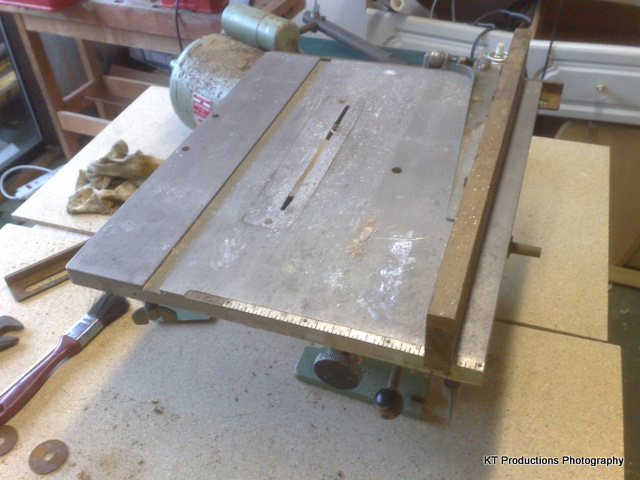
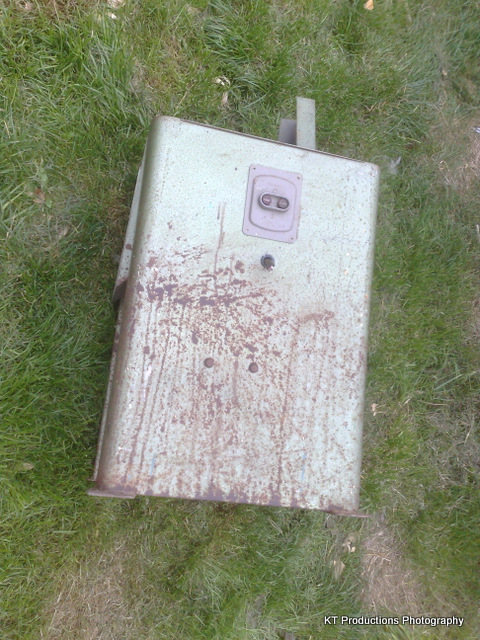
The old Gryphon motor worked fine but again was really rusty...
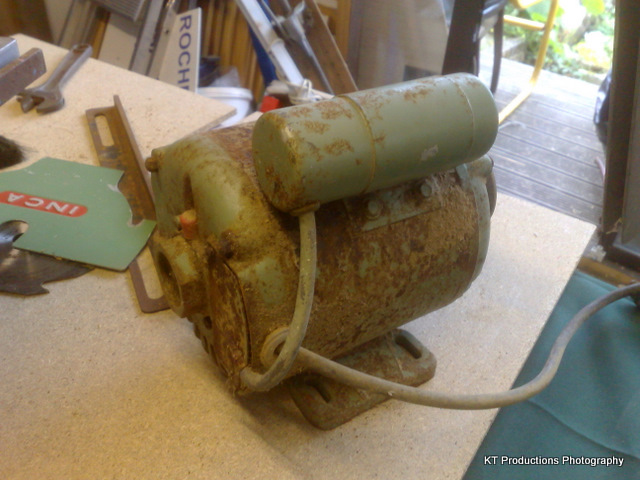
The wiring was particularly bad with totally perished rubber "insulation" which wasn't!!
How the guy didn't electrocute himself simply amazes me!
Anyway....a little stripping down and polishing...rust neutralising and painting and she now rocks and rolls....OH...and I replaced the wiring!!
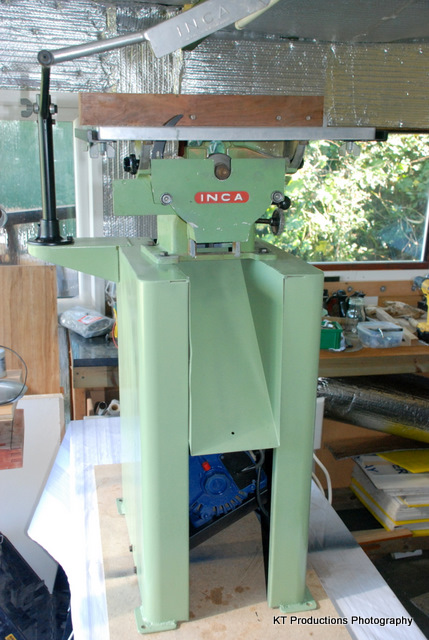
The colour matching was more towards the INCA green than the "Startrite" metalic green....since I couldn't get this colour...it is "FORD FOREST GREEN"...
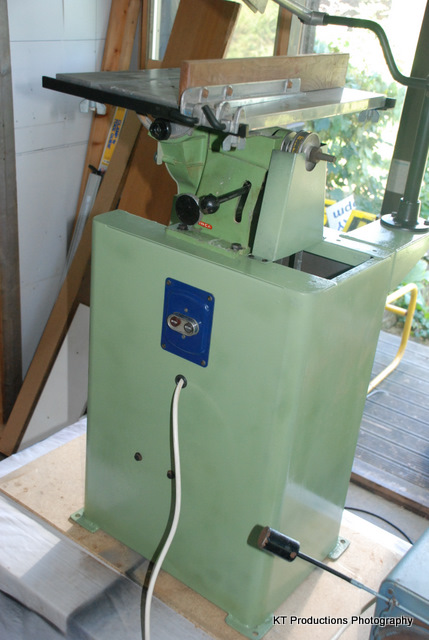
The motor was not an INCA one so that became enamel blue...just for a bit of contrast...
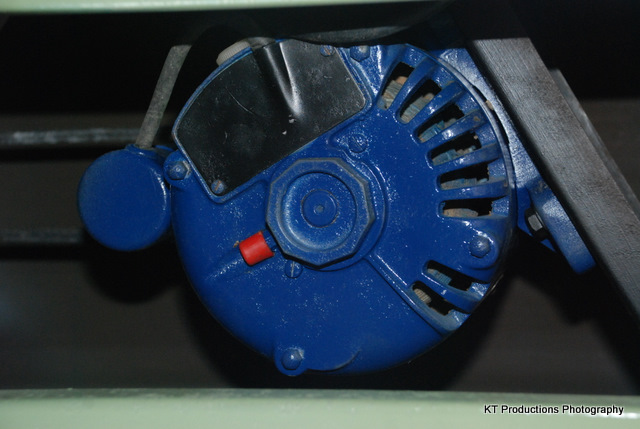
The cast aluminium bed needed complete sanding down through the grades and came out quite well...it had some deep gouges..
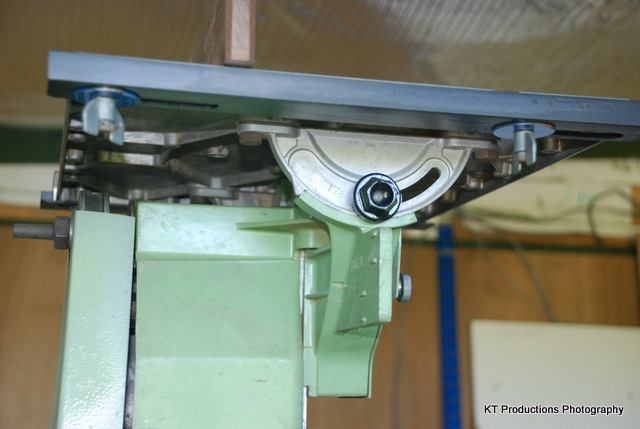
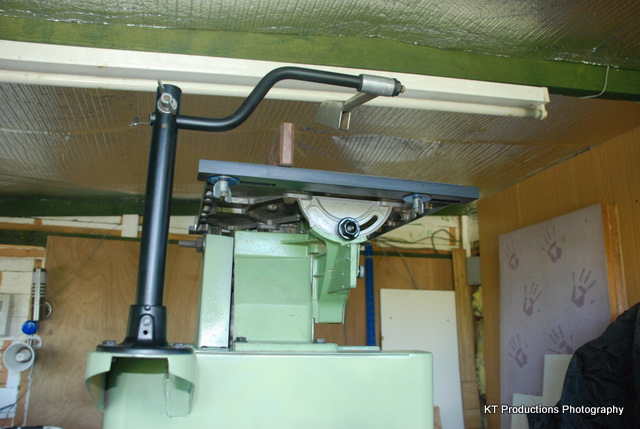
I cleaned the main bed up and left it basically untouched...there was some paint flaking in some places...but not many...
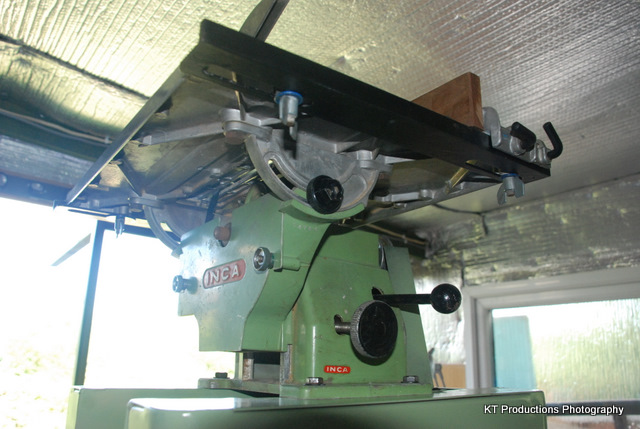
I need to get a new blade as the one in it was quite rusty and had one tooth of the TCTs missing...I didn't really want any more coming off at a few thousand revs! I need to source one with a 15mm arbour...160mm...not sure where I will find one of them in the UK!!
Any comments...help...advice or anyone with knowledge of this gem...gratefully received...
Cheers guys
Jim